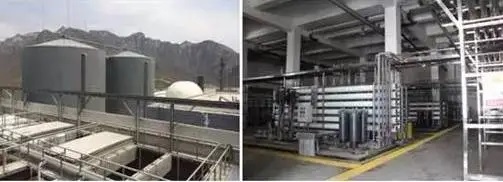
第四章 设计计算书
1、细格栅的设计说明、计算
1.1、细格栅设计说明:
1)按形状,格栅可分为平面格栅和曲面格栅两种;按栅条净间隙,可分为粗格栅(50~100mm)、中格栅(10~40mm)、细格栅(3~10mm)三种;按清
渣方式,可分为人工清除格栅和机械清除格栅两种。
2)当格栅设于污水处理系统之前时,采用机械清除栅渣,栅条间隙为16~25mm;采用人工清除栅渣,栅条间隙为25~40mm。
3)过栅流速一般采用0.6m/s~1.0m/s。
4)格栅前渠道内的水流速度一般采用0.4m/s~0.9m/s。
5)格栅倾角一般采用采用45°~75°。
6)通过格栅的水头损失一般采用0.08m~0.15m。
7)机械格栅不宜少于2台,如为1台时,应设人工清除格栅备用。
8)格栅间隙16mm~25mm,栅渣量0.10m3~0.05m3栅渣/103 m3污水,格栅间隙30mm~50mm,栅渣量0.03~0.10m3栅渣/103 m3污水。
9)在大型污水处理厂或泵站前的大型格栅(每日栅渣量大于0.2 m3),一般采用机械清渣。小型污水处理厂也可采用机械清渣。
10)本工程设一道细格栅,取栅条间隙为6mm,采用机械清渣方式。
1.2、细格栅设计计算:
1.2.1、设计流量:
1)平均日流量:Q=280t/d=280m3/d=3.241×10-3 m3/s
2)设计最大流量:取污水总变化系数Kz=1.5 Qmax= Q·Kz Qmax=3.241×10-3×1.5 m3/s=4.8615×10-3 m3/s
1.2.2、设计参数:
1)栅条间隙b=6mm;
2)栅前流速ν1=0.7m/s;
3)过栅流速v=0.8m/s;
4)栅条宽度s=0.01m;
5)格栅倾角 =60°;
6)栅前部分长度0.5m;
7)栅渣量W1=0.1 m3栅渣/103m3污水。
1.2.3、设计计算:
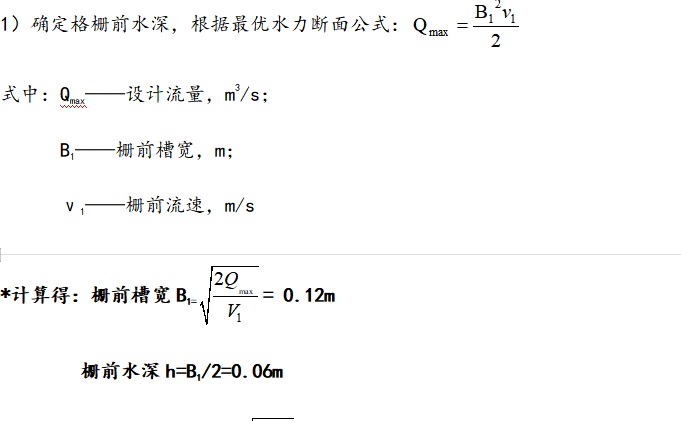
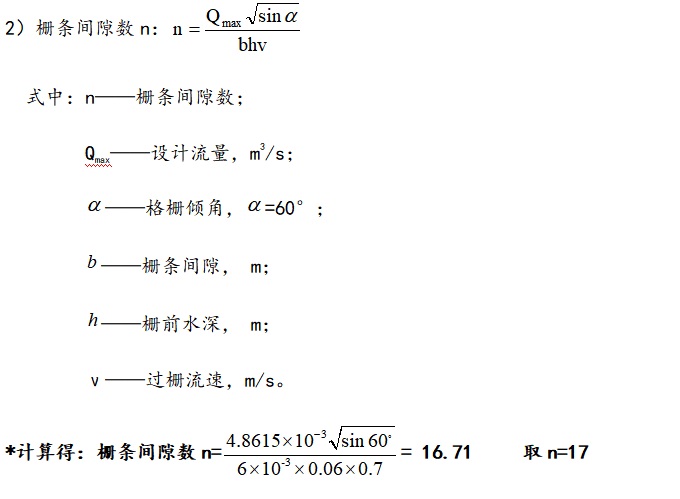
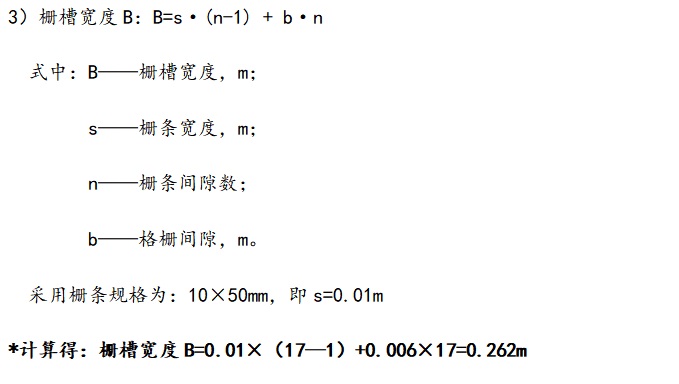
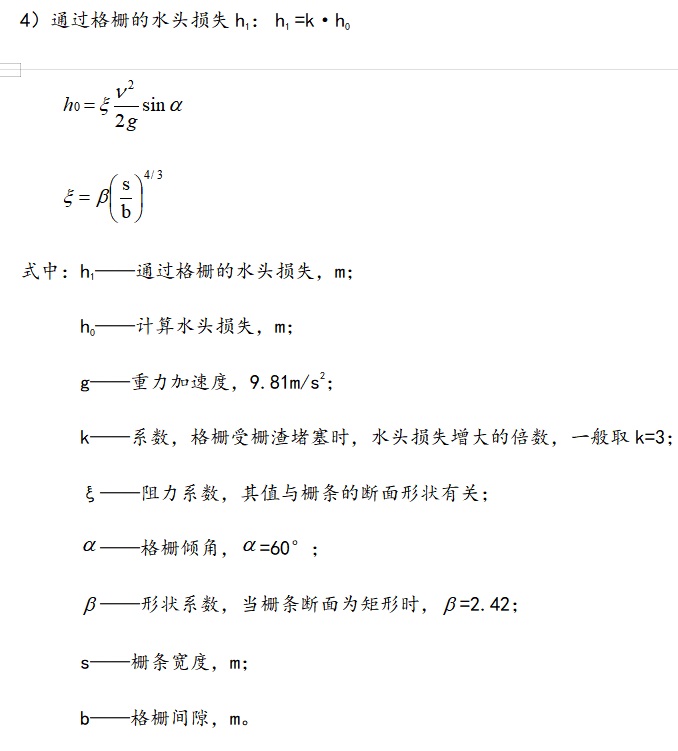
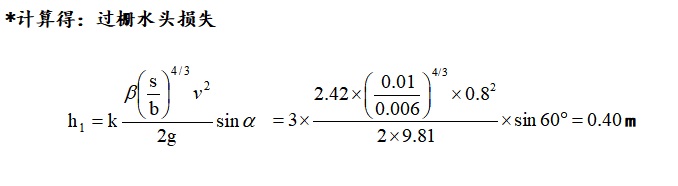
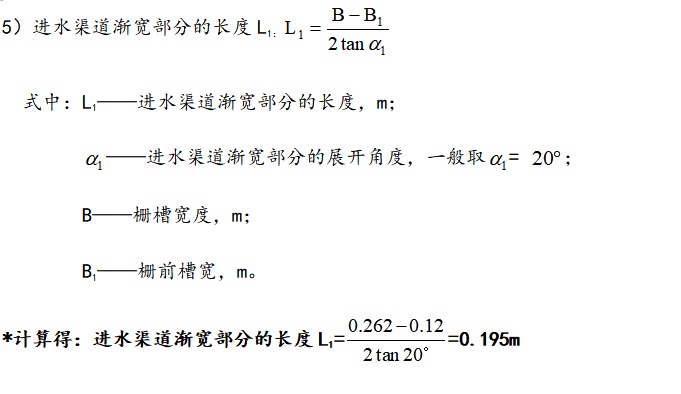
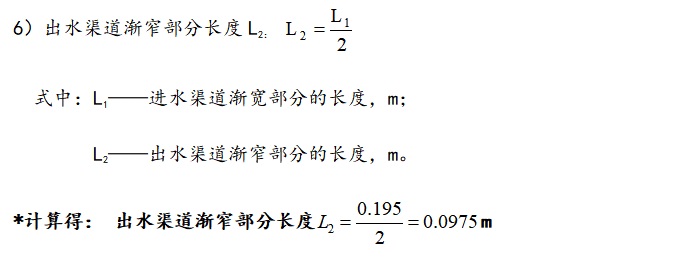
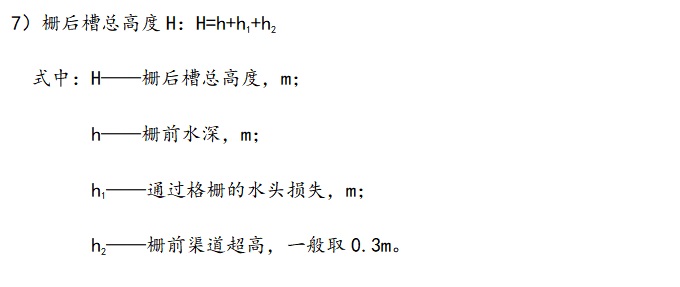
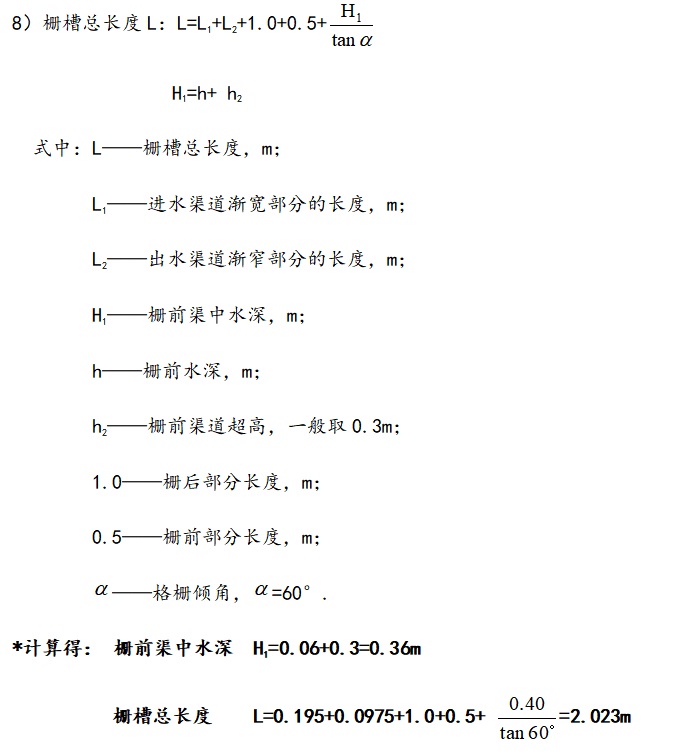
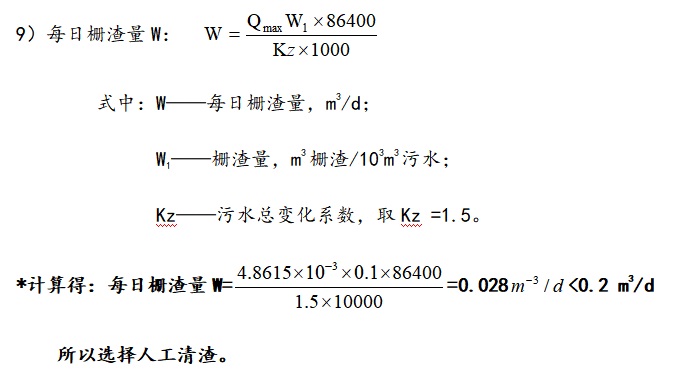
2、调节池设计说明及计算:
2.1、调节池设计说明:调节池可以调节水量和水质,调节水温及pH。本次调节池设计为钢筋混凝土结构,采用矩形池型。采用停留时间法进行设计计
