目前国内外利用酯交换法制备生物柴油生产技术主要有碱催化法、酸催化法、酶催化法、无催化剂超临界反应和超声波强化反应等。酸催化交换过程产率较高,但反应速率慢,分离难,易产生三废,比较适合酸价高和含水杂的低级油脂;碱催化法反应速率较快,但不适用于低级油脂;酶催化法环保率低、成本高,原料适应性差;超临界法,催化剂用量少,产率较高,但设备要求高、能耗高。 本项目系统研究了超声空化、碱催化制备生物柴油新技术,发现反应时间可缩短至10小时(转化率近100%),说明超声空化能加速油脂一醇非均相反应进程,但是超声空化技术存在难于规模化的缺点;国内对普通碱催化制备生物柴油技术有一定的积累,也有小规格试生产,但急需在制备工艺的原料广泛适应性(如利用废弃油脂、高酸价油脂等)、反应过程强化与降低提纯过程能耗方面取得突破;研究结果表明水力空化能够极大地缩短生物柴油反应时间,提高转化率,降低能耗及生产成本。
1、工艺技术路线
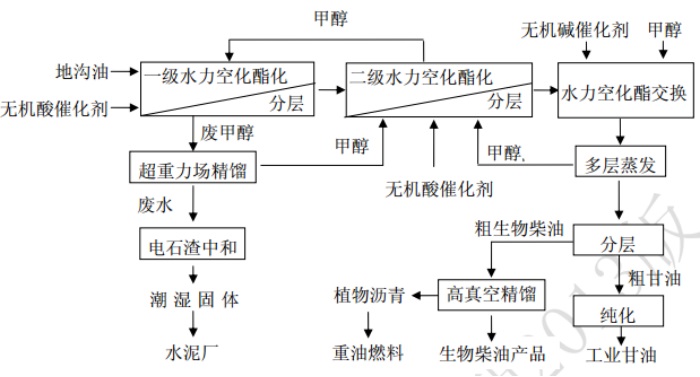
2、关键技术
(1)沟油预处理技术:地沟油作为原料油生产生物柴油在成本上有着明显优势,但需要较高的加工工艺技术;其主要原因是地沟油中含有较多的杂质和游离脂肪酸,酸价高,颜色重,尤其是高酸值极大地阻碍酯交换反应的进行;因此地沟油的预处理就成了必要的步骤;尤其为了防止酯交换时发生皂化,预处理工艺中降低酸值是要解决的关键问题;本项目通过研究地沟油预处理的最佳工艺路线,并确定其各个步骤的参数;对于最主要的酯化降酸,采用无水硫酸铁为催化剂,通过单因素和正交试验考察醇油摩尔比、反应时间、反应温度和催化剂用量对预处理酯化降酸效果的影响,在为后续酯交换反应提供优质原料油的同时,有效降低酯交换反应时间,提高生物柴油制品品质。
(2)水力空化作为生物柴油制备过程的强化技术:本关键技术采用水力空化乳化新技术解决接触面问题。现有的酯交换技术中甲醇和动、植物油的互溶性差,反应体系成两相,酯基的转化主要在界面完成,反应速度低。采用动态超声乳化技术可以将油脂分散呈微米甚至纳米级的颗粒,呈数量级地增加两相的接触面积,使酯交换反应在短时间内达到平衡。采用搅拌结合水力空化强化反应技术,可使生产设备和能耗比现有的搅拌碱催化技术分别缩小5倍和降低10%。
(3)多层蒸发技术脱除粗生物柴油中的甲醇和微量水分:生物柴油沸点高于350℃,从沸点上讲很容易脱除甲醇和水分;但是在不沸腾的条件下,甲醇和水分子从内部扩散到蒸发面需要很长时间;在传统的蒸发釜中需要数小时才能除尽甲醇和水分,生物柴油长时间受热导致部分分解;针对这个问题,开发了多层蒸发器,在其内部设置了多层蒸发盘,每一层上有加热管,盘上液层高度100毫米(釜式蒸发器液层高2米),液体在盘上平推流流动,逐盘向下流动,流出最后一盘时甲醇和水已经除尽;多层蒸发器的优点是浅液层汽化,降低了汽化温度;液体不返混,停留时间均匀,效率高;设备内持液量小,停留时间短,液体从进到出15分钟即可完成任务;连续操作,产量高; 采用多层蒸发技术使得粗生物柴油中的轻组分除尽,生物柴油不分解,且能耗有效降低。常规蒸发技术脱除甲醇和水分,时间长、能耗大,长时间加热导致生物柴油分解;自主开发的多层蒸发技术,具有浅液层汽化、加热温度低、不返混和停留时间短的优点,达到了甲醇和水分脱尽、生物柴油不分解和产量大的目标。
