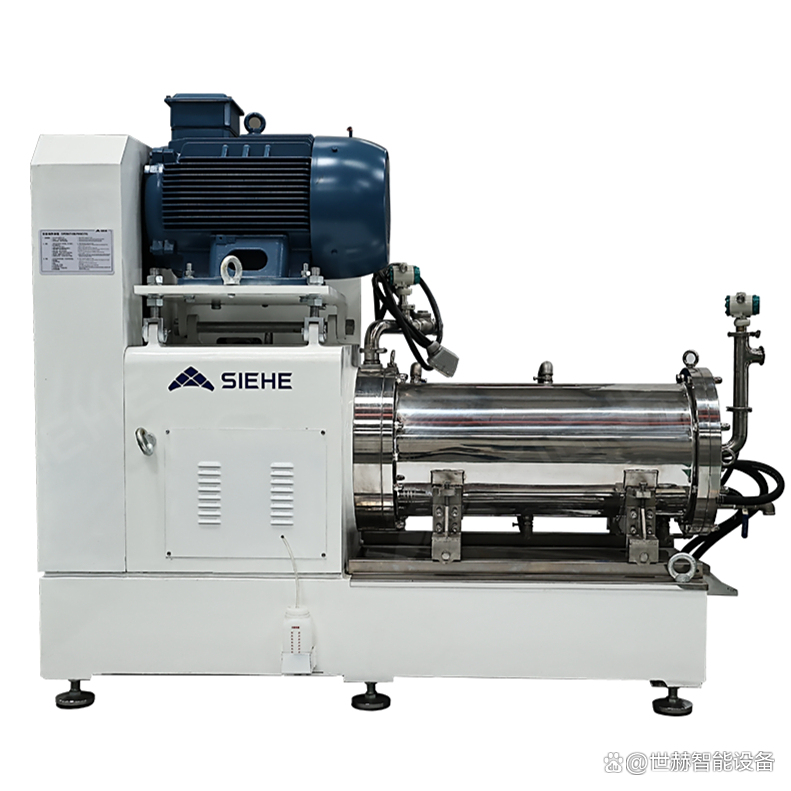
5、砂磨机选择:首先,立式砂磨机由于避免了密封方面的问题,在制造上就较为容易,成本造价较低;所以立式砂磨机更加适合一些对产品要求比较低,但产量较大的研磨产品。其次,卧式砂磨机的制造成本较高,但它能保证物料的密封性,防止产品的污染,较好的保证产品的纯度,适合一些要求高精度和高细度的产品。
6、砂磨机工艺流程

1)粗磨:粗磨采用ABC倒罐研磨方式,通过程序进行控制,根据设定A罐子接受上游浆料或者输送浆料至下游工艺,当A罐完成作业时与B罐组成AB罐循环研磨即A罐→砂磨机→B罐→砂磨机→A罐循环作业,C罐代替A罐做承上启下作用,如此周而复始做到砂磨机完全不停机。
(1)进入砂磨机的浆料首先要经过2串2并的过滤、除铁器,砂磨过程中循环除磁,可以减少异物带入。 (2)研磨好的浆料经过2串2并的过滤、除铁器后通过泵浦输送到精磨罐待精磨。 (3)过程全程自动控制,可在砂磨机屏上进行手动操作。设备操作屏都有端口接入中央控制室,在控制室即可集中监控各设备运行情况。
2)精磨:精磨采用ABC倒罐研磨方式,通过程序进行控制,根据设定的研磨方案,任意两个精磨罐作AB倒罐研磨,C罐作为接上游料或者作输送至下游的动作,即A罐→砂磨机→B罐→砂磨机→A罐循环作业,同时C罐接受上游浆料;当砂磨机研磨完成时,C罐和AB罐中的其中一个空料罐组成一个循环研磨作业,装有研磨好浆料罐同时向下游输送浆料直至完成后开始接受上游浆料,如此周而复始做到砂磨机完全不停机。 (1)进入砂磨机的浆料首先要经过2串2并的过滤、除铁器,砂磨过程中循环除磁,可以减少异物带入。 (2)研磨好的浆料经过2串2并的过滤、除铁器后通过泵浦输送到除磁罐待除磁。 (3)过程全程自动控制,可在砂磨机屏上进行手动操作。设备操作屏都有端口接入中央控制室,在控制室即可集中监控各设备运行情况。
3)除磁:除铁采用A罐循环方式,当AB罐除磁循环作业时,C罐除完磁的浆料进入喷雾系统喷雾作业,当C罐浆料用完后通过程序自动切换到已经完成罐再进入喷雾作业,同时B罐打入待除磁浆料,程序同时切换到除铁器与B罐进行单罐循环除磁作业,周而复始。
7、研磨介质选择与填充