算,本次设计采用停留时间t=6h.本次设计设置一个调节池,一个用于吹脱塔前,用石灰调节pH值至11,增加游离氨的量,使吹脱效果增加,去除更多的氨
氮。另一个用于吹脱塔后,用酸将pH值降低至8左右,达到后续生物处理所适宜的范围。调节池示意图如图2.2所示。
2.2、调节池设计计算:
2.2.1、调节池容积:
1)每日处理废水总量(即设计最大水量): Q0=280×1.5=420m3/d;
2)最大时平均流量:Qh=420/24=17.5 m3/h;
3)停留时间:t=6h;
4)调节池容积:V= Qh·t
式中:V——调节池容积,m3;
Qh——最大时平均流量,m3/h;
t——停留时间,h。
*计算得:调节池容积V=17.5×6=105m32.2.2、调节池尺寸:调节池的有效水深一般为1.5m~2.5m,设该调节池的有效水深为2.5m,调节池出水为水泵提升;采用矩形池,调节池表面积为:
式中:A——调节池表面积,m2;
V——调节池体积,m3;
H——调节池水深,m。
*计算得:调节池表面积A= m2;取池长L=6m,则池宽B=5m。
考虑调节池的超高为0.3m,则调节池的尺寸为:6m×5m×2.8m=84 m3,在池底设集水坑,水池底以i=0.01的坡度滑向集水。
3、初沉池:本设计采用竖流式初次沉淀池
3.1、设计参数
①池子直径(或正方形的一边)与有效水深之比不大于3.0,池子直径不宜大于8.0m,一般采用4.0~7.0m。
②中心管流速不大于30mm/s,本设计中取V0=28mm/s
③中心管下口设有喇叭口和反射板,反射板板底距泥面至少0.3m;喇叭口直径及高度为中心管直径的1.35倍;反射板的直径为喇叭口的1.3倍,反射板表面
积与水平面的倾角为17°。
④中心管下端至反射板表面之间的缝隙高在0.25~0.50m范围内,缝隙中污水流速在初沉池中不大于30mm/s,本设计中取v1=25mm/s。
⑤当池子直径小于7.0m时,处理出水沿周边流出,当直径D≥7.0时,应增设辐流式集水支渠。
⑥排泥管下端距池底不大于0.20m,管上端超出水面不小于0.40m。
⑦浮渣挡板距集水槽0.25~0.50m,高出水面0.10~0.15m,淹没深度0.30~0.40m。
3.2、设计有关公式
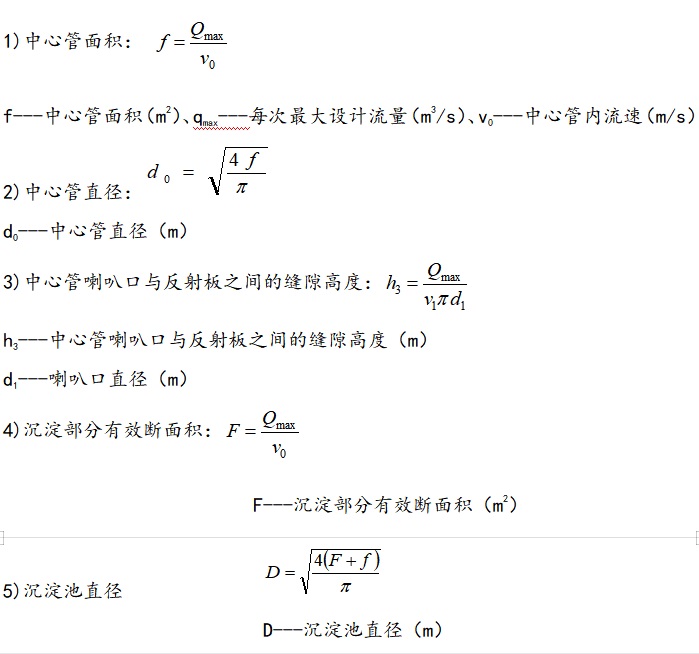
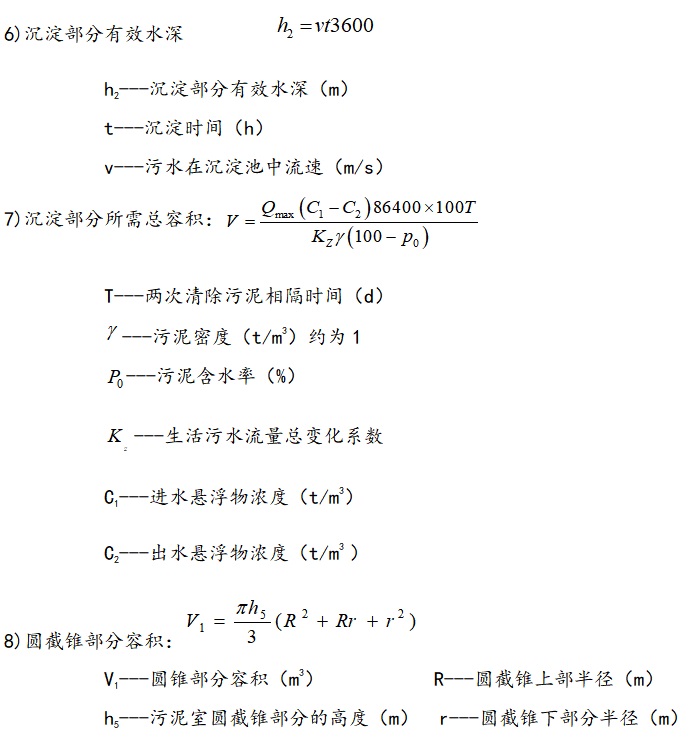
9)沉淀池总高度:H=h1+h2+h3+h4+h5
H---沉淀池总高度(m)
h4---缓冲层高度(m)
h1---超高(m)
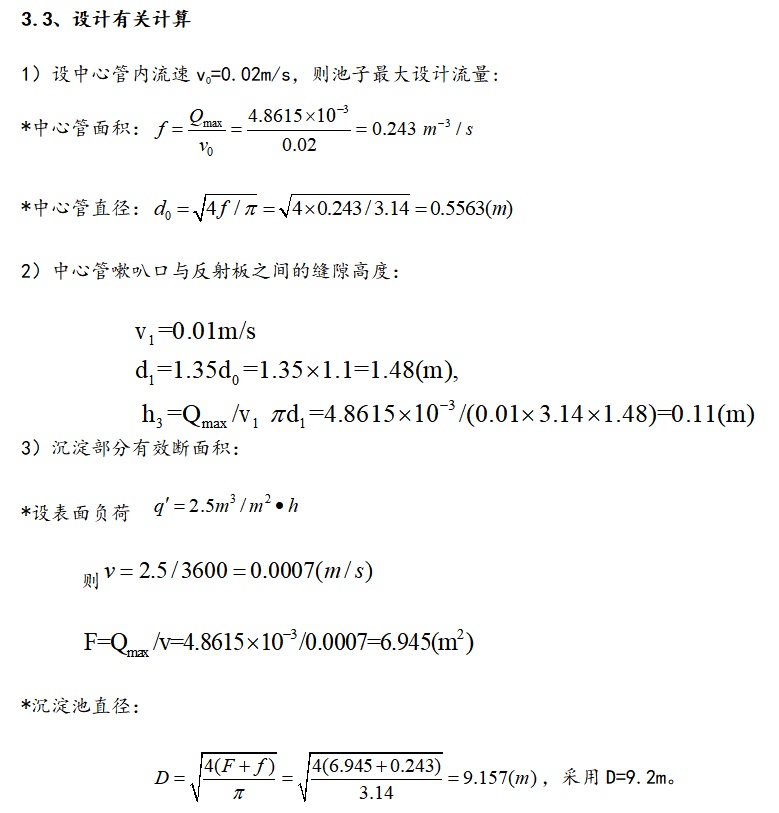
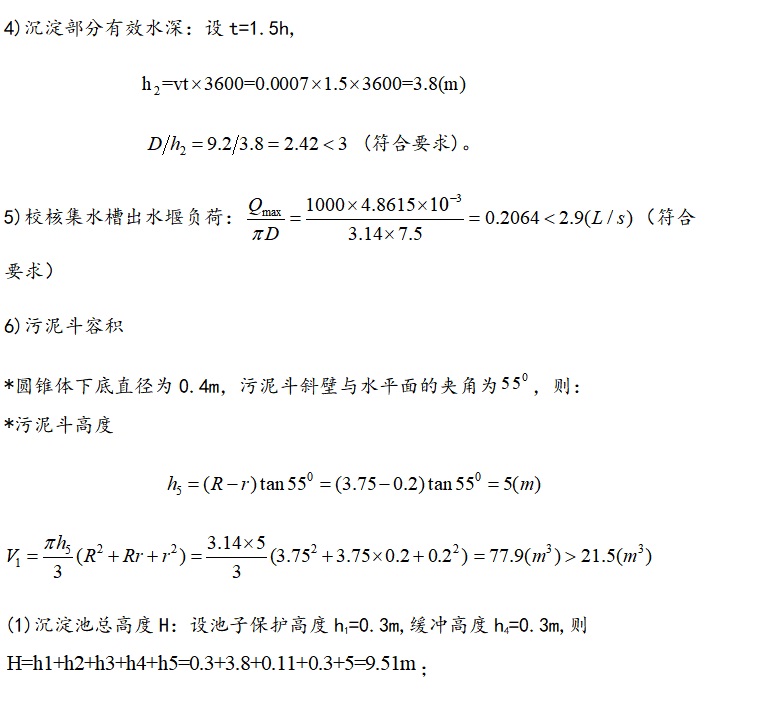
4、吹脱塔
4.1、设计说明:吹脱塔是利用吹脱去除水中的氨氮,在塔体中,使气液相互接触,使水中溶解的游离氨分子穿过气液界面,向气体转移,从而达到脱氮的
目的。
