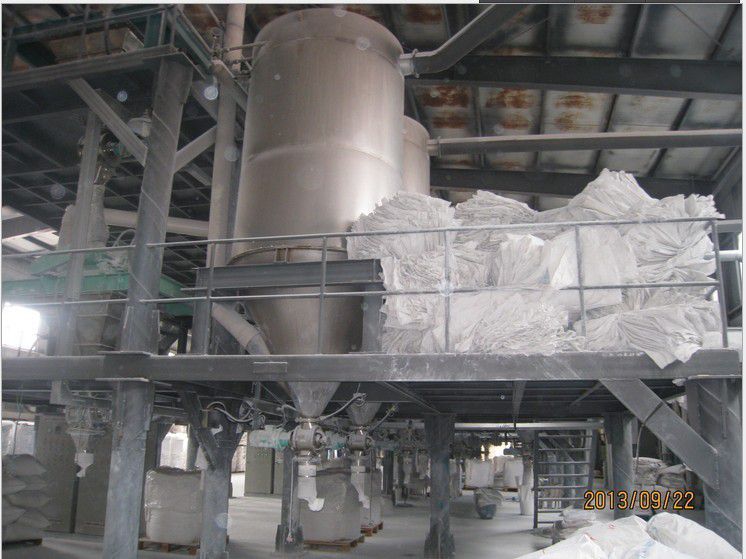
3、节能降耗改造生产工艺原料由原有钛渣和钛精矿调整为钛精矿,后煅烧的物料量(主要为钛精矿)和硫酸(新酸)用量都相应增加,其增加原因主要由于全矿后钛矿品位比钛渣低,使用全矿工艺硫酸消耗量会增加。
1)原矿粉碎:原料由原有钛渣和钛精矿调整为钛精矿,将钛精矿送入带热风干燥的风扫 磨粉碎和干燥,经分级后,粒径合格的矿粉风送酸解工序。粉碎工序中产生少量的粉尘 经袋除尘器达标排放。
2)连续酸解:为提高废酸利用率、提高酸解率,由原间歇酸解工艺调整为连续酸解,新建两套连 续酸解系统,原间歇酸解设备拆除,酸解主要是将原料中的二氧化钛用硫酸分解成可溶 性硫酸氧钛。 ①反应控制条件
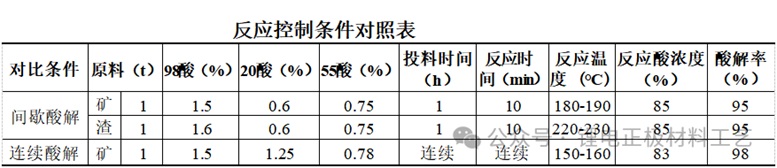
②连续酸解工艺 (1)原料系统 *原矿——从磨后矿仓经气力输送到酸解储料仓,仓上设有除尘系统,防止粉尘冒出, 矿仓配有称重系统。 *硫酸——98%硫酸从硫酸储罐区经硫酸泵送至楼顶阳极保护冷却器、降温后送至两 个浓硫酸高位槽通*过流量计、温度计、气动调节阀等仪表设备远程控制实现高位槽液位 恒定不变,温度保持,然后分别按设定流量送至每套预混系统。 *稀酸——稀酸利用稀酸储槽,经流量计、气动调节阀按设定流量送至每一套反应器。 98%酸+20%酸+55%酸→83%酸(反应酸浓度) *主要由98%酸与20%回用酸、经废酸浓缩装置浓缩的55%酸配置成83%酸,用于酸 解浸取酸。 (2)钛液制备系统 *预混——浓硫酸来自高位槽,通过电磁流量计、气动调节阀按设定流量进入预混槽, 预混槽设计按30min混合时间,装矿粉量约8吨,浓硫酸12吨,并配有称重系统,通过仪 表设备使酸矿按设定比例实现自控联锁,从而保证酸矿比例。然后利用预混搅拌使酸、矿充分混合后自动下料进入反应器供料槽。 *为防止酸矿自身温度偏高,混合时有放热反应,预混槽设冷却水夹层,温度较高时 可自动开阀放冷却水,通过预混槽壳体换热给酸矿预混料降温达到连续安全稳定生产。 *反应——供料槽将已经混合好的混合物料由流量泵泵入反应器中,泵输送能力需达 到15m3/h ,因据产品产量要求,输送量要大约在10.3m³/h左右。为了能使浓硫酸与矿粉发生反应,还需要加入稀酸稀释浓硫酸,稀酸加入量通过测量稀酸酸含量及酸矿比例 进行计算。稀酸通过流量计、气动调节阀和硫酸计量系统联锁实现按设定比例流量进入反应器,在稀释过程中放出大量的热,酸矿会发生持续性反应,利用反应器搅拌使酸矿充分混合,确保充分反应,持续反应。 (3)溶解系统:反应生成的固相物从出口处溢出进入一级溶解槽,同时溶解槽内按比例加入工艺水或稀酸,利用溶解搅拌使固相物充分溶解生成钛液,当液位达到溶解槽上部的溢流出料 口时,钛液和部分未完全溶解的固相物溢流进入二级溶解槽,并利用机械搅拌进行二级 充分溶解,当充分溶解后输送至还原槽。为防止钛液高温水解,一二级溶解槽都设有盘 管以便冷却水进入,以便控制溶夜温度,需小于60℃ , 一二级溶解槽都设有温度传感测 量器,通过温度传感器反馈信号至中控系统,然后控制输送冷却水的流量。 (4)尾气处理系统:酸解反应产生的尾气中含有大量的SO2 、SO3 、硫酸雾等物质,每台反应器系统的 烟气从管道出来经负压送去原酸解尾气处理系统。 3)钛液 VCE 连续结晶:VCE连续真空结晶系统为本次新增装置,原因采用渣矿混合工艺,工艺过程无硫酸亚铁产生,建设有钛液浓缩装置(薄膜蒸发器,无结晶装置)。 (1)预冷段工艺说明:预冷段正常情况下使用自来水,入口水温 20℃,自来水流经两级预冷冷凝器,使水温上升 10℃,热钛液由上工段由输入到本系统入口,温度50~60℃,出口压力0-0.1MPa。热钛液自1#预冷蒸发罐循环泵入口与强制循环钛液一起被吸入循环泵。级1#蒸发,降温后流入2#预冷蒸发罐循环泵入口,与2#强制循环钛液一起被吸入循环泵,进入2#预冷蒸发罐,经2#预冷蒸发罐出来的钛液温度降至35-40℃。 *每次系统启动时,先不抽真空,打开给料阀,待中温钛液槽注入钛液量不少于 2 米时(可在参数表里设定),启动真空机组,然后开强制循环泵。 *结晶段是分批次进行的,每次启动时,向钛液槽注入钛液后,开搅拌电机,开真空 机组,待真空度达到 10KPa 以后,开循环泵,然后再补料,再开凉水塔、凉水循环泵 及冷冻水循环泵,再开冷水机组。期间真空机组,冷水机组均正常工作。冷冻水温度自 2-25℃之间。当要停止结晶时,先停冷水机组,再停凉水塔及冷热水循环泵,再停真空 机组,再排真空。 (2)结晶段工艺说明:结晶段是分批次进行的,每次启动时,向钛液槽注入钛液后,开搅拌电机,开真空 机组,待真空度达到 10kPa 以后,开循环泵,然后再补料,再开凉水塔、凉水循环泵及 冷冻水循环泵,再开冷水机组。当钛液温度降到 20℃,启动转料泵,将钛液槽内的冷 钛液转至钛液槽。 (3)亚铁分离工艺说明:两套 30m2 圆盘分离系统,对结晶槽内结晶料浆通过结晶钛液泵泵至离 心脱水机进行过滤,过滤后滤液自流进入清钛液贮槽贮存,过滤后亚铁固体从溜管至亚 铁临时库房存放或直接用车装走。过滤的亚铁洗涤时启动洗液泵泵送至需要洗涤的离心 脱水机洗涤亚铁滤饼,洗液自流回洗液槽循环使用。洗液槽洗液循环洗涤至一定钛浓度 后泵送至小度水贮槽回用。 4)MVR 钛液浓缩
