
方形电池指以铝壳作外壳的电池,采用激光封口工艺,全密封铝壳技术已非常成熟,且对材料技术指标(如产气、膨胀)要求不高,是国内较早推广的一种动力电池形式。相对于其他两种锂电池形式(圆柱&软包),方形电池在市场使用中的优点突出,主要包括:①封装可靠性高;②系统集成效率高;③相对质量轻,能量密度较高;④结构简单,扩容方便,是单体大容量化的主要路径选择;⑤单体容量高,系统构造简单,便于电池管理。
1、 设备主要功能及描述 1.1 、铝壳(方形)锂电池装配设备:铝壳锂电池装配线用于动力电池中段装配,是动力电池生产过程的重要环节,对于电池的性能、精度都有举足轻重的影响,因此该装配线设备的自动化程度、操作的准确性等越来越受到市场的关注。本节将介绍一条非常成熟以及在市场上经得起考验并受到认可的电池装配线,该装配线设备有以下一些特点: ①兼容性强,可以根据客户的要求,从而兼容多种不同系列产品。 ②模块化设计,换型时间短、零件少、成本低。 ③装配精度高,视觉及机械双重定位方式,提高定位精度。 ④可根据客户不同工艺路线的电芯实现全自动装配线的非标定制。 ⑤工艺设备布局合理,节省空间,整线全自动化,人力成本很低。 ⑥高制造品质保证,全参数检测与监控。 ⑦电池安全性和一致性的制造保证。 本自动生产线用于实现方形铝壳锂离子动力电池卷绕后电芯的自动装配,生产线主要由以下几大部分组成:热压测试机、X射线机、配对机、超声波焊接机、转接片焊接机、合芯机、包膜/热熔/贴胶机、入壳预点焊机、激光顶盖焊接机、氦检机。