
从油井中开采出来的原油中都含有一定量的水和盐类物质,因此一般在油田会对原油进 行脱水(盐)处理,使外输原油达到一定标准(我国 BS&W≤0.5%、含盐 50mg/L);出于避免催化剂中毒、减轻设备和管线腐蚀结垢等方面的考虑,炼油企业对原油质量的要求更高,因此原油炼制加工的首要工序(位于常减压蒸馏装置之前)就是进行原油预处理——脱盐脱水(BS&W 降低为 0.1%~0.2%、含盐≤5.0mg/L);随着世界各地油田开采程度的不断加深,原油劣质化趋势十分显著,从不同地质结构和 区块开采出来的原油,其比重、粘度、硫和重金属含量都有不同程度的升高;而且油田为了 提高采收率也在不断增加注水和各种助剂的加注量,使原油性质更加复杂多变;此外进口高含酸、高含硫以及机会原油(Opportunity Crude)的炼制,也对各地炼油企业在生产运行、工艺控制上产生了极大影响,首先就是对原油电脱盐装置的冲击,对原油脱后含盐指标的控制也越来越困难;近年来多次出现因盐类水解对设备产生严重腐蚀,以及因之而产生换热器、炉管和其它管线设备的结垢问题,既影响传热过程,又因增加系统阻力而降低了工艺效率,严重时还会因为堵塞管线设备而导致各种非计划停工,大大缩短开工周期,同时还可能会因设备腐蚀而引发各类安全生产事故;此外盐类还会对催化裂化、加氢、延迟焦化、重整等工艺过程产生极大危害,比如造成催化剂中毒等,可以说对炼油生产的负面影响相当致命;所以原油电脱盐装置的运行效果如何,将在相当程度上影响炼油企业的“安、稳、长、满、优”运行。
1.目前炼油企业采取的应对措施不外乎包括:
1)增大电脱盐罐的罐容以增加水力停留时间,或增加电脱盐罐的级数 -目前有三级甚至四级;
2)强化破乳剂种类筛选,增加破乳剂用量;
3)提高加热温度,达 100℃左右;
4)密切关注装置操作运行,减少操作弹性。虽然采取上 述举措在一定程度上解决了企业的燃眉之
急,但却相应带来了运行能耗和运行成本的居高不下。显然搞好电脱盐是保证炼油生产装置正常运
行的先决条件,取新型高效的电脱盐技术以应对原油劣质化趋势,更是具有十分重大的指导意义。

2.技术路线
1)尽管目前原油电脱盐罐内可以采用水平式电极、垂直悬挂平板式电极、鼠笼式电极和复 合式电极等电极结构形式,但采取的供电电源绝大部分为工频/高压交流电源;但由于劣质化原油的导电性较强,随着时间(µs 级)的增加,极间原油将会全部击穿,形成短路,具体表现 在电脱盐设备无法正常给电;
2)另一方面,由于常规工频/高压交流电场对稳定油包水型乳化液 的破乳能力不足,致使原油脱后含盐指标仍然偏高、设备运行不稳定。国内外的大量实践表明,采用高频/高压脉冲交流电场进行油包水型乳化液的破乳时,在极间原油短路击穿形成 之前关闭脉冲输出,待原油绝缘特性恢复后再发下一个脉冲,这样利用高频脉冲的特性既可 在电极间施加较高的电场强度,还能避免电极间形成短路击穿现象。
3)客观而言,虽然就“高频脉冲交流电场优于 高频脉冲直流电场 优于 常规工频交流电场”这一理念在国内已经取得了基本共识,但工程化应用的关键在于大功率工业级高频/高压脉冲交流电源的研制开发;当然对于已经建成投用的原油电脱盐设备而言,受限于电脱盐罐的内部结构等原因,即便更新使用了高频/高压脉冲交流电源,其中仍有可能存在油水乳化层(rag layer),进而影响电脱 盐效率的优化提升。为此,可以研发一种紧凑高效电场破乳设备,将油水乳化层抽出来单独对 其进行破乳处理;然后将破乳处理后的油水混合物与掺混了稀释水的新油水混合物一起进入电脱盐罐内。
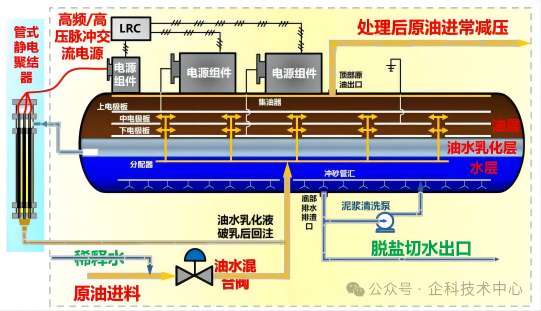
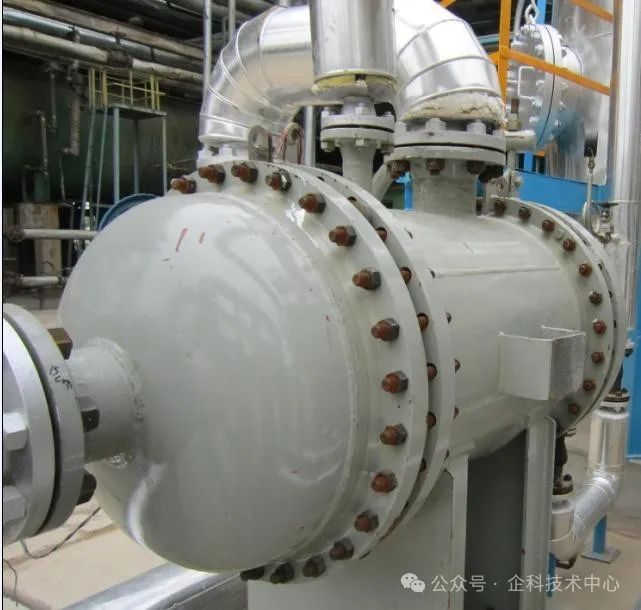
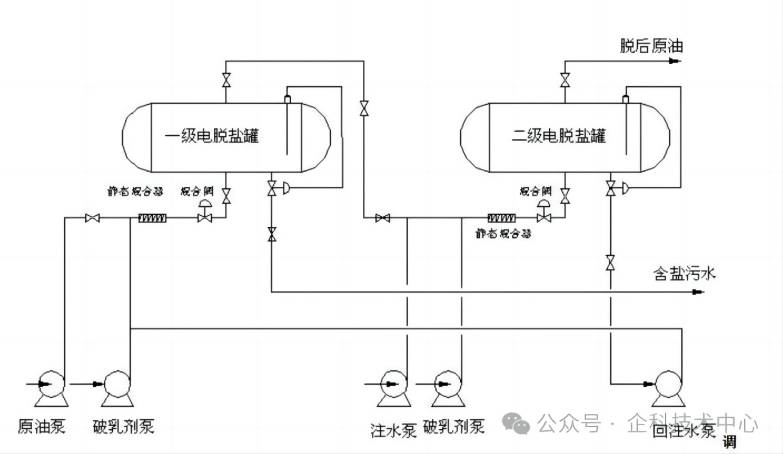
|