(1)清钛液从进料泵进入 MVR 蒸发系统,进料通过凝水预热器、蒸汽预热器两级预 热将物料温度预热至~62℃ , 然后进入降膜蒸发器。 (2)物料在降膜蒸发器内逐渐蒸发浓缩时,当系统物料浓度通过质量流量计自动在线 检测,达到出料设定浓度时,合格浓缩液通过出料泵打出系统;出料未达到出料设定浓 度时,浓缩液出料阀关,物料返回蒸发器继续蒸发浓缩直至达到要求的出料浓度。浓缩 液出料的瞬时流量、累计流量通过流量计进行指示监控。
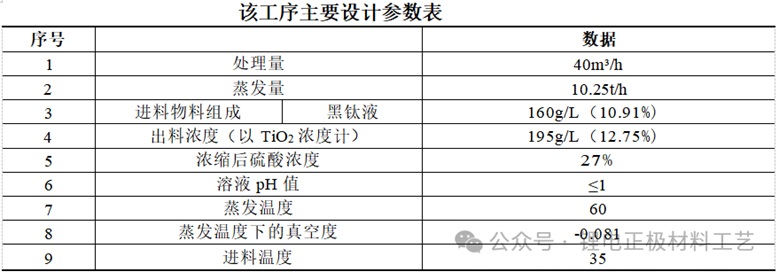
5)控制过滤-水解工序
(1)由酸解-沉降工序来的钛液送至钛液板框,加入硅藻土助剂(作为过滤介质,最后 随滤渣进入污水处理站)进行二级控制过滤,进一步除去钛液中的细颗粒杂质及部分胶 体杂质后进入钛液贮槽,产生的细颗粒杂质及部分胶体杂质即滤渣用酸解尾气处理后废 水打浆后进入厂区污水处理站处理。 (2)精滤后的钛液由钛液泵送入浓钛液预热槽,通过蒸汽盘管加热,预热至工艺要求温 度后卸料至水解锅。钛液在水解锅内完成水解反应,使硫酸氧钛转化为偏钛酸。水解后 的偏钛酸经自流进入偏钛酸贮槽,泵至石墨冷却器冷却后送至水洗工段。 (3)废酸主要来自于水洗工序,H2SO4 浓度 20~22% ,企业配套建设了一套废酸浓缩装 置,将产生的废稀硫酸浓缩至一定浓度(55%),通过压滤机除铁后,返回钛白系统(7.51 万吨/年),其余外售科技股份有限公司(1.57 万吨/年)。
6)水洗-漂洗工序 (1)水解工段送来的偏钛酸浆料泵至吸片槽中,用叶滤机真空吸滤上片,当叶滤机吸片厚度达35~40mm时,将叶滤机提至水洗槽中用50℃左右温水进行水洗。水洗合格 后,将叶滤机提至卸料槽,偏钛酸经刮片打浆后用泵送至漂白罐中。 (2)水洗吸片酸用CN 过滤器进行回收。回收后的清废酸部分回用至酸解作为浸取酸使 用,多余的稀酸进入废酸浓缩系统浓缩后回用。 (3)煅烧晶种制备:每生产 1 万吨钛白粉需煅烧晶种 570 吨。采用自生晶种常压水解工 艺使 TiOSO4 生成偏钛酸(H2TiO3 ),该法水解率可达 96% ,水解后的偏钛酸物料颗粒 均匀、粒度分布窄,有利于水洗工序。 (4)二洗滤饼打浆后送至偏钛酸计量槽,计量后调浆至规定浓度后进行预热,预热至规 定温度后自流放入碱溶槽,与碱溶槽内已预热好的液体 NaOH 进行反应,生成钛酸钠, 保温熟化并经冷却后送至钛酸钠贮槽。