实现电芯热压、X射线检测、极耳预焊配对、转接片极耳焊接、背面贴胶、盖板激光焊接、贴胶、折极耳合芯、包胶、包膜、入壳、顶盖封口焊接等功能,在整个过程中实现全自动化。整体布局合理,各设备结构紧凑,全程自动监控、智能化,各设备可实现追溯功能,连接MES系统,可实时上传数据到系统,设备运行稳定,关键部件均采用进口品牌或国际一线品牌,该装配线在其他客户工厂大批量投入生产,得到充分验证,各设备技术成熟。
1.2 、装配产线未来的发展趋势:铝壳(方形)电池生产线使用时间比较长,相应的技术已经非常成熟,现有的装配线设备也大同小异。未来的发展趋势,除了从材料方面继续改善,找到高性能的电芯材料外,对于电池装配生产线而言,高效率、低成本等依然是动力锂电池未来发展的方向,对现有市场发展概况总结后有以下几点值得关注: ①电池本体的性能方面,比如电池尺寸、能量密度、多极耳结构等。 ②装配生产效率,在保证设备成本改动不大的情况下,不断提升生产效率。 ③电池装配线的自动化程度不断提升,同时生产的良率更容易控制。合理控制每个工序的制作时间,从而有效缩短锂电池的生产时间,而且极大改善了工人的劳动强度大和生产成本高的问题。 ④兼容性更好,适合更大范围的产品。 ⑤模块化技术是提高效率的重要途径。
