
一、概述:艾奇逊石墨化炉(Acheson furnace)是指以发明者艾奇逊的名字命名的一种石墨化炉。艾奇逊炉于1895年发明并首先在美国取得专利,它的雏形是:在耐火材料构筑的长形炉体内,装入炭的坯料和颗粒料,组成导电的炉芯,在炉芯的四周是绝热保温料。作为炉头的两上端墙上设置有导电电极,并与电源相连接,构成通电的回路。当电路接通,炉芯由于电阻的作用即发热升温,使炭的坯料在2200~2300℃的温度下,经高温热处理而转变为人造石墨。
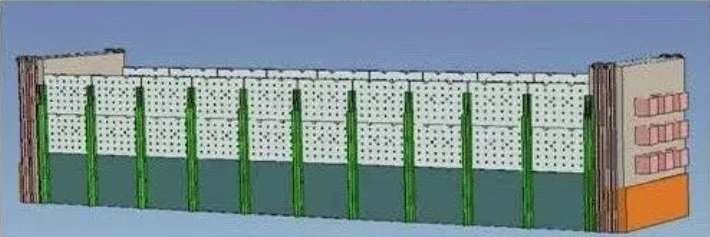
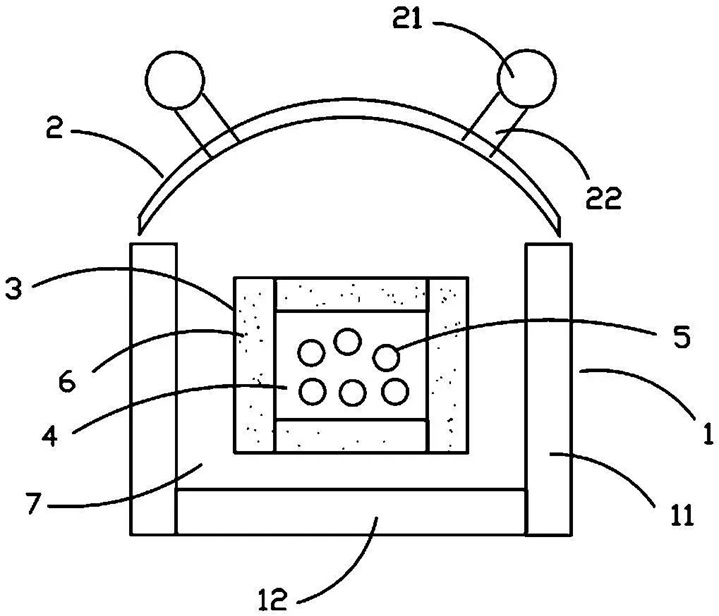
二、艾奇逊石墨化炉结构:艾奇逊石墨化炉(如下图所示)由耐火材料铺砌的型炉底(砌在钢筋混凝土基础上)和两个装砌有导电电极组的端墙组成,呈长方形分布。端墙的作用是固定导电电极组,其外侧砌耐火砖或炭块,内侧砌石墨块,墙体中部用石墨粉填充构成密封填料空间,数根导电电极(石墨电极)穿过端墙,导电电极直径和数量根据石墨化炉通电时的电流强度而定,相关石墨化石油焦产品参数供参考,在通电期间电极温度不断升高,因此要对导电电极进行冷却。炉身两旁用耐火砖砌成侧墙,也可用耐热混凝土制成的墙板立放在炉两侧代替炉墙。侧墙的作用是保证所装制品和辅助料所占据的空间。
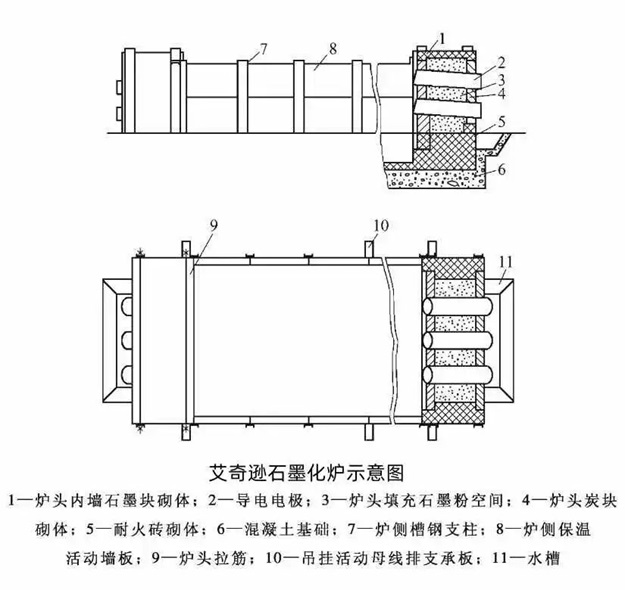
1、小型艾奇逊石墨化炉炉身长10~12m,炉身宽1m左右,每次可装20t左右焙烧品;中型艾奇逊石墨化炉炉身长14~16m,炉身宽3m左右,每次可装40~50t焙烧品;大型艾奇逊石墨化炉炉身长18~20m,炉身宽4m左右,每次可装100t左右焙烧品。
2、艾奇逊石墨化炉是全球应用得相当广泛的石墨化炉,自1895年发明后,在国内外得到迅速推广,在相当长的一段时间内,一直占据着石墨化炉的主导地位。
1)艾奇逊石墨化炉问世百年来也在不断地改进和完善,从交流炉发展到直流炉是其重大的技术突破。
2)一些主要技术指标(如送电时间、单位电耗)及产品质量都得到大幅度改善,但艾奇逊石墨化炉的固有缺点,如热效率低、单产能力小、温度不均匀等缺点依然存在。
3)串接石墨化炉的应用结束了艾奇逊石墨化炉一统天下的局面。石墨化市场资讯,关注我们更多了解。