然后泵入隔膜压滤机过滤洗涤,除去 NaOH、SO42- 等杂质,打浆后送至酸(胶)溶槽中与盐酸(30%左右)发生反应,生成金红石晶型的 溶胶,即煅烧晶种。制好的煅烧晶种放入晶种贮槽备用。晶种制备过程中产生含 NaOH 的碱性废水(约 15%)送酸解和煅烧工序作尾气洗涤补充水。 (5)煅烧晶种的制备化学反应式为: 碱溶:H2TiO3+2NaOH→Na2TiO3+2H2O 酸溶:Na2TiO3+2HCl→TiO2·+2NaCl+H2O (6)煅烧晶种制备流程见下图。
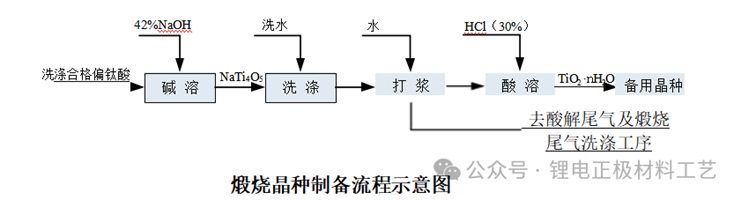
7)盐处理:在偏钛酸中加入盐处理剂(磷酸、氧化锌、氢氧化钾、三氧化二锑),混合均匀后 直接泵至煅烧工序偏钛酸料浆贮槽。
8)煅烧工序 (1)盐处理后的料浆送至煅烧工序偏钛酸料浆贮槽,由泵送至隔膜压滤机进行压滤,滤 液送入煅烧工序作为煅烧尾气洗涤水,滤饼卸至偏钛酸贮斗,底部皮带输送至加料螺旋加入窑内进行煅烧。 (2)随窑的转动,物料向前移动,经与高温气体逆流接触,逐步完成脱水、脱硫以及晶 型转化至窑头落入下料管,经双翻板阀至冷却转筒同空气进行间接热交换后被冷却。从冷却转筒出来的物料由葫芦吊吊至大料仓、贮存并供给成品破碎的雷蒙磨进行粉碎。 (3)煅烧工序主要反应方程式如下:H2TiO3 →TiO2+H2O↑
9)成品破碎:煅烧后的金红石钛白粉物料直接经雷蒙磨粉碎至合格粒径后即得钛白粉成品,粉碎 时产生的尾气含有细粒的产品,采用滤袋收尘系统进行回收,尾气达标后排放。中间粉 碎前粒径 1-3mm ,中间粉碎后 0.4μm。
10)汽流粉碎:气流粉碎为新增设备,不替代或改造现有雷蒙设备,建设气流粉碎系统主要目的是 对现有产品进行质量升级,进一步提高产品消色力、粒度分布均匀等质量指标,收集在 粉前料仓内经过现有雷蒙磨设备初步粉碎的TiO2 由进料螺旋输出,物料在高压过热蒸汽 引导下进入汽流粉碎机进行粉碎(汽流粉碎前0.4μm ,汽流粉碎后0.35μm),同时计量 泵加入工艺要求量的助剂,在此大部分物料被粉碎至原级粒子后被送入汽粉袋滤器,微 粉化TiO2在高温袋滤器中与蒸汽分离出,收集在汽粉袋滤器下部,干净蒸汽被导入冷却 器用脱盐水喷淋,喷淋水经集水槽汽水分离器分离后去前工段洗涤水槽,不凝性气体用 风机排空;收集在汽粉袋滤器下部的物料经喷射器与冷空气混合后送至低温袋滤器,物料在此 处与空气分离后,收集在其下部,送入成品贮仓。
11)包装:成品贮仓内成品由全自动包装系统按工艺要求进行准确的称量、包装、打码、码垛、 整形、缠绕等自动化程序后,再由成品叉车运送至成品库房存放。

|