
3).CTC(Cell To Chassis) (1)CTP 技术有效提升了 Pack 层级的成组效率,但仍然存在 Pack 与整车耦合的过程。如果能够将 Pack 取消,直接将电芯集成到整车或底盘上,将进一步提升电池的成组效率。 (2)正是基于这一目标,近年来新能源整车和动力电池企业都在探索电池与整车一体化集成技术。 (3)电池与整车一体化集成技术根据底盘和车身是否可以解耦可以划分为 CTC(Cell ToChassis,电芯集成到底盘)和 CTB(Cell ToBody,电芯集成到车身)两种路线。 (4)CTC 技术主要应用于非承载式车身,整车有完全独立的底盘,且底盘与上车身解耦,可以根据需要更换上车身。 (5)CTC 与线控底盘系统、域控集成、整车热管理集成和高压电气集成一起组成一体化底盘集成技术的五大关键特征,图 9 为某 CTC 一体化底盘。
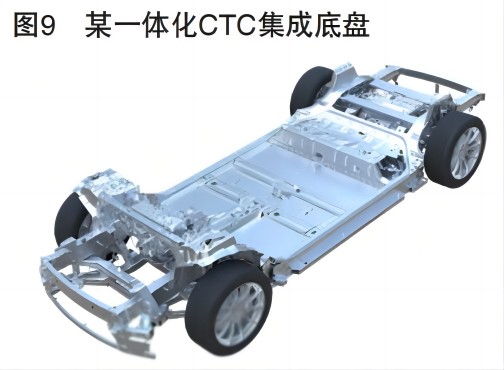
4).CTB/MTB(Cell/Module To Body) (1)CTB/MTB 技术即 Cell/Module To Body,电芯或模组集成到车身,主要应用于承载式车身,是传统 Pack To Body 技术的延申。 (2)特征是将电池 Pack 的上盖和乘员舱地板进行集成整合,从而在 Z 向上额外获取 10~15mm 的空间,或用于布置电池,或用于提升乘员舱总体高度。
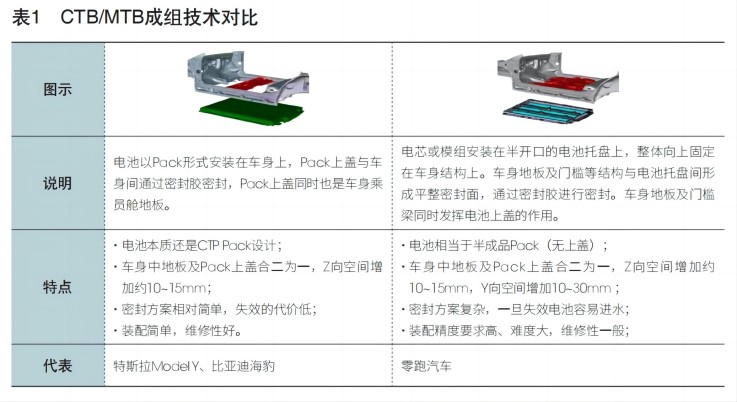
(3)表 1 为两种 CTB/MTB 成组技术对比。零跑汽车宣称其 MTB 技术相对于传统电池包方案零部件数量减少 20%,电池布置空间提升 14.5%,同时得益于大量高强度钢的使用,整车扭转刚度提升了 25%。
5).MTC/MTV(Module To Chassis/Vehicle):对于商用车来说,电池系统的配电量比较大,动辄 200~450kWh,甚至更高;同时商用车小批量多品种的属性特点要求整车的电量配置可以灵活调整,同一个底盘平台产品可能要兼容多个电量配置,且电量跨度也大;此外整车的应用工况也较乘用车更加恶劣,这些特点要求商用车电池具有更安全的界面性能和出色的可维护性,因此 MTC/MTV 技术应运而生。 MTC/MTV 技术是将模组直接集成到底盘或整车的技术。这一技术虽然保留了模组,但由于其具有独立的机械强度、电气设计和一定等级的防护性能,以及标准化对外接口和清晰的性能界面,可以省去 Pack 层级的结构部件,因此,可以更充分的利用底盘或车身空间;此外模组可以灵活的串并联组成不同电量的系统,兼具良好的维修性能,能够适应复杂的应用场景和严苛的工况要求。图 10 为重卡和客车 MTV 应用方案示意。
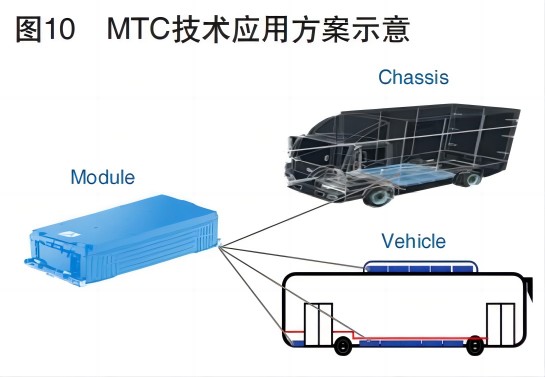
6).电芯倒置与侧躺:在各种成组技术的实际应用中,电芯基本都是正立放置的(主要指方壳电芯)。 (1)2022 年 6 月宁德时代发布麒麟电池,首次提出了电芯倒置成组方案,可以提升 6% 空间利用率。 (2)2023 年 12 月,小米汽车发布的 SU7车型,是全球首款搭载宁德时代电芯倒置电池的车型,如图 11 所示。
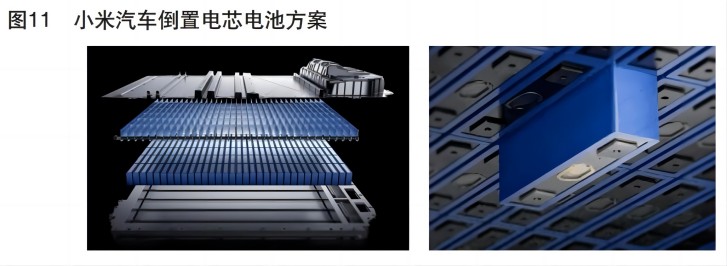
(3)电芯倒置方案可以将正立方案中电芯极柱上方用于 Busbar、绝缘片、采样线等部件的空间,与为满足底部球击标准要求而设计的电芯底部缓冲空间合二为一,进而在 Z 向尺寸上额外挖掘出 5~10mm,实现空间利用率的提升。
(4)此外,由于电芯泄压阀朝下,配合Pack 独特的泄压路径设计,可以保证电芯在热失控情况下快速向下释放热量和压力,从而最大程度保障上方乘员舱的安全。

|