(4)高真空精馏技术:因原料是地沟油,粗生物柴油需精馏才能符合国家生物柴油标准;生物柴油沸点350℃左右,需在高真空下精馏;即使是高真空,塔釜和塔顶的温度仍高达240℃和170℃,热量需回收;塔釜的植物沥青几乎不汽化,而要实现精馏,塔釜必须要有物料汽化,这就导致传统的塔釜必然留有生物柴油,降低了精馏得率;为了采出植物沥青中残留的生物柴油,就得把釜残再蒸一次。采用多层蒸发器作塔釜,可解决这个问题,上面的蒸发盘提供生物柴油汽化,下面的蒸发盘把植物沥青中的生物柴油蒸干,既保证了精馏汽化的需要,又提高了精馏得率;采用组合式冷凝器,回收塔顶热量,具有热量回收效率高,同时保证生物柴油不被抽入真空泵中,结构紧凑,投资抵。
(5)粗甘油精制技术: 粗甘油的商品性较差,对正常有序的生产造成困挠。经分离得到副产品粗甘油,因生产过程的因素,在粗甘油里总存在着游离碱(pH>12),脂肪酸皂及沉降分离过程夹带的部分脂肪酸甲酯。所以副产品粗甘油在进入精甘油生产前,必须经废甲醇酸液酸化处理,使粗甘油中的游离碱被中和,脂肪酸皂分解成脂肪酸。而脂肪酸又与脂肪酸甲酯溶为一相,然后通过脱甲醇后,在沉降分离罐中进行多级重力沉降分离,下层清液酸性粗甘油去甘油车间,经氢氧化钠液碱中和脱酸后,再经真空闪蒸脱水脱低沸,然后进入甘油薄膜蒸馏;国内的成套精甘油装备还停留在50年代,效力低,能耗高,品质差;而国外装备价格很高,只能望而怯步;我们在吸收国外装备技术的基础上,结合公司实际,设计一套简捷的精甘油生产线,满足生产需要。粗甘油价格每吨2300元,工业甘油价格每吨5300元,这样就大大提高了企业生产效率和经济效益。
(6)超重力精馏回收甲醇技术: 酯化产生的酸性甲醇水溶液,需回收甲醇以循环使用。传统的办法先将酸性甲醇水溶液用碱中和,然后进入高20米的精馏塔分离,使得设备和附属设施投资大,操作不便。采用耐腐蚀的釜汽化,甲醇水汽相进入高度不足4 米的超重力精馏装置,顶上得到高于99.5%的甲醇,再沸器则为甲醇含量小于0.1%的废水;采用超重力精馏装置可降低设备和公用工程投资,方便操作,同样的处理要求,高度仅为塔设备的1/5,体积仅为1/7,极大地强化了精馏过程。
(7)三废处理技术: 地沟油预处理采用密闭式烘房,集中排气,经碱液吸收后无味放空;生产过程中各设备密闭操作,放空管中的甲醇气体经冷阱后集中放空,故无废气排放。整个生产过程中仅有的固体植物沥青,可作重油燃料。与传统工艺不同,本项目拟利用“甘油洗”代替酸洗和水洗过程,所以,整个生产过程仅为酯化反应产生的废水,其量为生物柴油量的3%左右。一级酯化产生的酸性废甲醇,经精馏后,塔釜产生的含酸废水与电石渣中和,形成无机钙盐或镁盐,少量水分经挥发后,将其送至水泥厂或砖瓦厂作原料。因此,整个生产过程无“三废”排放,做到了地沟油全利用,清洁生产。本项目中因取消了酸洗和水洗操作,废水产生量仅为生物柴油量的3%,且仅含无机酸,用电石渣中和后,作为水泥厂的原料;整个生产过程密闭,甲醇不泄漏,地沟油酸败气体经碱液吸收后无味排放;精馏产生的植物沥青作为重油燃料。