1.3 、铝壳(方形)锂电池生产装配线的设计:对于铝壳锂电池产线的设计,针对客户提出的要求会有不同的设计。根据在生产过程中遇到的问题及相应的实践,主要要从以下几个方面去考虑: ①产品的工艺:包括电池的大小、极耳的大小、焊接的厚度等。 ②厂房空间大小:合理安排生产线设备的具体位置,以及要优化的机构等,还要考虑人机工程,人工操作的方便性,以及后期维护的可操作性。 ③设备设计:结构越简单越好,这样操作更容易。 ④生产线中节拍的分配:重点考虑瓶颈工位的效率,如果效率达不到,考虑将单工位改动为双工位甚至多工位,同时高的安全性能和直通良率也是重点关注的点。 ⑤产品定位方式:对于客户不同的需求,采用不同的产品定位方式,比如侧边定位、以两边为基准定位、夹具定位等。 ⑥粉尘防止装置:圆柱电池装配线设备中基本都是每个需要除尘的设备中都有相应的除尘设施,比如集尘器、毛刷等。 ⑦设备中的物流设计:包括设备内部的输送、设备之间的输送等。 ⑧质量检测:整套装配线中会设计CCD检测、电芯测厚检测、绝缘检测、短路检测等。 ⑨生产线的外观的一致性,保持整套设备的美观。02 设备组成及关键结构
1.4、铝壳锂电池装配线设备整体布局如下: ①整线尺寸:长×宽×高=3700mm×7000mm×2400mm(高度不包括报警灯),操作面高度900mm,设备间距800~1000mm。 ②外观:受力底架采用方通焊接结构,上部密封框架采用铝合金型材结构,用有机玻璃进行密封,设备外罩整体用钣金包覆。 ③操作界面:每台设备均设有独立操作的触摸屏,所有设备的触摸屏全部采用嵌入式。 ④整线布局:铅壳电池装配线布局如图1所示。