1)NH3溶解在水中的反应方程式为:NH3+H2O=NH4++OH-;从反应式中可以看出,要想使得更多的氨被吹脱出来,必须使游离氨的量增加,则必须将进
入吹脱塔的废水pH值调到碱性,使废水中OH-量增加,反应向左移动,废水中游离氨增多,使氨更容易被吹脱。所以在废水进入吹脱塔之前,用石灰将pH
值调至9,使废水中游离氨的量增加,通过向塔中吹入空气,使游离氨从废水中吹脱出来。
2)吹脱塔内装填料,水从塔顶送入,往下喷淋,空气由塔底送入,为了防止产生水垢,所以本次设计中采用逆流氨吹脱塔,采用规格为25×25×2.5mm的陶
瓷拉西环填料乱堆方式进行填充。吹脱塔示意图如图2.4.1所示。
4.2、设计参数:
1)设计流量Qmax=420 m3/d=17.2 m3/h=4.861×10-3 m3/s
2)设计淋水密度q=100 m3/(m2·d)
3)气液比为2500m3/m3废水
4.3、设计计算:
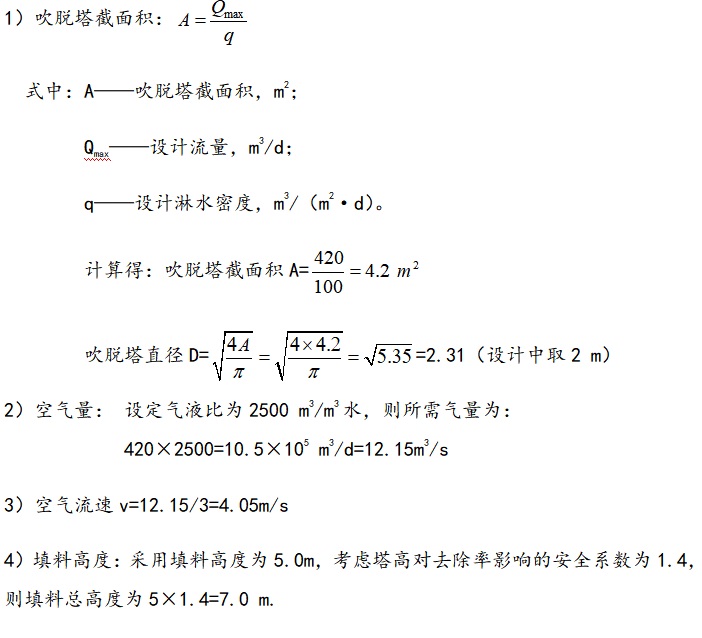
5、UASB反应器
5.1、设计说明:UASB,即上流式厌氧污泥床,集生物反应与沉淀于一体,是一种结构紧凑,效率高的厌氧反应器;它的污泥床内生物量多,容积负荷率
高,废水在反应器内的水力停留时间较短,因此所需池容大大缩小;设备简单,运行方便,勿需设沉淀池和污泥回流装置,不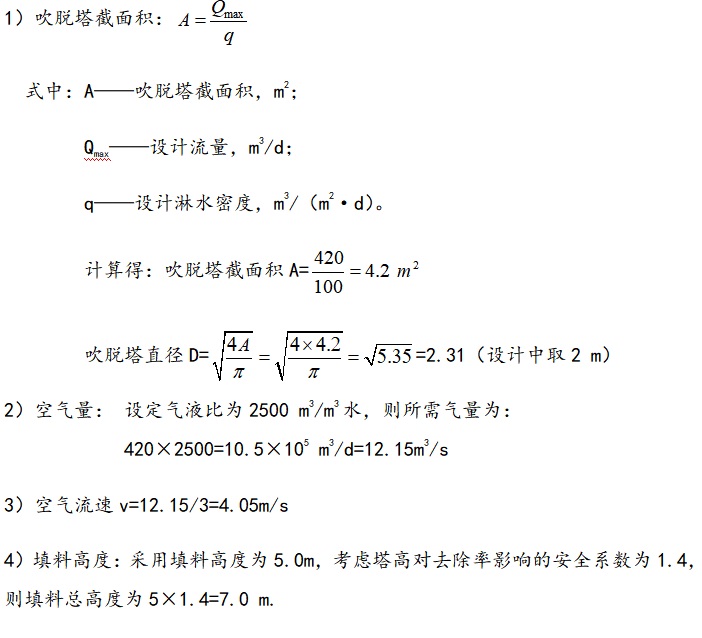
5)需充填填料,也不需在反应区内设机械搅拌装置,造价相对较低,便于管理,且不存在堵塞问题。
5.2、设计参数
1)设计参数选取如下:容积负荷(Nv)6.0kgCOD/(m3·d);污泥产率0.1kgMLSS/kgCOD;产气率0.5m3/kgCOD
2)设计水质: 表2.2 UASB反应器进出水水质指标
水质指标 |
COD |
BOD |
SS |
进水水质(mg/l) |
23000 |
11000 |
2200 |
去除率(%) |
75 |
90 |
87 |
出水水质(mg/l) |
5750 |
1100 |
286 |
3)设计水量:Q=280m3/d=11.67m3/h=3.241×10-3m3/s
5.3、设计计算
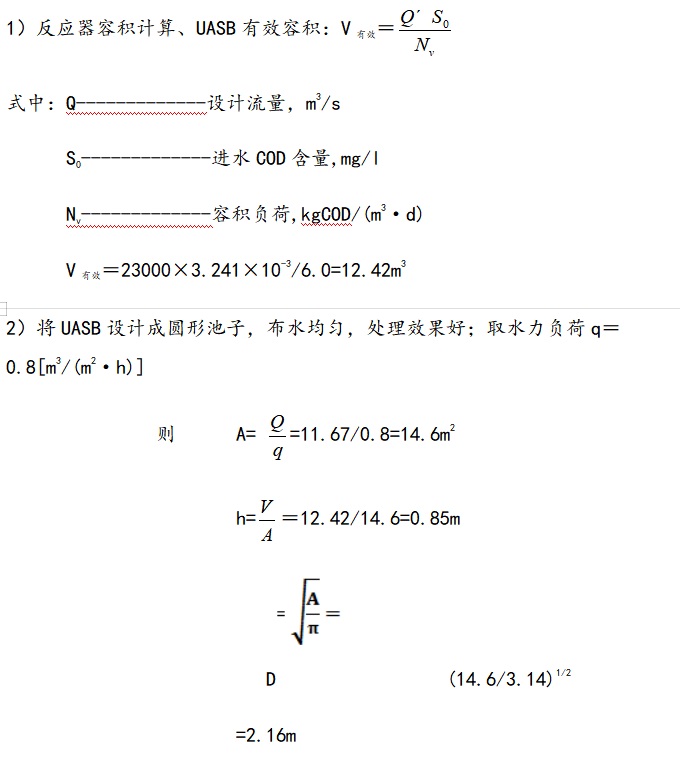
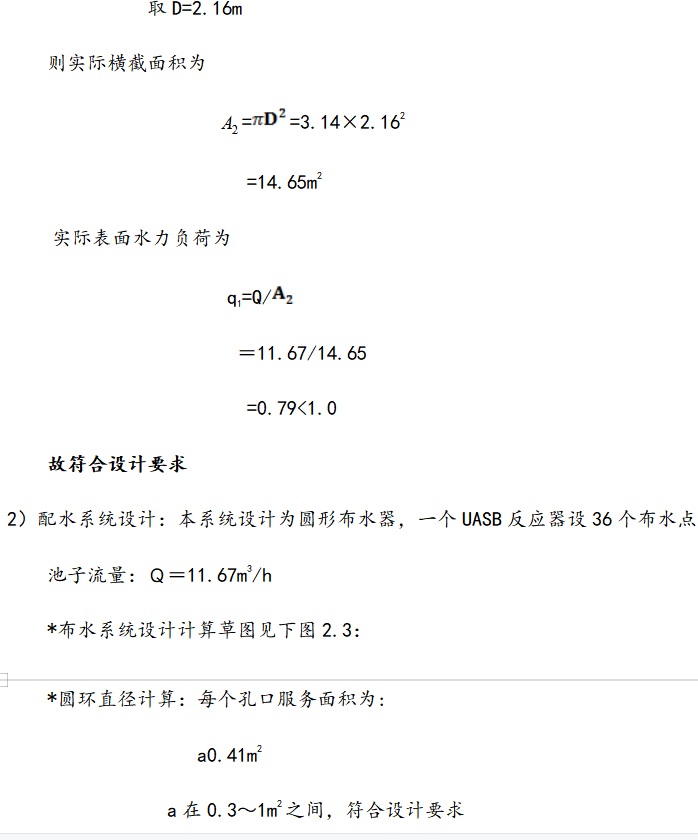
3)三相分离器设计
①设计说明:三相分离器要具有气、液、固三相分离的功能;三相分离器的设计主要包括沉淀区、回流缝、气液分离器的设计。
②沉淀区的设计:三相分离器的沉淀区的设计同二次沉淀池的设计相同,主要是考虑沉淀区的面积和水深,面积根据废水量和表面负荷率决定;由于沉淀
区的厌氧污泥及有机物还可以发生一定的生化反应产生少量气体,这对固液分离不利,故设计时应满足以下要求:a.沉淀区水力表面负荷<1.0m/h;b.沉淀器
斜壁角度设为50°,使污泥不致积聚,尽快落入反应区内;c.进入沉淀区前,沉淀槽底逢隙的流速≦2m/h;d.总沉淀水深应大于1.5m;e.水力停留时间介于1.5~2h;f.