3、项目的主要技术特点和创新点分析:
创新点一:自主研发水力空化制备生物柴油的方法,采用水力空化酯交换反应器来优化生物柴油的生产,这种方法工艺简单,酯交换反应速度快,反应时间比传统反应器缩短2~3倍,油脂酯交换转化率高达99%,而且甲醇、催化剂消耗量少,能耗低,适于大规模的工业生产;地沟油中含有约30%的脂肪酸和70%的甘油三酯。脂肪酸与甲醇反应生成生物柴油(脂肪酸甲酯)和水,称为酯化反应;甘油三酯与甲醇反应生成生物柴油和甘油,称为酯交换反应。上述两步反应均为可逆反应,反应式如下所示。
a.由脂肪酸到生物柴油的反应式为: RCOOH + CH3OH = RCOOCH3 + H2O
b.由甘油三酯到生物柴油的反应式为:C3H5(RCOO)3 + 3CH3OH = RCOOCH3 + C3H5(OH)3
c.酯化反应和酯交换反应一般都需要催化剂,主要有均相酸碱催化、固体酸碱催化和酶催化,另外,高温高压法和超临界法无需催化剂。国内外已经产业化的技术中,主要采用均相酸碱催化法,其它方法还需经生产实践进一步检验;甲醇与油脂互溶性差,两者反应属于液-液非均相反应,研究表明酯化反应属于中等反应速度,两相接触面积的大小是决定反应时间的关键因素。采用传统的搅拌混合方法,甲醇在油脂中分散度低,反应两相接触面积小,反应时间长,实验室搅拌速度600rpm时,甲醇液滴粒径为3700nm,而在工业上,搅拌速度要远低于实验室,液滴更大,反应速度更慢;利用超声波产生的“超声空化”可以使甲醇与油脂产生乳化,甲醇分散性好,反应时间短;“水力空化”是利用液体通过节流元件,液体流速和压力产生激烈变化而产生空化,使得液体质点之间产生强力撞击,导致甲醇与油脂乳化,与“超声空化”有异曲同工之妙;实现“水力空化” 只需一台离心泵和一套可自行设计加工的节流元件,具有在生产上容易实现、适合大中小规模的生产、耐腐蚀、不易损坏、成本低的优点;实验室酯交换和生产中酯化反应的数据如表所示。
d.不同混合方法生产生物柴油的数据比较
混合方法 |
甲醇液滴粒径(nm) |
比表面积(m2/m3) |
实验室酯交换反应时间(h) |
工业上酯化时间(h) |
搅拌 |
3700 |
1.6×106 |
1 |
6 |
超声 |
250 |
2.4×107 |
0.25 |
/ |
水力空化 |
450 |
1.3×107 |
0.25~0.3 |
1.5 |
由表可知,水力空化混合与搅拌相比,两相接触比表面积提高了近一个数量级,反应速度提高了3~4倍。