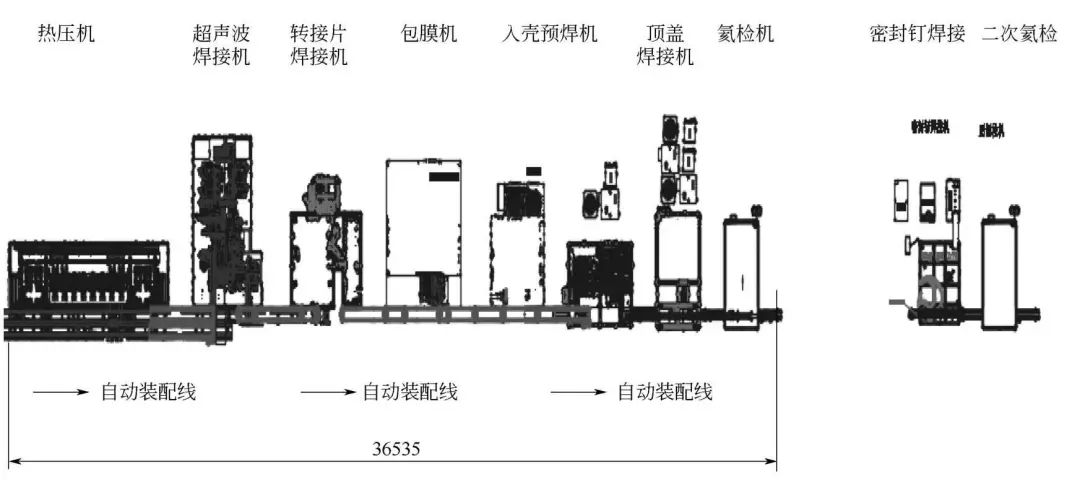
图1 铝壳电池装配线布局
2、本生产线是全自动生产线,包含了铝壳电池从热压机至氦检机的全部生产过程,如图2铝壳电池整体工艺所示,即:卷绕到热压输送线(包含卷绕机上取料机械手6套)→热压机→超声波焊接机→转接片激光焊接机→包麦拉机→入壳和预点焊接机→顶盖激光焊接机→气密性检测机。
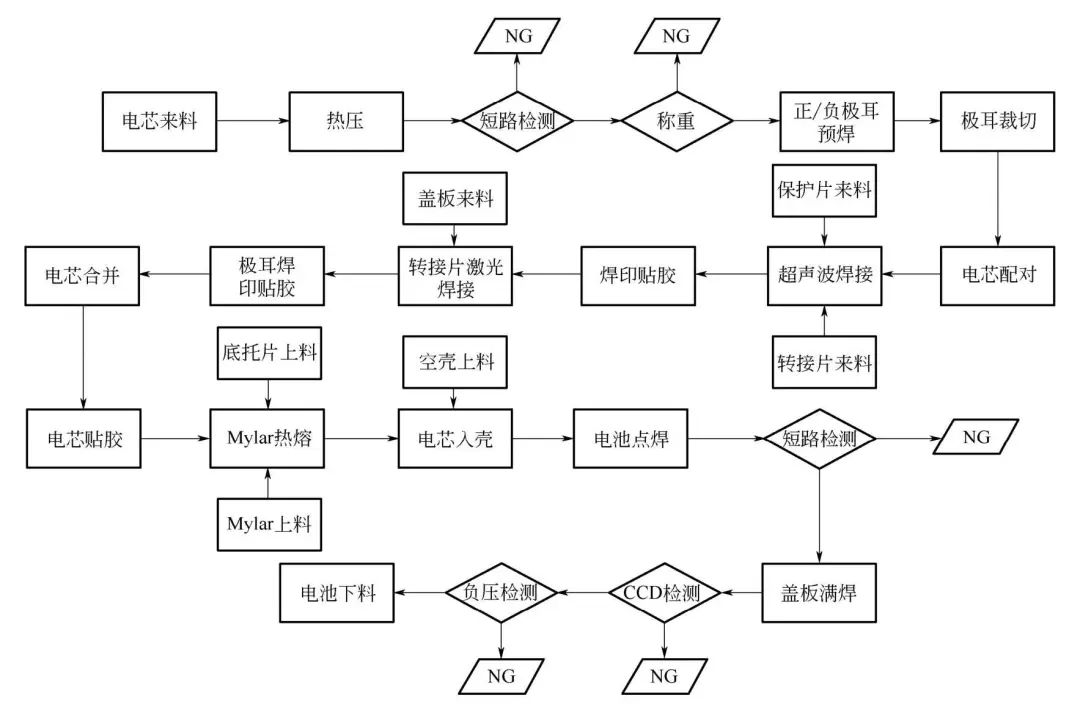
图2 铝壳电池整体工艺
2.1、热压机:热压机设备用于卷绕电芯的热压成型,主要功能包含:电芯来料扫码、A/B电芯分别自动上料、热压、Hi-pot测试、不良品剔除。热压温度、压力、时间及Hi-pot测试参数及结果与条码对应关联,并上传到MES系统中。该设备主要包含电芯上下料模块、检测模块、热压模块等。该设备是装配铝壳电芯的第一道工序,热压卷绕电芯成型的效果直接影响后续的加工成品质量,因此该装配设备的效率、工作精度、自动化程度都是需要重点考量的。其设备布局以及工艺流程如图3和图4所示。
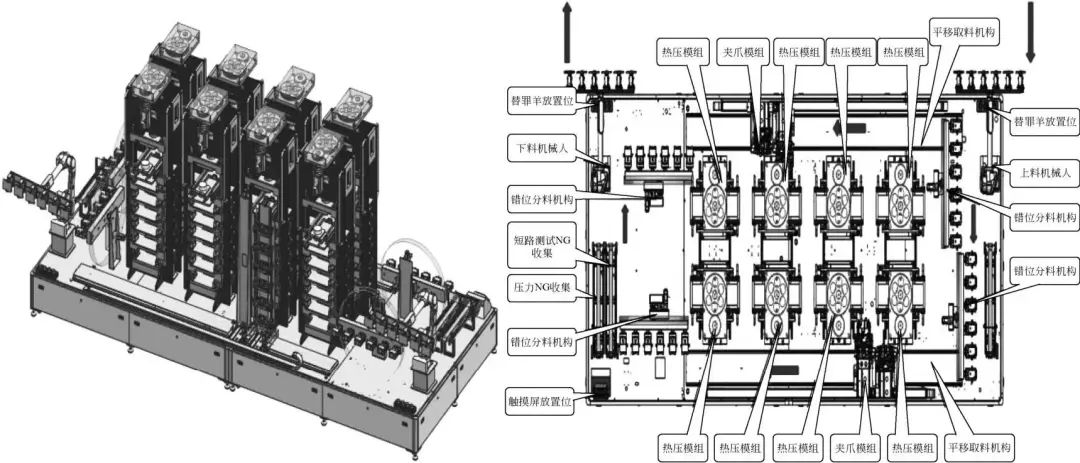
图3 热压机设备布局
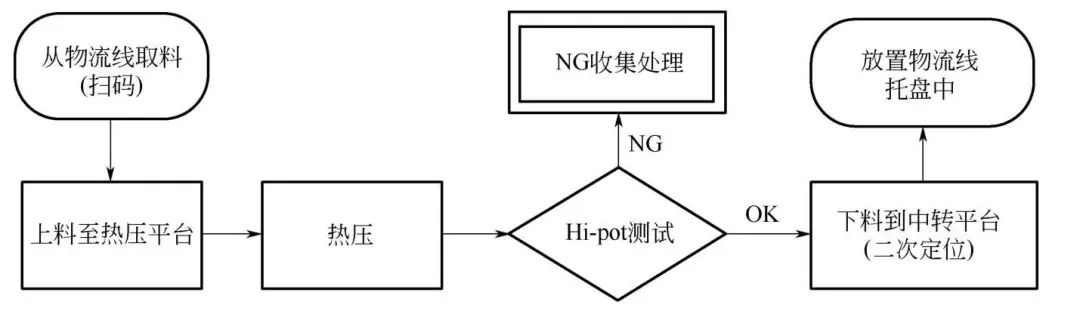