如果以上条件均能满足,则可达到良好的分离效果
*沉淀器(集气罩)斜壁倾角θ=50°
*沉淀区面积为:A=πD2=3.14×2.162=14.65m2
*表面水力负荷为:q=Q/A=11.67/14.65=0.79<1.0
*符合设计要求。
③回流缝设计:取h1=0.3m,h2=0.5m,h3=1.5m,如图2.4所示:b1=h3/tgθ;
式中:b1----------下三角集气罩底水平宽度,m;
θ----------下三角集气罩斜面的水平夹角;
h3----------下三角集气罩的垂直高度,m;
b1= =1.26m
b2=9.5-2×1.26=6.98m
*下三角集气罩之间的污泥回流逢中混合液的上升流速V1可用下式计算:
V1=Q1/S1;式中:Q1----------反应器中废水流量,m3/h;
S1----------下三角形集气罩回流逢面积,m2;
V1=(208/4)/(3.14×6.982/4)=1.36m/h
V1<2m/h,符合设计要求
*上下三角形集气罩之间回流逢中流速(V2)可用下式计算:V2=Q1/S2,
式中:Q1----------反应器中废水流量,m3/h;
S2 ----------上三角形集气罩回流逢之间面积,m2;
*取回流逢宽CD=1.4m,上集气罩下底宽CF=7.8m;DH=CD×sin50°=1.07 m
DE=2DH+CF=2×1.07 +7.8 =9.94m
S 2=π(CF+DE)CD/2=39.0m2
则V2= Q1/S2=208/(4×39.0)=1.33m/h1<2m/h
故符合设计要求
确定上下三角形集气罩相对位置及尺寸
CH=CDsin40°=1.4×sin40=0.9m
AI=DItg50°=1/2(DE-b2)×tg50° = 1/2(9.94-6.98)×tg50° =1.76m
故 h4=CH+AI=0.9 +1.76=2.66 m
h5=1.0m
由上述尺寸可计算出上集气罩上底直径为:
CF-2h5tg40°=7.8-2×1.0×tg40°=6.12m
BC=CD/sin40°=1.4/sin40°=2.18m
DI=1/2(DE-b2)=1/2(9.94-6.98)=1.48m
AD=DI/cos50°=1.48/cos50°=2.30m
BD=DH/cos50°=1.07/cos50°=1.66m
AB=AD-BD=2.30-1.66= 0.64m
④气液分离设计:
d=0.01cm(气泡),T=20°С
ρ1=1.03g/cm3, ρg=1.2×10-3g/cm3
V=0.0101cm2/s, ρ=0.95
μ= Vρ1=0.0101×1.03=0.0104g/cm·s
一般废水的μ>净水的μ,故取μ=0.02g/cm·s; 由斯托克斯工式可得气体上升速度为:
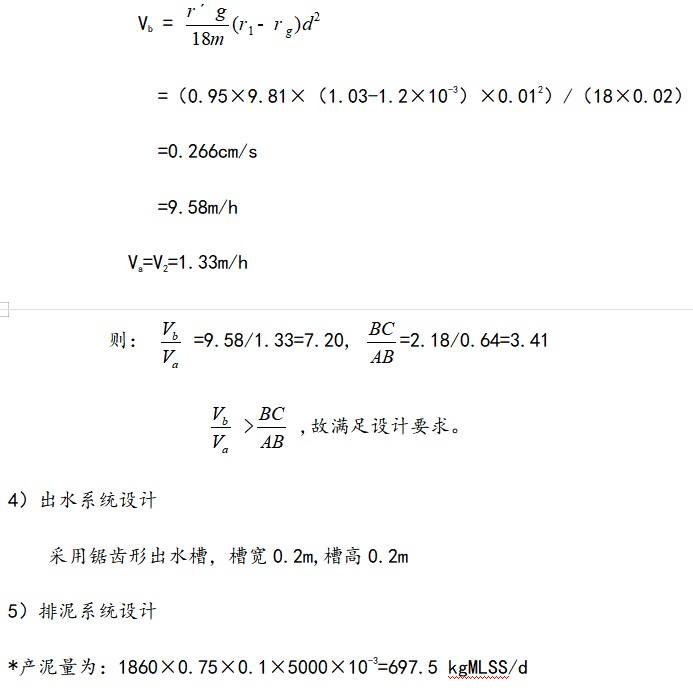
*每日产泥量697.5kgMLSS/d,则每个USAB日产泥量174.38kgMLSS/d,可用150mm排泥管,每天排泥一次。