创新点二:自主开发生物柴油酯化酯交换反应装置,酯化反应过程甲醇和水不汽化,成倍降低了能耗;甲醇循环套用,显著减少了甲醇回收的能耗;由于酯化反应具有很强的可逆性,要将水分不断除去,才能将反应进行到底。甲醇的沸点64.5℃,水的沸点100℃,蒸发脱水时,甲醇先于水沸腾,需有大量的甲醇汽化,才能带出少量的水分,蒸出的甲醇(95%)-水溶液必须再经过精馏才能循环使用,又增加了能耗。所以,传统的酯化工艺能耗大,甲醇循环用量大。
a、酯化反应过程甲醇和水不汽化,成倍降低了能耗:针对传统酯化反应能耗高的情况,本项目在60℃、常压下,采用两级酯化法,第一级酯化后,脂肪酸含量降为5%,甲醇-水相与油相静止分层,含水甲醇进超重力床回收后循环利用,油相进入第二级酯化,脂肪酸降为1%以下,分层后,甲醇相作为原料进入第一级酯化,油相进入酯交换反应,反应物进入多层蒸发脱出粗生物柴油中的甲醇和微量水,粗生物柴油与甘油分层后,进入精馏塔精制,获得生物柴油产品,甘油进一步纯化获得工业甘油。采用本项目工艺,生产1吨生物柴油少汽化600kg甲醇,相当于节约标准煤23kg。
b、甲醇循环套用,显著减少了甲醇回收的能耗:第一级酯化的甲醇来自第二级酯化,第二级酯化的甲醇来自多层蒸发和超重力场,新鲜的甲醇进入酯交换反应;需要精馏回收的甲醇水溶液仅仅来自第一级酯化。1吨生物柴油少回收甲醇500kg,节约标准煤20kg,以年产1万吨生物柴油计算,仅此一项可节约标准煤430吨。
创新点三:自主开发的多层蒸发的生物柴油连续精馏系统和工艺,能维持较高的真空度,提高产能,降低能耗,提高产品的收率;并最大程度上消除因停留时间过长造成的高温分解和聚合,提高生物柴油精馏得率,较釜式再沸器提高10%以上;通过组合冷凝器和产品-原料换热器,回收高温生物柴油产品的冷凝潜热和显热,极大的降低能耗,节能50%以上;工业生物柴油精馏过程是一个涉及高温(加热导热油的温度通常控制在250~300℃之间)高真空(操作绝压通常低于1000Pa)的单元操作,操作的关键之一就是高真空条件的维持;高真空操作的目的主要有两方面:a)生物柴油组分甲酯沸点高,高真空操作可降低甲酯沸点,从而降低加热介质导热油温度,减少能耗。生物柴油主要由碳16甲酯和碳18甲酯组成,因原料不一样,也会含有一定量的低碳甲酯(碳数小于16个)和高碳甲酯(碳数大于18个),操作绝压在1000Pa条件下,碳16甲酯、碳18甲酯的沸点仍处在较高的温度,约在170℃~200℃之间。b)生物柴油组分碳18甲酯中不饱和键含量较多(油酸甲酯、亚油酸甲酯和亚麻酸甲酯等),高真空可降低甲酯沸点,进而减少甲酯在高温汽化的过程不饱和键的分解。操作的另一关键是生物柴油加热汽化过程的停留时间控制,过长也会造成甲酯中不饱和键的分解,产品酸值升高,颜色加深,甲酯精馏得率下降。工业生物柴油精馏过程还需要考虑的一个问题就是热能回收。生物柴油的汽化热平均值约为65kcal/kg,比热约为0.5kcal/(kg.