
3、 放电等离子烧结(SPS):SPS 技术是一种受到学术界广泛关注与研究的新型快速烧结技术,图3为
其工作原理示意图。SPS技术开创性地将直流脉冲电流引入烧结过程,压头在向材料施加压力的同时也充
当电流通过的载体。与传统烧结技术通常利用发热体辐射加热不同,SPS 技术借助大电流通过模具或导
电样品产生的热效应来加热材料。对于绝缘样品,通常使用导电性良好的石墨作为模具材料,利用模具
的电阻热使样品快速升温; 对于导电样品,则可以使用绝缘模具,使电流直接通过样品进行加热。其升
温速率可达1000℃/min,当样品温度达到设定值后,经过短时间保温即可完成烧结。
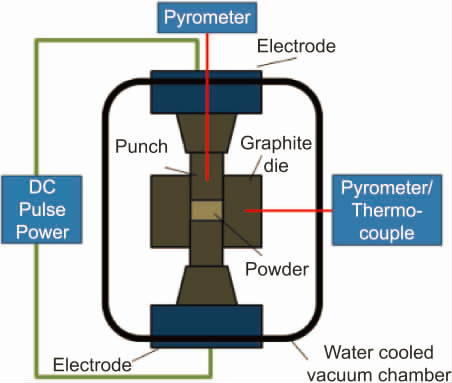
图3 SPS 设备的工作原理示意图 1)SPS 技术具有烧结温度低、保温时间短、升温速率快、烧结压力可调控、可实现多场耦合(电-力-
热) 等突出的优点。除Al2O3、ZrO2等常见陶瓷外,SPS 技术也可用于许多难烧结材料的制备,如
ZrB2、HfB2、ZrC、TiN等超高温陶瓷以及W,Re,Ta,Mo 等难熔金属及其合金。
2)通过使用阶梯状等经过特殊设计的模具改变流经模具的电流密度,可人为地在样品中制造温度梯
度,因此SPS 技术还可以用于制备功能梯度材料。此外,纳米晶透明陶瓷、介电陶瓷等功能材料也可利
用 SPS 技术制进行烧结。
4、闪烧( FS):FS 技术于2010 年由科罗拉多大学的Cologna 等首次报道,其来源于对电场辅助烧结技
术(field-assisted sinteringtechnology,FAST) 的研究。图4a 是一种典型的FS装置示意图,待烧结
陶瓷素坯被制成“骨头状”,两端通过铂丝悬挂在经过改造的炉体内,向材料施加一定的直流或交流电
场。炉体内有热电偶用于测温,底部有CCD相机可实时记录样品尺寸。以3YSZ为例研究人员发现与传统
烧结相比,若在炉体内以恒定速率升温时,对其施加20V/cm 的直流电场场强,可在一定程度上提高烧
结速率,降低烧结所需的炉温,如图4b所示。随着场强的增强,烧结所需炉温持续降低。
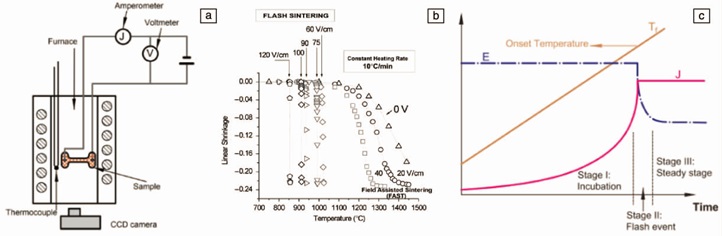
图4 FS 装置示意图(a) ,直流电场对3YSZ 烧结速率的影响(b),FS过程中各参数变化趋势(c)
1)当场强为60V/cm 时,样品会在炉温升高至约1025℃时瞬间致密化; 当场强提高至120V/cm 时,烧结
炉温甚至可以降低至850℃。这一全新的烧结技术被称为“闪烧”,即在一定温度和电场作用下实现材
料低温极速烧结的新型烧结技术。
2)通常有如下3个现象会伴随FS 发生: ① 材料内部的热失控; ② 材料本身电阻率的突降; ③ 强烈的
闪光现象。
3)FS 技术主要涉及3个工艺参数,即炉温(Tf)、场强(E)与电流(J)。图4c为传统FS过程各参数变化趋
势图。
4)在这一模式下,对材料施加稳定的电场,炉温则以恒定速率升高。当炉温较低时材料电阻率较高,
流经材料的电流很小。
5)随着炉温的升高,样品电阻率降低,电流逐渐增大。这阶段称为孕育阶段(incubationstage) ,系
统为电压控制。
(1)当炉温升高至临界温度时,材料电阻率突降,电流骤升,FS 发生。由于此时场强仍稳定,因此系
统功率(W = EJ) 将快速达到电源的功率上限,系统由电压控制转变为电流控制,这一阶段称为FS阶段
(flash sintering stage) 。
(2)当材料电阻率不再升高时,场强再次稳定,烧结进入稳定阶段(steady stage) ,即FS的保温阶
段,保温阶段之后一次完整的FS 过程结束。
6)与传统烧结相比,FS主要有以下优势: 缩短烧结时间并降低烧结所需炉温,抑制晶粒生长,能实现
非平衡烧结,设备简单,成本较低。
5、 冷烧结(CS)
1)为使陶瓷材料的密度达到其理论密度的95%以上,陶瓷材料烧结温度需达到其熔化温度的50%~75%。
因此,大多数陶瓷材料的烧结温度大于1000℃,使得陶瓷材料的生产过程需要消耗较多的能源,且高温
烧结使得陶瓷材料在材料合成、物相稳定性等方面受到了限制。
2)为了降低陶瓷粉体的烧结致密化温度,液相烧结、场辅助烧结、FS 等新型烧结技术被应用,但是由
于固相扩散以及液相形成仍需较高温度加热陶瓷粉体,上述技术并没将烧结温度降低到“低温范畴”。
3)近期美国宾西法尼亚州立大学 andall课题组受水热辅助热压工艺启发,提出一种陶瓷CS 工艺新
技术;与传统的高温烧结工艺不同,陶瓷CS工艺通过向粉体中添加一种瞬时溶剂并施加较大压力(350~
500 MPa) 从而增强颗粒间的重排和扩散,使陶瓷粉体在较低的温度(120 ~ 300℃) 和较短的时间下实
现烧结致密化,为低温烧结制造高性能结构陶瓷和功能陶瓷创造了可能。

|