石油、石化企业中油泥分离处理是一个非常重要的环保难题,采用传统工艺即真空过滤加填埋或焚烧的办法,能耗高,浪费惊人,二次污染非常严重。目前业内把三相螺旋沉降离心机应用到油泥处理工艺中,效果十分明显,从根本上根除了传统技术的弊端。
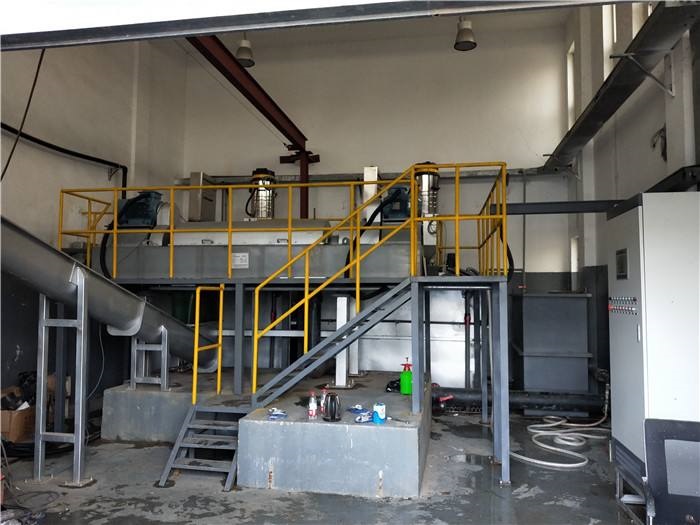
三相卧螺离心机主要由驱动部、转鼓及螺旋推进器构成,在电机高速驱动下,悬浮液中的固体颗粒瞬间沉降到离心机转鼓的内壁并通过螺旋推进器排出;二种不同比重的液体即水和油由于受到的离心力的不同(水的离心力大,油的离心力较小)而形成二个同心的液层通过溢流口分别分离出来;不同液体层的厚度可通过调节溢流堰和可变叶轮来改变,从而实现污泥、水及油的三相分离。经过三相卧螺离心机处理的干泥含水率和含油率都非常低,并且一次分离成功;一方面降低了运行成本,而且降低了对环境的污染。必须指出的是污泥排出含水量可通过调节堰板的直径解决,堰板的直径增大,排水区域增大,其含水率下;转鼓转速越高,分离污泥效果越小,分离效果更满意;同时转鼓和螺旋的差速越小,排除的污泥的含水量越低;进料的固体含量越高,所需的差数也越高。
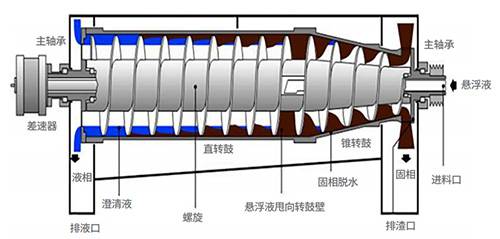
三相卧螺离心机应用到油田、石化行业的污泥处理时,整套系统的设计必须考虑加药系统、离心机、进料泵等要自动联动控制,在离心机超温、超压或缺药、缺料情况时会自动报警或停机;直接接触污泥及油、水的部件要高等级不锈钢材质;传动部件不但耐腐蚀性要好而且要耐磨性要高;另外为提高分离效果,一般要在离心机进口出设计自动加药装置加入絮凝剂和破乳剂,油泥分离的效果更佳。
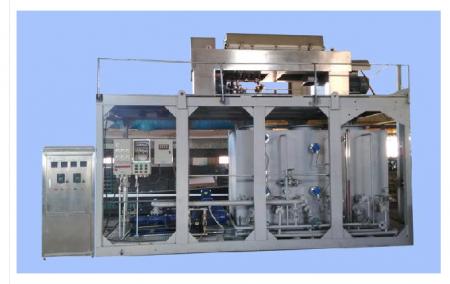
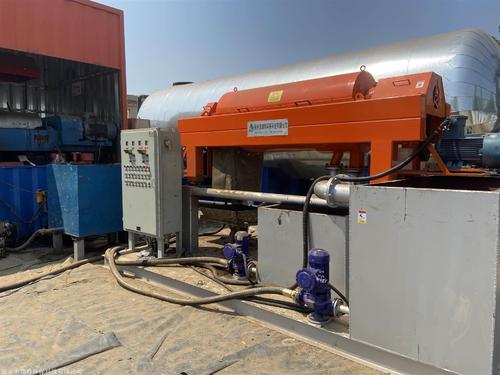
总而言之,三相卧螺离心机进行油泥分离的过程是一个全封闭、全自动、连续式工艺处理过程,占地面积小、生产自动化程度高、劳动强度低、工作环境相对较好。它必将取代传统的劳动强度较大,能耗高的油泥分离工艺设备。不久的将来在市政污泥的分离、食品蛋白淀粉分离等领域也必将更加广泛的应用。 |