随着我国经济建设规模的不断扩大,防水卷材的需求量日益增加,防水卷材制造业也发展迅猛,尤其是改性沥青防水卷材成套设备的技术也日趋完善。目前,《改性沥青防水卷材成套设备适用条件》行业标准即将颁布,这将有力地推动防水卷材设备行业的技术进步和创新。
一条完整的改性沥青防水卷材生产线包括原材料存储系统、改性沥青制成系统、卷材成型系统、导热油加热系统、冷却系统、除尘及烟气处理系统,下面重点介绍改性沥青防水卷材生产线的主要几个技术要点:
1、原材料储存系统 原材料储存系 统主要包括沥青、填充料、覆面矿物粒料等的储存输送装置。
1.1 沥青采用罐装储存、密闭输送方式。沥青储罐的配置应遵循高效、节能、环保及维修便捷等原则。总容积应大于500m³,此外,沥青储罐必须采用导热油升、保温的内置换热器型密闭式节能型储罐 ,以实现高效、节能、环保及减少沥青热老化的目的。
1.2 填充料也采用罐装储存、密闭输送方式可以配置容积为50m³的储罐多台。填充料储存输送装置可 以实现在密闭条件下填充料的自动进仓、自动计量及 自动进入改性沥青搅拌 罐,填充料储存罐宜架空于改性沥青搅拌罐的上方,最大限度地利用高位差原理实现自动“上料”、降低能耗。
1.3 覆面矿物粒料同样采用罐装储存、密闭输送方式,应配置容积为 50m³的覆面矿物粒料储罐2台以上 ,以满足使用2种以上覆面矿物粒料的要求。
1.4 由于改性沥青系统采用高自动化配料方式,上述 原材料储存输送装置相关的泵、阀、料位及温度等设备或参数应具备远程控制能力并配备远程监控措施。
2、改性沥青生产系统
改性沥 青系统包 括有效容积10m³-15m³的立式改性沥青制备罐(配料)2台以上、有效容积10m³-25m³的卧式或立式改性沥青搅拌罐(融胀)2台以上、有效容积6m³-15m³的立式预浸料制备罐2台、流量 10m³以上的胶体磨1台或多台 (间隙可在0~3mm自由调节,根据年产量另决定数量)、过滤器若干、20m³以上的沥青计量罐1台、高黏度沥青泵、相关电动或气动阀门若干。
特别介绍:立式改性沥青制备罐搅拌桨叶的结构与转速对搅拌能力和效率的影响较大,宜采用立式螺旋搅拌和分散盘相结合的高速搅拌系统。同时,高效立式改性沥青制备罐应配备斗式提升机或风送上料等上料系统(满足生产需求,减少体力劳动)和导热油强制自循环系统 以实现各配料罐的工艺温度自控。
由于改性沥青系统采用 自动化配料方式,改性沥青系统相关泵、阀、料位及温度等设备或参数应具备远程控制能力并配有远程监控措施。改性沥青系统的自动化配料方式通常依赖中央控制系统的配备与设计,包括可编程控制器(PLC)自动控制系统和计算机监控系统两部 分。该系统具有运行可靠、自动化程度高、操作简单、参数设定便捷、控制模式灵活、有监控画面等诸多优点。
3、卷材成型系统:一条多功能改性沥青防水卷材生产线的卷材成型系统应包括胎基展卷机、胎基接头机、胎基停留机、胎基烘干机、胎 基对中装置、预浸机组、涂盖机组、厚度测量控制系统、撒砂系统、覆膜装置、压花装置、冷却装置、张力自动调节装置、卷材对中装置、划线烧边装置、成品停留机、缓冲装置、自动卷毡机、卷材称重装置、码垛机、热缩机及中央控制系统等机组或装置。
3.1 胎基展卷机应具备双工位、机动上胎基、调偏、胎基计量和张力调节等功能。
3.2 胎基接头机应有胎基热压接头、胎基制动和导向辊组等装置,热压板宜由导热油供热,温度应有显示并可调节。
3.3 胎基停留机的胎基储量应达到80m以上,确保生产设备50m/min的平均运行速度;活动辊组框架在导向装置引导下,设备正常运行时应始终处于水平状态,并可自动升降。
3.4 胎基烘干机宜由导热油供热,温度有显示并可调节或自控,宜采用穿箱式设计,保证烘干预热胎基效果满足工艺要求,避免“过烘”现象,同时有效减小设备高速运行状态下胎体与烘干机的磨擦阻力,保证胎体的质量。
3.5 胎基对中装置由测量、执行及机械等组件构成,具有手动、自动两种工作模式,调偏精度应达±10mm ;(防止胎基的跑偏、撒裂及断头现象发生,保证生产的高速连续运行)。