6)理论上每日的污泥量:W=Q*(C0-C1)/1000(1-0.97)
式中:Q ------------ 设计流量,m3/d
C0 ------------ 进水悬浮物浓度,mg/L
C1 ------------ 出水悬浮物浓度,mg/L
P0 ------------ 污泥含水率,%
W=280*(175-22.75)/(1000*1000(1-0.98))=2.31m3/d
7)产气量计算:每日产气量:1860×0.75×0.5×280×10-3=195.3m3/d
6、MBR膜生物反应器
6.1、设计说明:MBR工艺的设计应主要包括生物反应器设计参数选取、泵系统选择、膜组件选择等几个方面;MBR工艺的设计应主要包括生物反应器设计
参数选取、泵系统选择、膜组件选择等几个方面。
1)生物反应器参数的选取。采用MBR工艺处理城市污水,污泥负荷、体积负荷已不再是制约处理效果的重要指标;根据中试运行的经验,可将水力停留时间
HRT、污泥停留时间SRT作为MBR工艺生物反应器单元的设计依据,因为这样不仅能确保工艺操作的长期稳定性,而且能简化设计过程。
2)泵系统选择。MBR工艺中加压泵的特点是扬程高、流量小;而循环泵则要求扬程低、流量大。考虑到加压泵和循环泵并联工作的需要,两种泵的扬程必
须相等,即H2=H3。泵流量的选择,则只需达到膜组件对设计膜面流速的要求即可。在此前提下,为节能起见,循环泵的流量宜大一些,而加压泵的流量宜
小一些(至少应满足Q2>Q)。
3)膜组件选取。膜组件是MBR工艺的关键组成单元,它的选择对MBR工艺的运行具有决定性的作用。研究表明:以回用为目的的城市污水生物处理应优先
选用超滤膜组件。膜通量是膜组件设计中最重要的技术参数之一。当处理能力一定时,设计选择的膜通量越高,所需的膜面积就越小,膜组件部分的固定投
资就越少;但另一方面,MBR工艺的运行周期也就会越短,从而增加膜组件清洗的次数和费用。设计运行周期一般不小于3周。
6.2、设计参数、生物反应器中微生物浓度X(即污泥浓度)理论计算公式如下:
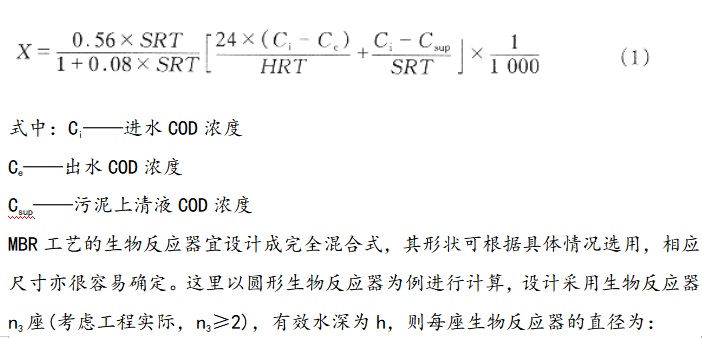
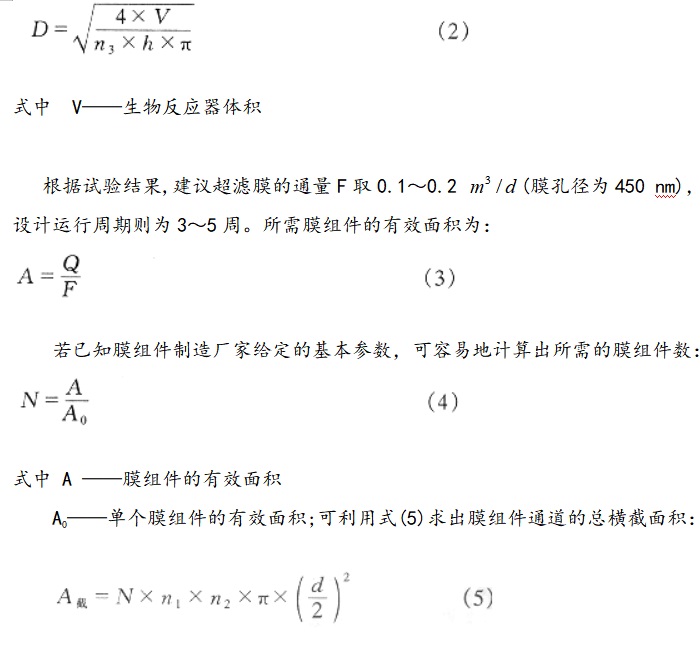
6.3、设计计算MBR工艺的污泥负荷比普通活性污泥法略低,而体积负荷则是普通活性污泥法的数倍。换句话说,与普通活性污泥法相比,这种工艺不仅对污
染物去除效率高,而且占地面积可以很小。
1) 设计流量:最大流量Qmax=420m3/d。拟采用MBR工艺进行处理并回用,故障检修时则将全部或部分污水排入城市污水收集系统。
2)进、出水设计水质: 设计水质选取中等强度的城市污水,参考中试的近三年运行结果,确定进、出水设计水质如表1。
表1 MBR工艺设计的基本参数
Q(m3/h) |
17.5 |
进水水质 |
CODi |
(mg/L) |
23000 |
SSi |
(mg/L) |
2200 |
出水水质 |
CODe |
(mg/L) |
20 |
SSe |
(mg/L) |
0 |
生物反应器设 计参数 |