图4 热压机工艺流程
1)由图4可以清晰看出卷绕电芯在热压机上的操作过程,工作过程中设备对卷绕电芯热压后并进行检测,并将检测结果包括热压温度、压力、时间及Hi-pot等上传到MES系统中,进行实时跟进反馈,剔除不良品,保证加工质量。
2)从图3的设备布局图中可知,热压机设备中上下料机械手组件、进出转移拉线、转移机械手、错位分料机构、热压组件等比较关键,对整个装配出来的半成品有至关重要的作用,选取其中几个机构做详细的介绍说明。
①错位分料机构。如图5所示为错位分料机构,其中翻转定位模块的作用是:翻转机构使用皮带伺服驱动,实现夹具翻转和连接板同步翻转,夹具始终保持水平,翻转平稳可靠。定位夹具使用夹爪气缸、双联杆气缸夹紧和定位;与电芯接触面使用POM材料。
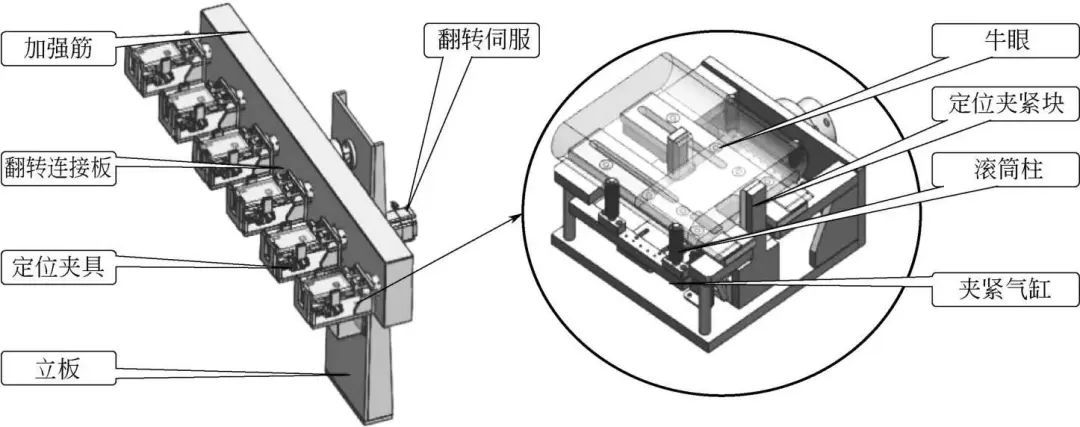
图5 错位分料机构
②上下移载模块。上下移载模块如图6所示,其主要完成的动作为:平移使用同步带伺服模组,双皮带驱动,增加上下料模组移动的平稳性能;上下料模组进出料使用皮带伺服,独立伺服控制;夹爪升降使用丝杆气缸升降;变距机构使用伺服驱动连杆机构,以中间连杆为定位基准,实现同步变距,伺服可控制夹爪等距尺寸,实现热压机在不同工作位置平移模组同步进出料。
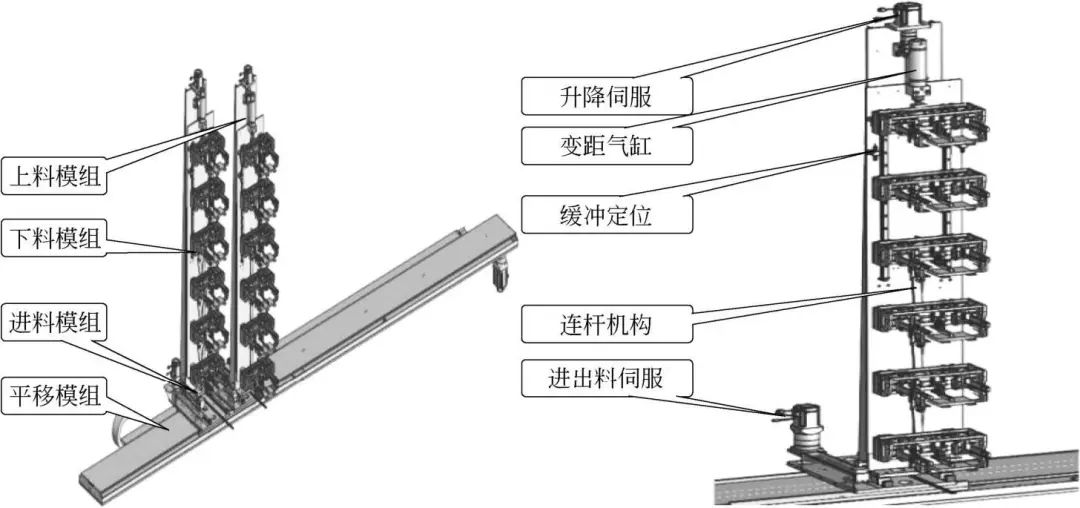
图6 上下移载模块