℃),这意味着1kg生物柴油液体产品从饱和温度冷到室温所释放的热量与1kg甲酯蒸汽冷凝释放的汽化潜热相当,因而热量回收应不仅仅考虑甲酯显热,同时也要考虑甲酯的潜热一起回收;本项目开发的一种基于多层蒸发的生物柴油连续精馏系统和工艺,该系统包括进料泵,进料泵连有产品-原料换热器,产品-原料换热器通过组合冷凝器连有多层蒸发器,多层蒸发器上方连有冷凝器,冷凝器连有产品中间罐,产品中间罐连有出料泵,多层蒸发器下方通过中间进料泵连有精馏塔,精馏塔上方通过组合冷凝器连有轻组分中间罐,轻组分中间罐经回流泵连有产品-原料换热器以及预热器,预热器连回精馏塔。
a)通过进料泵输送,粗生物柴油原料依次通过产品-原料换热器、组合冷凝器预热,进入多层蒸发器脱除低碳甲酯等轻组分,轻组分蒸汽通过与多层蒸发器顶部连接的冷凝器冷凝后,收集在轻组分中间罐,经出料泵输送作为生物柴油轻组分产品;
b)脱净低碳甲酯等轻组分后的粗生物柴油再经中间进料泵输送,进入精馏塔精制,进入精馏塔内的粗生物柴油由精馏塔底部多层蒸发加热托盘汽化,生物柴油蒸汽经与精馏塔顶部连接的组合冷凝器冷凝,收集在产品中间罐,经回流泵输送,部分经预热器加热回流至精馏塔内,部分经产品-原料换热器冷却后出料作为生物柴油产品,精馏塔底部出料为生物沥青。
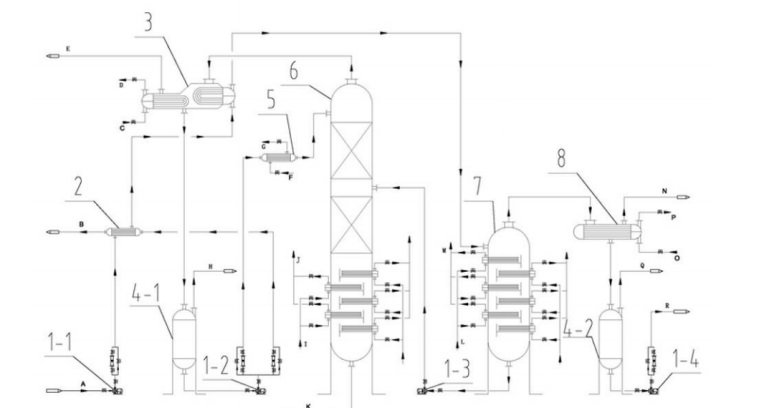
本项目结构示意图:(进料泵1-1、回流泵1-2、中间进料泵1-3、出料泵1-4、产品-原料换热器2、组合冷凝器3、轻组分中间罐4-1、产品中间罐4-2、预热器5、精馏塔6、多层蒸发器7、冷凝器8)
c)本项目技术的优点有:
1]、粗生物柴油经多层蒸发器脱净低碳甲酯等轻组分后,促使后续精馏塔体系维持较高的真空度,提高产能,降低能耗,提高产品的收率;
2]、在多层蒸发器和精馏塔内,均采用浅液层多层蒸发方式加热汽化,从而可降低加热托盘液层厚度,提高加热管表面真空度,降低加热介质温度,提高加热汽化量,通过加热托盘的层数可控制粗生物柴油加热汽化停留时间,最大程度上消除因停留时间过长造成的高温分解和聚合,提高生物柴油精馏得率,较釜式再沸器提高10%以上;3、通过组合冷凝器和产品-原料换热器,回收高温生物柴油产品的冷凝潜热和显热,极大的降低能耗,节能50%以上。
创新点四:采用多层蒸发技术脱除粗生物柴油的甲醇和微量水分,具有浅液层汽化、加热温度低、不返混和停留时间短的优点,达到了甲醇和水分脱尽、生物柴油不分解和产量大的目标;常规蒸发技术脱除甲醇和水分,时间长、能耗大,长时间加热导致生物柴油分解。生物柴油沸点高于350℃,从沸点上讲很容易脱除甲醇和水分;但是在不沸腾的条件下,甲醇和水分子从内部扩散到蒸发面需要很长时间。