1)研磨介质也简称研磨珠,最早期是用天然砂(所以称为砂磨机),后来发展到玻璃珠、硅酸锆,现在基本都是用氧化锆珠,氧化铝珠等。(所以现在砂磨机也叫珠磨机)。 2)为了达到好的研磨效果,选择的研磨介质的规格及材料要适当。研磨介质选择参考三个依据:污染情况、介质材料及直径、效率。 3)在研磨生产过程中介质通过速度改变来传递部分能量,达到研磨效果。当搅拌速度一定时,能量的释放与研磨介质的数量有关。当研磨介质数量与搅拌速度一定时,还与介质的密度有关。质量相同时较大直径的研磨介质,也能够达到相同的效果。但有一点,相同质量研磨介质数量减少,效率降低。在具体操作中必须考虑研磨介质的效率,包括3个方面:研磨介质的需求量、功率的消耗和研磨容量。 4)研磨介质对研磨效果和效率有很大的影响,一般地,细度要求越细就要用细珠, 细度大可以用大珠﹔粘度低的可用小珠,粘度高的要用大珠。另外,密度大的珠子研磨效率会高一些(但对研磨腔磨损也会大一些,对动力要求会高一些)。 5)圆度越好,表面越光亮的珠子对研磨效果和效率都会好一些。珠子越硬就越耐用并不易破裂。 6)一般地,研磨介质直径应约为原料细度的 20 倍或成品平均细度的 1000 倍。
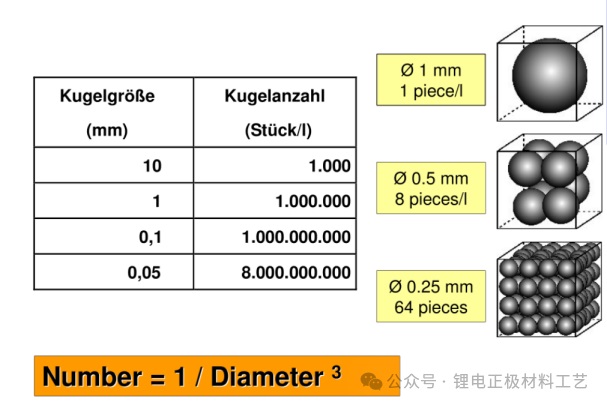
7)研磨介质有以下情况请不要采用:可使产品变色,与产品发生化学反应,介质磨损和破碎会产品产生影响。不同的行业和物料,对防止污染的要求也不同。 8)如果产品的要求很细而原料的颗粒又太大,有时不得不采用不同直径的介质装到几台砂磨机进行串联分步加工研磨。 9)研磨介质填充率与开磨效率关系很大。填充率过高,加速设备磨损,温度高,过低则效率不高。填充率要与浆料的温度细度各项指标综合考虑。关于研磨介质填充量,要考虑研磨介质的材质和粒径再进行选择,最优填充量为70%-80%;如果物料体质颜料较多、细度要求不高、物料易发热时,研磨介质应控制充填量在60%-70%,才能提高能量输入和产品产量,提高研磨率。研磨介质的填充率一般为50-80%为宜。原则是:白色或低温度要求的产品添加 55%左右,深色为 70%起渐量添加。 10)相同材质的珠子,大珠子和小珠子的堆积密度基本相同,差别不大。填充量(kg) =研磨桶有效研磨空间(L)×研磨介质的比重×填充率 11)常用研磨介质比重(单位:Kg/L):玻璃珠(1.5),硅酸锆珠(2.3),80 锆珠(3.2), 95 钇稳定纯锆珠(3.6),95 铈稳定纯锆珠(4.0);例:锆球总重量G=3.6*400*0.8=1152(kg)其中3.6为锆球堆积密度,400为研磨机容积,0.8为填充比例。
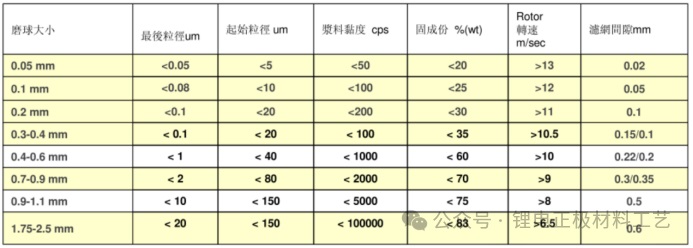
|