③热压组件。热压机设备的热压组件如图7所示,对其详细说明如下:
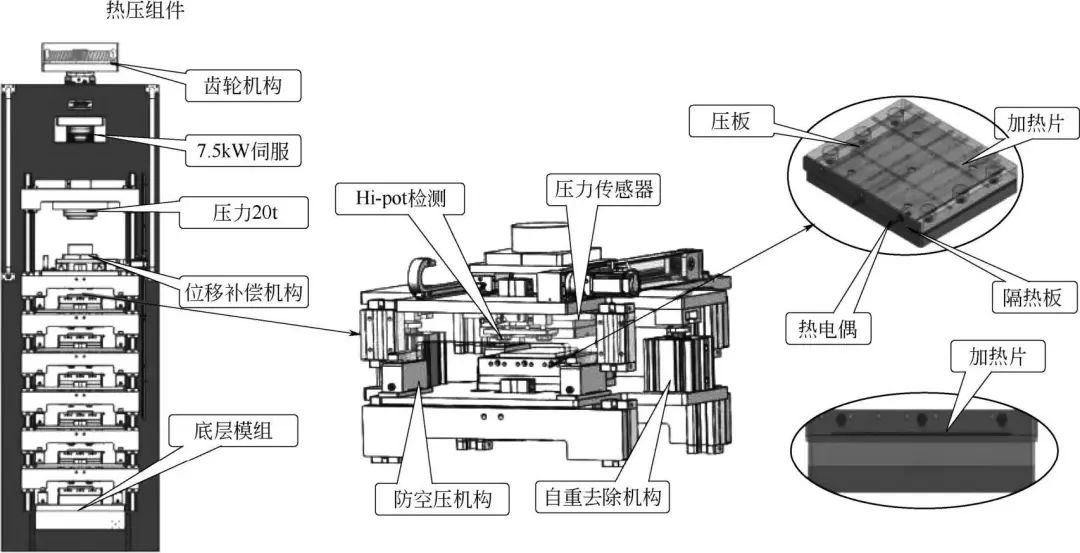
图7 热压组件
*主要部件:增压缸(压力20t、6层)、发热管、温控器、压力传感器等。
*动作流程:对电芯进行热压和Hi-pot测试。
2.2、 超声波焊接机:超声波焊接机主要通过电芯扫码、机械手自动取配对电芯、电芯校正与极性检测、转接片储片极性检测与校正、转接片上焊接治具、电芯上焊接治具、放保护盖板、超声波焊接与抽尘、焊印整形、贴胶与贴胶检测、自动下料等工序完成电芯超声波焊接。该设备实现电芯配对后至包膜前的电芯扫码、超声波焊接、贴胶及信息绑定;主要包括:电芯进站扫码、电芯校正上料、转接片校正上料、贴胶检查、信息绑定上传(MES系统)等功能。其设备布局图如图8所示。
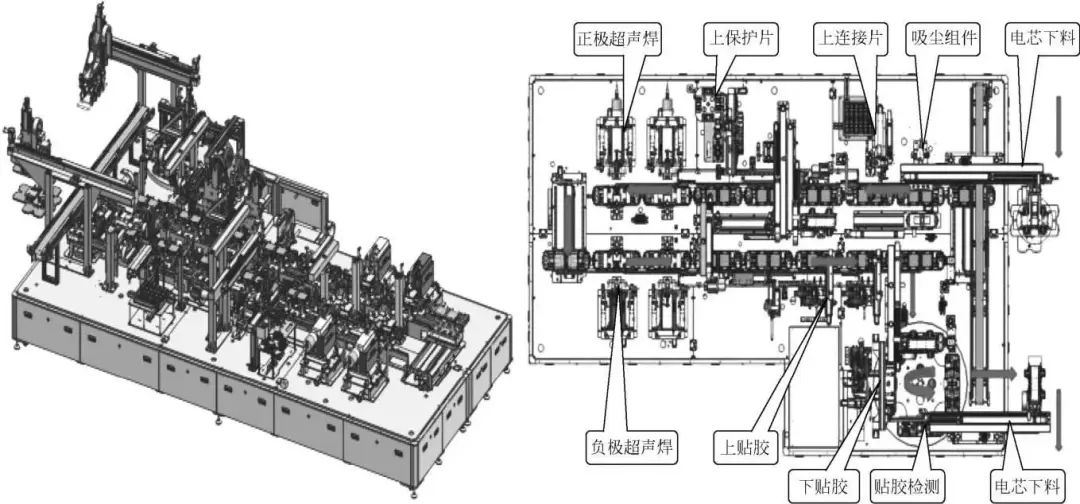
图8 超声波焊接机设备布局
*其中抓取机上装有颜色传感器来识别电芯的正负极耳,确保极耳不会配对出错。电芯从来料输送带上被机械手抓取,经过电芯二次定位后,再放入托盘中,保证A/B电芯极耳错位误差≤±0.2mm。电芯放置在托盘内采用居中对准,在放入电芯之前,托盘四周的弹性夹子会张开,然后机械手把电芯放入托盘中,夹子闭合,电芯被定位在托盘正中。本设备是自动生产线,详细工艺流程图如图9所示。