CODsup |
(mg/L) |
165.5 |
X |
(g/L) |
11.1 |
V |
(m3) |
833 |
D |
(m) |
13.3 |
膜组件设计参数 |
A |
(m2) |
1 389 |
A截 |
(m2) |
1.02 |
A占 |
(m2) |
8.08 |
N |
(个) |
808 |
3)膜组件计算
① 膜组件数:设计采用超滤膜组件,膜通量F取0.15 m3/(m2*h)(膜孔径为450 nm),运行周期3~5周;以Modules KERASEPTM系列产品K07BC1XX为例,每
根膜长1 200 mm,直径25 mm,内有19个通道,通道内径约3.5 mm,7根膜装配成一个膜组件,膜组件直径约为100 mm,每膜组件的有效表面积为1.72 m2。
② 膜组件的通道总横截面积及安装占地面积已知膜组件有关尺寸,可由式(5)得到膜组件通道总横截面积A截及占地面积A占。
4)生物反应器计算
① 生物反应器中的污泥浓度: 根据2.1的分析,取SRT=15 d、HRT=4 h,可得生物反应器中的污泥浓度X。
② 生物反应器的直径:设生物反应器为圆形完全混合式,有效水深h=3.0 m,可由式(2)得到D;上述各参数见表1。
5)曝气部分计算:根据2.3的分析,采用射流曝气,查《给水排水设计手册》第5册选用射流流量Qr≥2Q,此处即416.6 m3/h;工作压力Hr要求98~147 MPa。
6)选泵计算
① 提升泵:由2.4的分析知,污水提升泵的选择较为简单,只需满足设计流量Q、提升高度H1即可。其基本参数见表2。
② 加压泵:为节能需要,设计采用射流曝气。根据式(6)和2.4节的分析,确定加压泵的设计流量应为:Q2≥624.9 m3/h;此处取加压泵的流量Q2=800
m3/h,扬程H2=161.8 kPa,已能满足超滤操作的需要。其基本参数见表2。
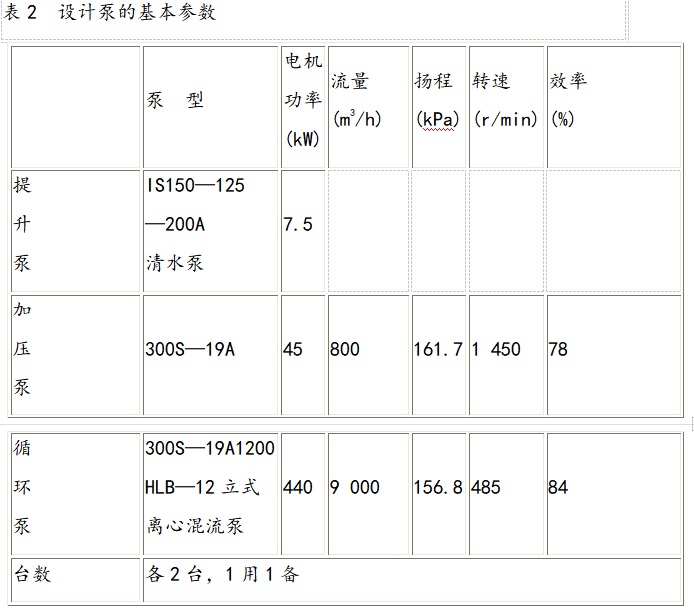
③ 循环泵:循环泵的设计流量Q3功能为膜组件提供适宜的膜面流速,以减缓膜堵塞的发生;扬程H3还满足与加压泵并联工作的需要。选泵结果见表2。
7)曝气装置设计:为有效利用高速循环的污泥混合液的能量,建议采用射流曝气装置进行曝气,可参阅《给水排水设计手册》第5册。一般,射流曝气
器的工作压力在98~196 kPa,建议回流流量Qr取2Q。
8)选泵计算: 提升泵的选择较为简单只需满足设计流量Q、提升高度H1即可,可直接查《给水排水设计手册》第11册进行选泵。流经膜面的总流量Qt则可
由最小膜面流速与膜组件横截面积的乘积来计算,而最小膜面流速和生物反应器中的污泥浓度线性相关;从图1中的流量平衡关系可知,流经膜面的总流量Qt
等于加压泵与循环泵的流量之和。加压泵扬程H2的选择非常重要,必须能够满足膜组件过滤操作对压力的需要以及整个系统管路的沿程、局部水头损失。根
据中试经验,加压泵的扬程H2≥147.1 kPa即可。为达到经济的目的,加压泵流量的选择应尽量小并使运行工况尽可能在最佳状态。如果考虑到射流曝气的需