在传统的蒸发釜中需要数小时才能除尽甲醇和水分,生物柴油长时间受热导致部分分解;针对这个问题,开发了多层蒸发器,开发了一种种基于多层蒸发器的从生物柴油脱除甲醇的系统及工艺,系统包括多层蒸发器,多层蒸发器内设有6-12层加热盘,其中上层加热盘的液体溢出后能够流入至下一层加热盘内,加热盘内设有加热盘管及工艺液体温度计,多层蒸发器上设有对着上层加热盘的液体进口,输送泵通过原料控制阀和液体流量计与液体进口相连接,多层蒸发器的底部设有液体出口,多层蒸发器的顶部设有气体出口,气体出口连有冷凝器,加热盘管可供加热介质进出;本发明有益的效果是:利用每层独立控温的特点,原料从上而下一次性将甲醇脱尽,因此可以实现生物柴油脱除甲醇的连续操作工艺,达到原料加温时间短、操作简便易行的目的;在其内部设置了多层蒸发盘,每一层上有加热管,盘上液层高度100毫米(釜式蒸发器液层高2米),液体在盘上平推流流动,逐盘向下流动,流出最后一盘时甲醇和水已经除尽。多层蒸发器的优点是浅液层汽化,降低了汽化温度;液体不返混,停留时间均匀,效率高;设备内持液量小,停留时间短,液体从进到出15分钟即可完成任务;连续操作,产量高;采用多层蒸发技术使得粗生物柴油中的轻组分除尽,生物柴油不分解,且能耗有效降低。
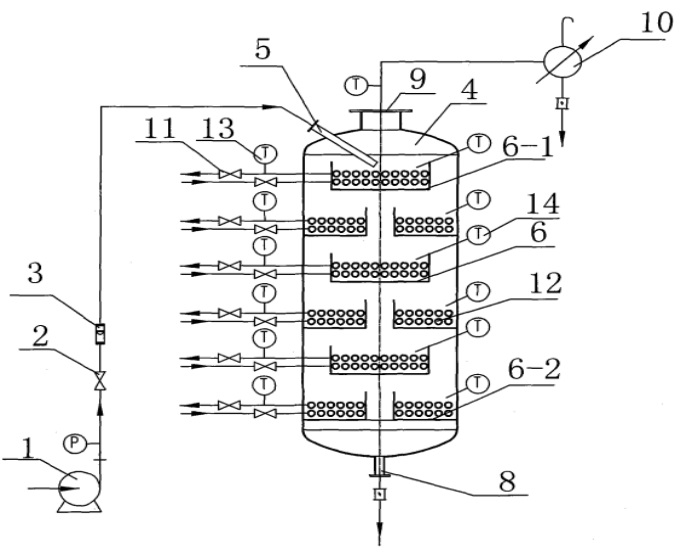
本项目结构示意图:(输送泵1,原料控制阀2,液体流量计3,多层蒸发器4,液体进口5,加热盘6,上层加热盘6-1,下层加热盘6-2,液体出口8,气体出口9,冷凝器10,导热油控制阀11,加热盘管12,导热油温度计13,工艺液体温度计14,水蒸气控制阀15,压力计16,疏水器17。)
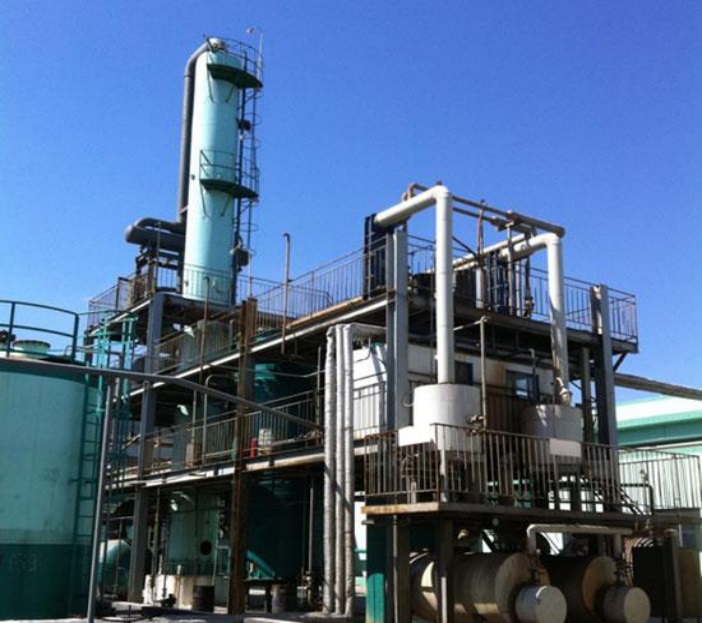
4、成套设备清单
设备名称 |
单位 |
单价 |
数量 |
用途说明 |
水油分相罐 |
只 |
5 |
2 |
粗甘油生产工业甘油 |
中和罐 |
只 |
8 |
1 |
甘油蒸馏系统 |
套 |
25 |
1 |
小 计 |
|
|
|
|
真空泵 |
台 |
5 |
2 |
粗甲酯脱杂 |
板式换热 |
台 |
3 |
3 |
精馏塔 |
套 |
30 |
1 |
屏蔽泵 |
台 |
8 |
6 |
小 计 |
|
|
|
|
原料暂存罐 |
只 |
5 |
2 |
流体循环酯化、酯交换 |
循环泵 |
台 |
2 |
6 |
中间体贮罐 |
只 |
2 |
5 |
小 计 |
|
|
|
|
耐腐蚀泵 |
台 |
3 |
4 |
辅助设备 |
齿轮泵 |
台 |
2 |
5 |
智能数显表 |
台 |
0.2 |
10 |
小 计 |
|
|
|
|
合 计 |
|
|
|
|
设备名称 |
单位 |
单价 |
数量 |
用途说明 |
沉降分离罐 |
只 |
5 |
4 |
粗甘油精制工业甘油 |
酸化罐 |
只 |
5 |
2 |
粗甘油暂存罐 |
只 |
2.5 |
2 |
闪蒸脱水罐 |
只 |
8 |
1 |
小 计 |
|
|
|
|
闪蒸罐 |
只 |
8 |
3 |
粗甲酯脱杂 |
小 计 |
|
|
|
|
酯化反应釜 |
只 |
8 |
2 |
流体循环酯化、酯交换 |
酯交换反应釜 |
只 |
10 |
2 |
小 计 |
|
|
|
|
合 计 |
|
|
|
|
|