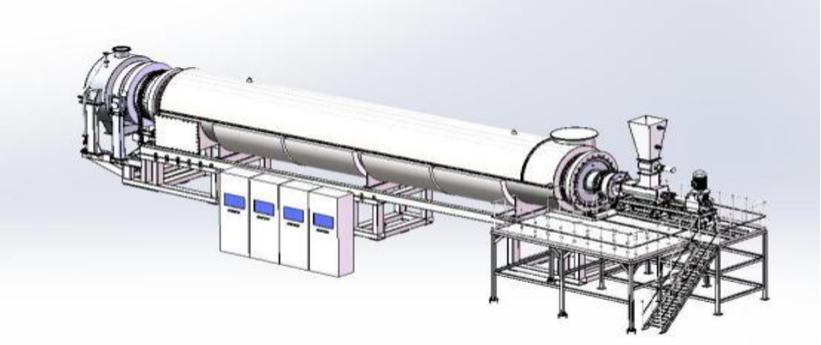
六、工艺流程
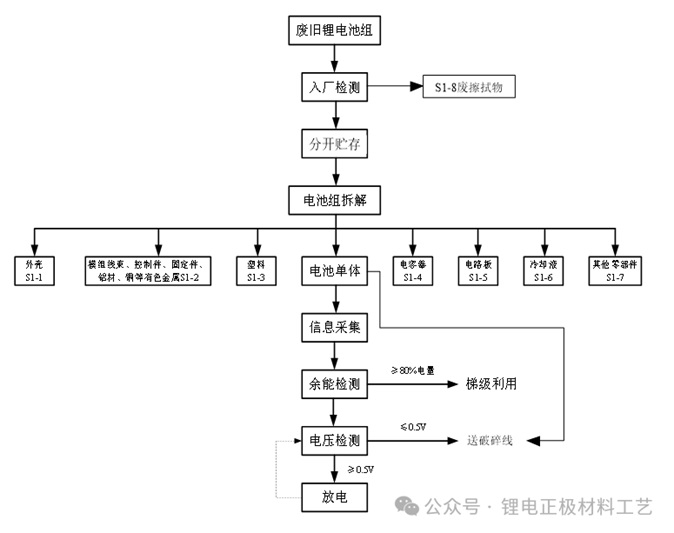
1、梯级利用工序工艺流程电池组进厂后具体前处理工序工艺流程介绍如下:
1)入厂检测、分区贮存:退役电池进厂之后进行人工初检,完好的电池单体堆存于原料区进入检测程序,漏液的电池拆解出的漏液电池单体直接进入破碎程序,不进入放电工序,拆解下来的其余组件用抹布擦拭干净,分别分类归入后续完好电池梯级利用后拆解过程产生的同类固体废物之中。完好的电池单体送入信息采集工序。
2)电池组拆解:
(1)废旧动力锂离子电池首先进行电池PACK包的拆解。首先对废旧动力锂离子电池包从外观、结构等进行安全评估,然后进行余电检测及绝缘耐压测试,快速放电将电池包中的多余电量通过余能储存装置储存起来,供局域电网使用;放电后拆除PACK包中的电池壳、铝外壳、电子元件、塑料等后得到电池模组,若冷却系统为液冷的电池包,还需抽入冷却液,冷却液采用专用容器收集后暂存于危废暂存间;对电池模组进行梯次利用测试,可梯次利用的电池模组作为梯次利用产品,不可梯次利用的模组进一步拆解,得到电池单体;对电池单体进行梯次利用测试,可梯次利用的电池单体组装成电池模组后作为梯次利用产品,不可梯次利用电池单体进入破碎系统。梯次利用电池按原材料的10%计,进入拆解系统的电池单体为原材料的67.5%(进入拆解系统的电池单体量=(原材料-梯次利用产品)*PACK中电池单体占比=(1-0.1)*0.7504*100=67.536%),即14806.92t/a。 (2)入厂检测时完好的电池组传送到电池组车间进行拆解。拆开电池组外壳,收集冷却液,拆除模组线束、控制件、固定件、铝材、铜等有色金属,电容器,电路板以及其他零部件等,得到退役磷酸铁锂电池单体,送破碎生产线。 (3)该部分产污节点主要为:S1-1外壳,S1-2模组线束、控制件、固定件、铝材、铜等有色金属片、线,S1-3塑料、S1-7电池包组其他零部件等一般固体废物;S1-4电容器、S1-5电路板、S1-6、S1-8废擦拭物等危险废物冷却液等危险废物。一般固体废物外售资源化利用,危险废物委托相应资质单位收集处置。