要,加压泵的流量须满足:Q2≥Qr+Q (6);若不考虑射流曝气的需要,在实际MBR工艺的运行中则只须:Q2≥Q(7);选泵时可参考泵生产厂家给定的技术参数,
使Q2大于Q有一个余量,确保工艺长期稳定的运行; 循环泵流量Q3等于流经膜面的总流量和加压泵流量Q2之差(由于循环泵、加压泵并联工作)。
(9)污泥负荷、体积负荷校核:MBR工艺的污泥负荷比普通活性污泥法略低,而体积负荷则是普通活性污泥法的数倍。换句话说,与普通活性污泥法相
比,这种工艺不仅对污染物去除效率高,而且占地面积可以很小。
(10)污泥负荷、体积负荷校核: 经校核污泥负荷FW、体积负荷FV分别为0.14 kgCOD去除/(kgVSS.d)、2.88 kgCOD去除/(m3.d)。普通活性污泥法中FW=0.1
~0.4 kgCOD/(kgVSS.d),FV=0.4~0.8 kgCOD/(m3.d)。
6、超滤设备
6.1、设计说明:建议每30min进行一次物理清洗,清洗过程为(顺冲-反冲1-反冲2-顺冲),每次步骤全过程需用时约2min,其中顺冲各30s,反冲各30s;每天的
物理清洗次数=24hr/day×60min/hr÷(30min+2min)=45次/天,每天有效产水(用于后续工艺)时间= 24hr ×60min/hr -45次/天×2min=22.5hr;需求超滤系统产
水量为135m3/hr,采用错流过滤模式,按回收率为90%计算,考虑到超滤系统运行当中反冲消耗的产品水=135m3/hr×2×1min×45/60/24=8.5 m3/hr;*超滤设
计进水量为(135+8.5)÷90%=160 m3/hr。
6.2、设计参数:选用LH3-1060-V型超滤膜组件,按每支 3 m3/hr 水通量计算,故总超滤膜组件用量= 160m3/hr÷3 m3/hr*支=54支;模块数量:此方案采用2
个模块;
1)原水泵选择: 原水泵流量= 160m3/hr; 原水泵扬程:20米(0.20MPa)考虑到压力的管道损失,此泵扬程可选高以满足最大透膜压差。
2)反洗系统设计:建议每30min进行一次物理清洗,反洗用水为超滤自产水,可从超滤产水储存箱中引取。反洗流量按2倍的设计产水量,反洗可以两个模
块交替进行,故反洗水泵扬程:20 米(0.20MPa);当进水中含有一定量有机物和微生物的情况下,建议在反洗水中添加1-2ppm含量的游离氯,能有效控
制有机物和微生物引起的污染。
3)化学清洗系统设计:化学清洗液流量选择 1-2 倍的产水流量,这里建议选择1.5倍化学清洗循环泵流量= 135×1.5=202.5m3/h 化学清洗循环泵扬程:15 米
(0.15MPa)化学清洗箱建议容积:每支膜壳体积Φ277×1600=100L;3m3。
7、污泥浓缩池
7.1、设计说明:污泥浓缩的主要目的是减少污泥体积,以便后续的单元操作。污泥浓缩的操作方法有间歇式和连续式两种。通常间歇式主要用于污泥量较
小的场合,而连续式则用于污泥较大的场合。污泥浓缩的方法有重力浓缩、气浮浓缩、和离心浓缩,其中重力浓缩应用最广。根据本次设计知整个工艺流