三、艾奇逊石墨化炉与厢式炉、连续化石墨化炉的比较?艾奇逊炉坩埚法是目前石墨化主流生产工艺。
1、按照加热方法不同,石墨化主要有间歇式和连续式两种生产工艺。
1)间歇式石墨化过程中物料需要经历装炉、升温、石墨化、降温断电出炉等工序。
2)以目前主流的艾奇逊炉为例,石墨化过程主要包括将负极材料均匀放入石墨坩埚内,再通过天车吊起平放入石墨化炉中,将电阻料放入炉芯处石墨坩埚外围,再包覆保温料,将炉体填满,即完成装炉。
3)将炉体装满后,即进入电加热过程,通过石墨化炉两侧的电极进行通电加热,在炉内达到一定温度后加盖炉顶并设置集气罩,炉内温度将继续升至2800 - 3000 ℃,最终将坩埚内含碳物质在高温热处理下,实现减少无定型碳微晶结构边缘杂质,使其具备石墨晶体结构特征。通电加热结束后,将炉顶打开,静置冷却至材料恢复常温,即结束该生产过程。
4)通常情况下,石墨化工序或提纯工序一个周期将达到15-22天。连续式石墨化具有成本、效率、环保等方面的优势,成为产业化探索新方向。
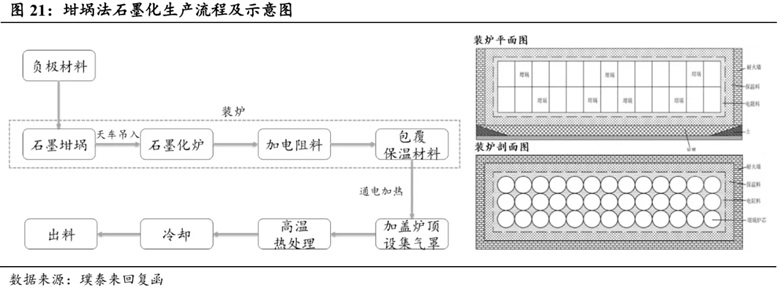
2、连续式石墨化生产过程中没有断电,石墨原料经过一系列的温区从而实现连续石墨化。
1)其原理是先将备好的粒度为1~30 mm的散状石油焦由上料装置送入进料斗,经过干燥、煅烧阶段,将产生的蒸汽和挥发分排出;而后进入高温区完成石墨化;最终进入炉底冷却器,冷却到200~300 ℃时,打开冷却器底部的闸板出料,自然冷却至室温。
2)连续石墨化具备以下优势:
(1)热能利用率更高(连续法25%,艾奇逊法10-15%);
(2)生产辅料节约,设备法几乎不消耗辅料,艾奇逊法没生产1吨产品大概消耗4吨辅料;
(3)废气集中处理,对环境友好,连续法生产过程密闭,由专门的辅机收集处理废气,艾奇逊法是敞开式冶炼环境,无法有效收集废气);
(4)碳排放很低,设备法仅为艾奇逊法碳排放当量的25%;
(5)设备法生产组织模式具有连续性,中间产品“不落地”,节省大量人力、运输运转费用。
3)根据山河智能反馈,行业艾奇逊法平均耗电8000-14000度/吨,而连续法耗电量将比传统艾奇逊法降低30%左右且辅料大大减少。但目前看实现连续石墨化升温至2800度以上相对困难,且由于其生产过程密闭杂质气化易使炉内压力过高。目前贝特瑞、山河智能等企业在尝试突破中。 |