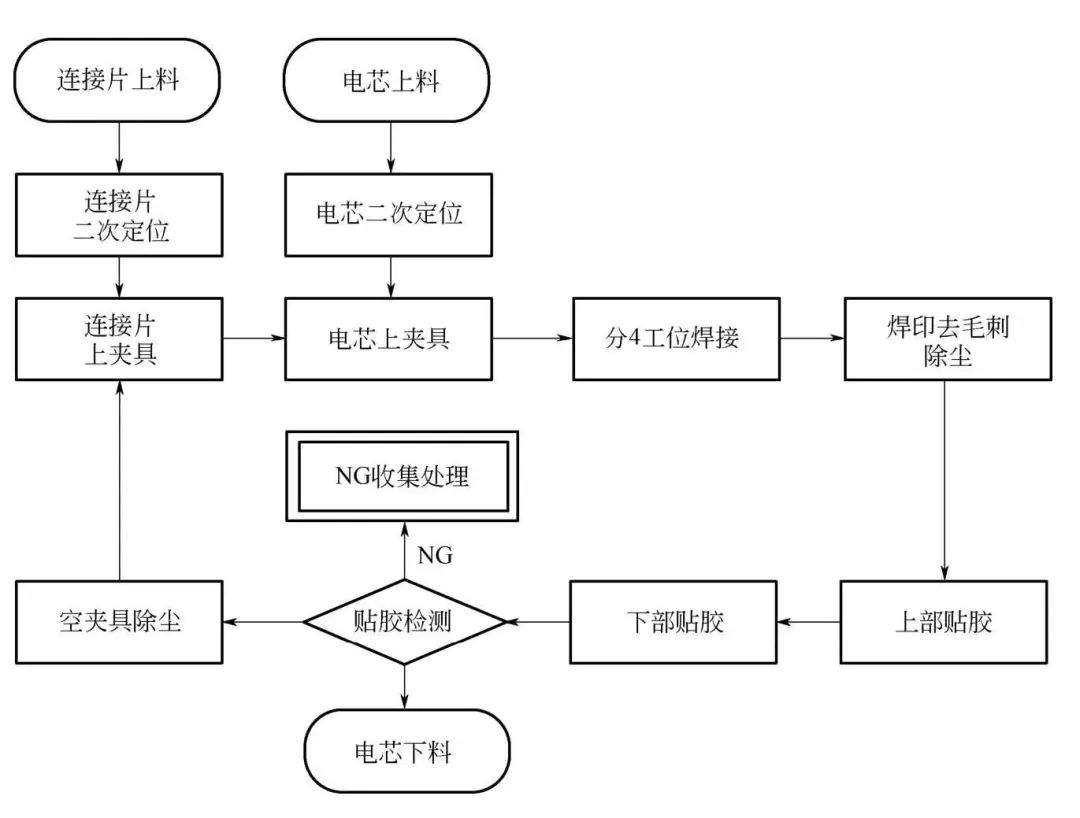
图9 超声波焊接机详细工艺流程图
1)设备组成及关键结构:从图8超声波焊接机设备布局图中可知,电芯上料模块、电芯超声波焊接循环线和夹具模块、转接片、保护片上料模块、保护片盖板上下料模块、超声波正负极焊接模块、焊印压平模块、电芯贴上保护胶模块、电芯贴下保护胶模块、电芯下料模块、贴胶检测等比较关键,对整个装配出来的半成品有至关重要的作用,选取其中几个机构做详细的介绍说明。
①电芯上料模块(图10)。具备电芯自动上料、来料除尘、来料防呆、来料缓存、缺料报警功能,同时具备电芯扫码绑定功能。
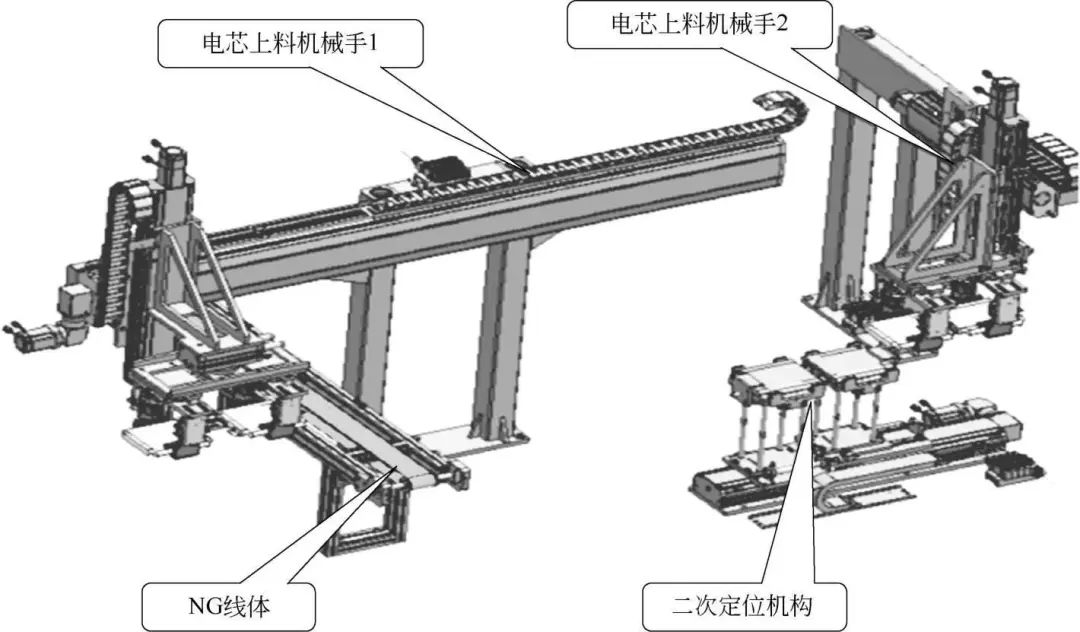
图10 电芯上料模块
a.主要零部件:平移机构+升降机构、电芯夹爪等。
b.动作流程:电芯上料搬运使用皮带模组,搬运机械手1从客户端物流线托盘中抓取一组电芯到二次定位机构;电芯二次定位后搬运机械手2将电芯抓取到循环线体。如果在上料过程中检测出两组电芯中有单组NG电芯,由搬运机械手1将NG电芯放回NG线体,再将OK单组电芯放入配对机构等待配对。
②电芯超声波焊接循环线和夹具模块。
a.主要零部件:循环线、模组、长短边定位块、气缸、导轨等。
b.动作流程(无动作流程写功能说明):电芯上料机械手2将电芯上料到循环线夹具,夹具夹紧电芯,平移机构带动夹具平移到下一个工位。
(末完、待续)
|