
六、POLE碰撞
1、按照E-NCAP中的柱撞试验条件,对Model 3进行侧面75°、 32km/h柱撞分析。
1)如图30所示,门槛梁则为主要变形吸能区,其中门槛内板外板均采用高强度钢板材料,而门槛加强板则采用“目”字型挤压铝材,极高的提升了门槛的承载能力,可对应包括pole碰在内的侧面碰撞,同时可起到了轻量化的作用;
2)门槛与地板座椅横梁错位焊接,座椅横梁处于柱状碰撞器碰撞路径范围,可有效抵抗乘员舱的变形。
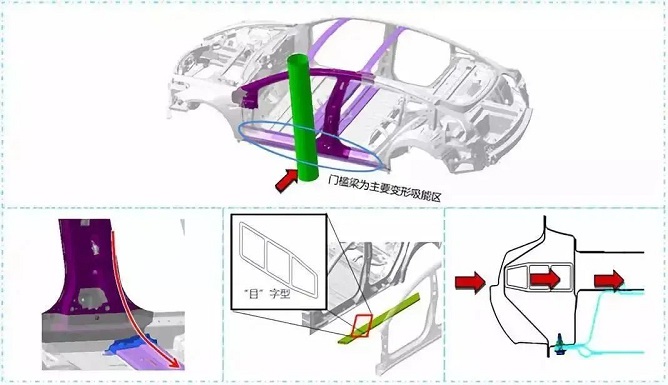
图30 应对POLE碰撞门槛处结构示意图
3)如表30所示,门槛断面系数及惯性矩均高于同类车型, “目”字型挤压铝提供了主要贡献。
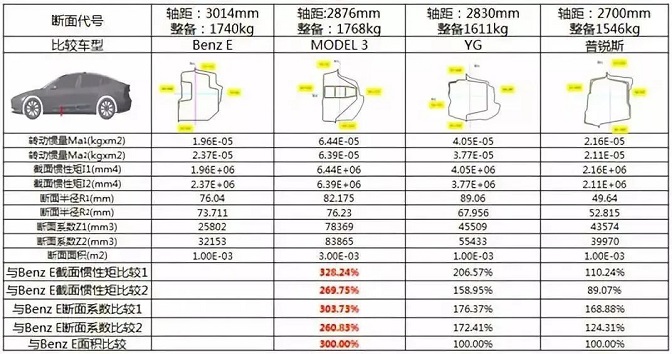
表31 Model 3与竞品车型门槛断面系数对比
2、对于电动车,柱状试验除了考虑乘员安全外还主要应对电安全问题。(电池包受柱状挤压有可能导致起火燃烧)。
1)Model 3电池包设计未做侧向支撑结构,侧碰(包括pole碰)电池防护主要由车身结构建立(如图32)。
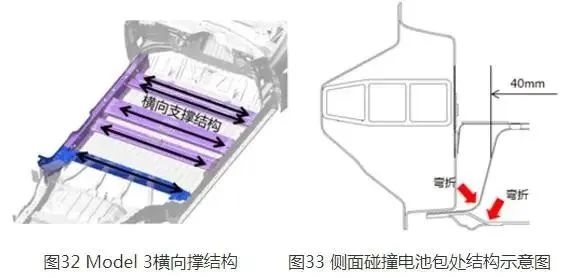
2)如图33所示,电池包与门槛间距约为40mm,POLE碰撞时电池包有一定挤压风险,电池包上下板均设计了弯折特征,控制POLE碰撞的变形模式。
七、后面碰撞
1、多条碰撞传递路径。
1)如图34所示,车后部均为铝材,考虑铝纵梁的吸能效率要优于钢纵梁,整车压溃量全部集中在后防撞梁和后纵梁后端部分。
2)后纵梁断面Z向高度高于传统车型,且为“日”字型结构,轴向刚度大,压溃时能吸收更多的能量,并拥较好的轴向压溃稳定性。
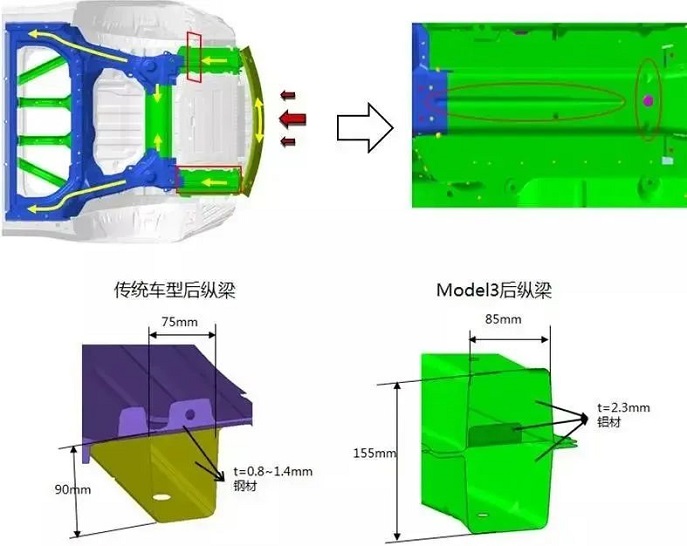
图34 后纵梁结构示意图
3)如图35所示,车身后部设计了3个 “环形”框架,形成了封闭的传力结构。后部碰撞中,第一层“环形”框架主要采用铝材,是储物和溃缩吸能区域;第二层“环形”框架主要采用高强度钢板,主要保护电机在后碰中的安全,同时后副车架对其进行了双重保护;第三层“环形”框架也采用高强度钢板,主要是对电池包进行安装及保护。
4)后保险杠总成整体采用活连接结构,可在低速碰撞后进行维修,撞梁本体采用“目”字型铝材,轻量化的同时可保证有效溃缩,防撞梁X向超出后行李箱盖50mm,可保证行李箱盖在后部低速碰时安全性。
5)Model 3的这种结构可对应后部的多种碰撞。
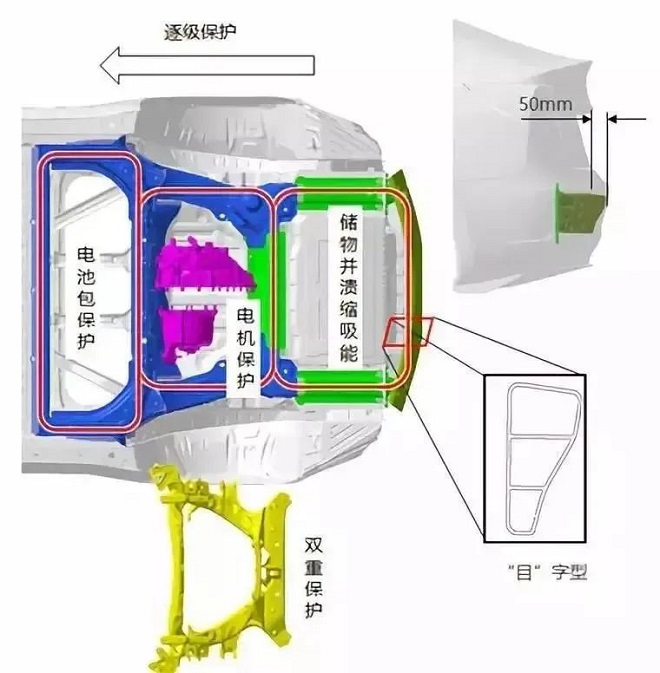
图35 后面碰撞环形框架示意图 |