程产泥量较小,因此选择一个不带中心管的间歇式重力浓缩池,其结构如图2-7-1所示。其浓缩原理是污泥在重力浓缩池中,污泥依次通过自由沉降、絮凝沉
降、区域沉降、压缩沉降的过程来脱去部分水分。即是通过自身重力来压密的过程。污泥浓缩池采用钢混结构;本次设计的污泥来源:(1)MBR工艺产生
的剩余污泥;(2)竖流式混凝沉淀池产生的污泥;由于MBR池将产生的污泥送入污泥浓缩池的同时,污泥浓缩池中的污泥又有部分回流至MBR池中,因
此MBR池中污泥进出同步进行时,进入的污泥量可抵消产生的污泥量。
7.2、设计参数:X——每日排放的剩余污泥量,kg/d;Qmax——设计流量,m3/d;Sr——BOD5降解量,kg/ m3;W——曝气池有效容积,m3;Xv——
MLVSS浓度,kg/ m3;f——系数,f=0.8;X——反应器内混合液平均MLSS浓度,kg/ m3;a,b——计算系数,取a=0.9,b=0.05;V1——SBR池产生剩余污
泥量,m3/d;p—污泥密度,p=1000kg/m3;
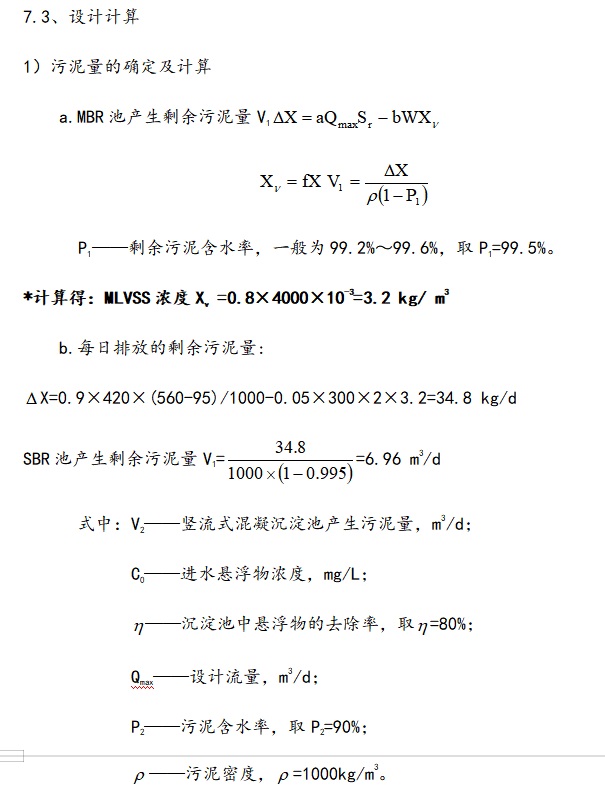
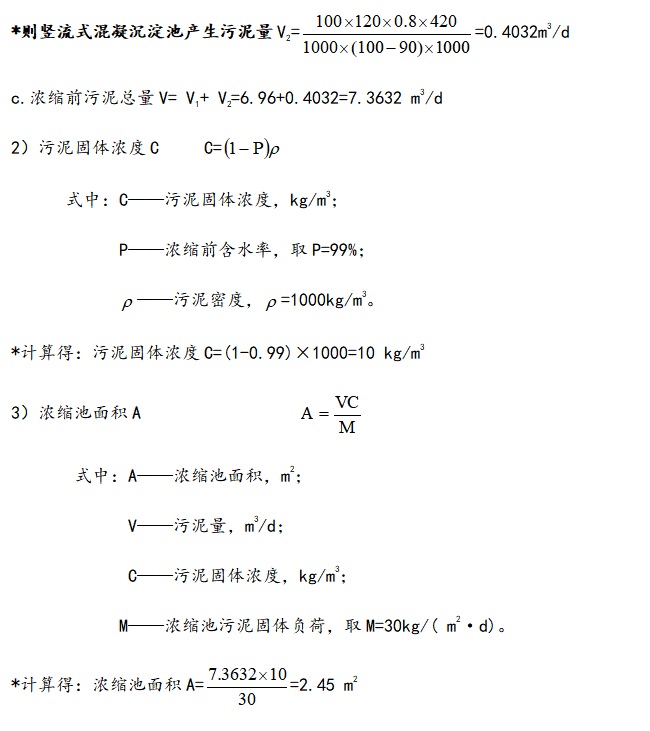
8)排泥周期T=V1/V2=1.09/2.45=0.44d,取排泥周期T=12, h。
8、消毒池
8.1、消毒池设计说明:深度处理工艺中经常采用的消毒方法有液氯消毒、氯片消毒、二氧化氯消毒、漂粉精消毒、次氯酸钠消毒和臭氧消毒。根据设计
的水量及水质,选择采用液氯进行消毒,去除渗滤液中的细菌和病毒,使出水达标,排放到水体接触消毒池选择一座六组四廊道式平流式消毒接触池。
8.2、设计参数:水力停留时间T=0.5h=30min; 消毒池有效水深h=2.0m;设计最大加氯量 =4.0mg/L; 一座消毒池格数n=2。
8.3、设计计算:
1)接触池容积V:V=Qmax X T
式中:V——接触池容积,m3;T——水力停留时间,h; Qmax——设计流量,m3/h;
计算得:接触池容积V=11.67×1.5×0.5=8.75m3
*校核:接触池长L=5m,消毒池宽B=2m,每格池宽b=1m;长宽比L/b=5/1=5,符合要求;实际消毒池容积V'=LxBxh=5×2×2=20m3;经校核满足有效停留
时 间的要求。
2)取消毒池超高h'=0.3m,接触池总高度H=h+ h'=2.0+0.3=2.3m
3)加氯量W =Pmaxx Qmax
式中:W——加氯量,kg/d;Pmax——设计最大加氯量,kg/m3;Qmax——设计流量,m3/d。
*计算得:加氯量W=4.0×10-3×420=1.68kg/d;选用储氯量为60kg的液氯钢瓶,每日加氯量为0.02瓶,共储用2瓶。
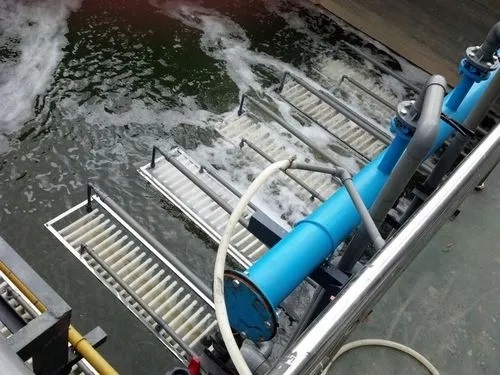
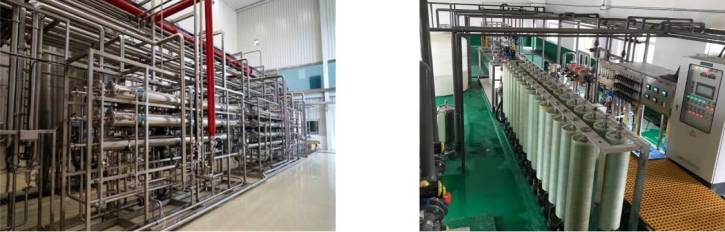
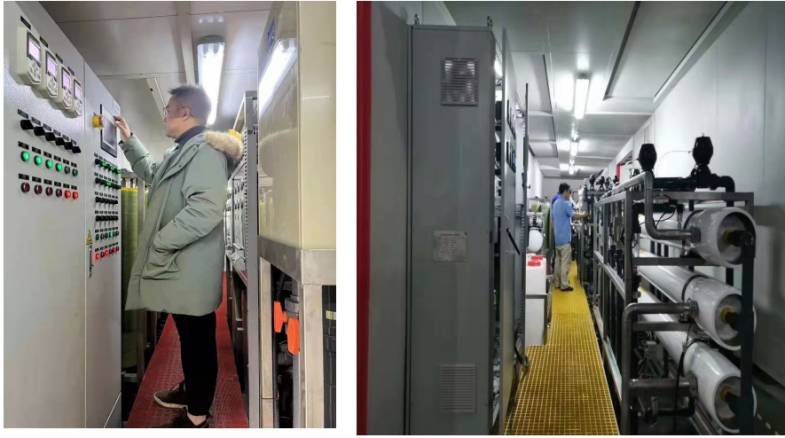
|