3)信息采集按照国家动力蓄电池回收利用过程中“建立动力蓄电池产品来源可查、去向可追、节点可控的溯源机制”的政策规定,单体电池在进行余能检测的同时,利用专门的国家网络信息平台,落实动力蓄电池的各项可追溯信息登记工作。即通过废单体电池编码可获取生产企业、电池类型、生产日期等信息。
4)余能检测废锂离子电池带电破碎有发生爆炸的危险,在处理前先进行余能检测。当锂离子电池的电压、容量达到设计值的80%,进行梯级利用。本厂区内,不对可梯次利用的单体电池进行处理。对于外观有变形、裂纹、烧坏、鼓胀、漏液等的动力蓄电池单体,为了安全起见严禁进行余能检测。
5)电压检测不能进行梯次利用的单体电池经进入电压检测工段。按照拆解技术规范进行电压检测,废旧电池单体拆解前残余电压应不低于0.5V。电池单体电压低于0.5V可去拆解车间进行破碎,高于0.5V的单体电池需要放电处理。
6)放电不能梯级利用的废电池进入经放电机放电,电压检测低于0.5V时,进入撕破工序, 拟建放电采用一体化放电机,不使用氯化钠溶液。
2、碳酸锂生产工艺流程:经梯级利用后余能不足的磷酸铁锂电池单体进入破碎机热解工序。破碎及热解工序除电池上料外均采用自动化设备作业,全程密闭,通过输送带或气动输送。热解输出极粉直接混合浆化,浆化后的物料通过管道泵到循环利用车间进行碳酸锂生产工序。具体工艺描述如下:锂电池单体投入破碎生产线,但主体破碎、分选工序均相同,生产设备和输送机均密闭设置,防止污染物的无组织排放。其中,输送机为适应废旧电池的输送而研发,在皮带机上增加了密封挡板和导料斗,防止废旧电池散落和外露,具体工艺流程如下:
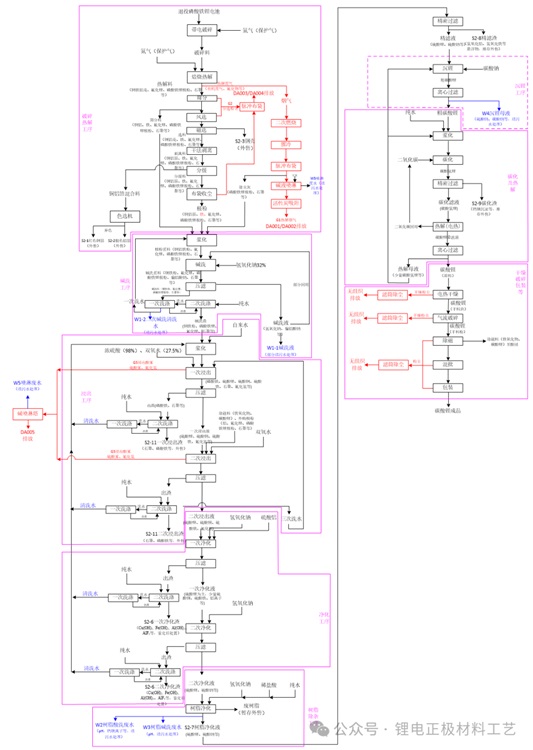
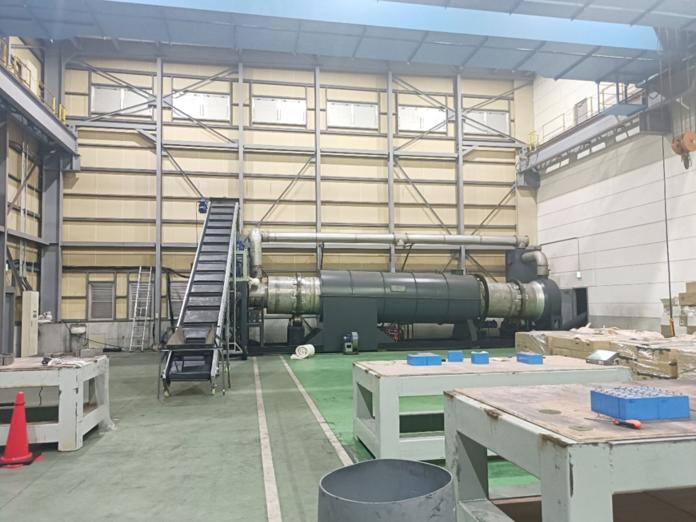
|