3.6 预浸机组的预浸池夹套内通导热油保温,温度有显示并可调节或自控;预浸池内料位和料温采用电磁阀门和传感器实现自控;预浸辊具备升降功能,表面钻有多个孔洞(防止胎基在浸油过程中偏移并增加胎基的浸透性);挤干压辊由多条经过热处理的镜面级辊筒组成,采用气动加压,压力可调节,能很好地将胎基表面沥青挤干;浸油池所有辊筒采用同步传动,变频器调整辊筒转速从属主机变化,避免形成胎基张力。
3.7 涂盖机组的预浸池夹套内通导热油保温,温度有显示并可调节或自控;浸油池中所有辊筒都采用高温热处理,表面镀硬铬。涂油池内料位和料温采用电磁阀门和传感器实现自控;压布辊具备升降功能,可调整胎基在涂盖料中的位置;涂盖机组定厚装置由定厚对辊、托油盘、布油器、厚度调节设备(手动/自动)及刮油刀组成,涂盖托辊内通导热油,具备升降功能(可调整胎基上下油压),托油盘及刮油刀辅助托辊调整胎基表面涂盖料厚度;二条半圆型或圆型定厚对辊与厚度测量控制系统相连,可手动或自动调整间隙以实现生产过程中可任意调整胎基上下涂盖料厚度的目的。
3.8 厚度测量控制系统是通过触屏显示、光电测量、PLC处理、控制伺服电机自动调整定厚对辊的间隙,实现卷材厚度的自动控制。
3.9 撒砂系统与覆面矿物粒料储存输送系统和环保系统相连,包括自动上砂和余砂回收装置、砂仓料位显示装置及撒砂自动跟踪装置,能够自动跟踪、调整撒砂量,并保证覆面矿物粒料的使用过程最大限度地在密闭环境中进行以减少扬尘点和二次粉尘产生。
3.10 覆膜装置由自动跟踪对中装置、可调式橡胶展膜辊、海棉吸水辊组及张力调节装置等组成,具有双工位、机动上膜、自动跟踪和张力调节等功能。覆膜装置采用移动式,可根据环境温度、物料差异及料温差异调整覆膜位置,避免烫膜等现象的发生。
3.11 压花装置设置于卷材下表面,采用气动加压,压力应可调节,以保证压花效果。
3.12 冷却装置采用循环水冷却方式,整个系统由三层式水表面张力悬浮冷水槽、可调式水表面悬浮辅助托架、辊式冷却机及除(吹)水风机等组成,具有冷却效果好、节能、降耗、节省空间和降低工程造价的特点。
3.13 张力自动调节装置可控制和调节生产线各段的张力,使整条生产线在速度调节范围内、合适的张力下同步运行。
3.14 卷材对中装置由测量、执行及机械等组件构成,具有手动、自动两种工作模式,调偏精度达±lOmm,可有效防止卷材的跑偏、撒裂及断头现象发生,保证生产 的高速连续运行。
3.15 划线烧边装置具有施工线的划制、面膜电热烧边、生产信息的喷制等功能,可实现产品防伪及产品信息追溯。
3.16 缓冲装置应采用光电开关,结合送毡装置,配合自动卷毡机正常工作。
3.17 自动卷毡机采用有胎、无胎双功能设计,并有自动/手动两种操作模式,根据不同种类卷材的生产需要进行自由切换。自动卷毡机由PLC控制,自动完成卷毡机卷杠的定位、卷取、卷材计长、切断、胶带捆扎、脱毡等工序。为 了便于卷重计量和防止卷材在卷取过程中跑偏,自动卷毡机还配有卷材称重装置和弹跳装置。自动卷毡机的收卷能力达到5~7卷/min,卷材长度计量误差小于l%。
3.18 码垛机由摆卷装置、移动装置、倾斜机构、夹紧装置、翻转装置、推卷装置、输送小车、托盘供给装置、输送带及PLC电控系统等部分组成,用来配合自动卷毡机工作,把包装好的卷材码放到托盘上,通过输送带进入叉车移走或进入热缩机进行热包装工序。
3.19 热缩机由PLC控制系统自动完成制袋、套袋、热缩等动作,用热缩膜将卷材连同托盘一起进行热缩包装,这样以托盘为包装单位的卷材在存放储运过程中不容易倾倒,大大降低了卷材入库、运输等环节的劳动量。
3.20 中央控制系统包括 PLC 控制系统和计算机监控系统,人机界面显示,可手动/自动调节切换,可一键启停,实现温度、厚度、张力等自动控制,可进行卷材生产的相关信息采集、处理及存储。交流变频调速系统的多 机同步无级 调 速范 围为 0~70 m /rain。中央控制系统具有运行可靠、操作简单、参数设定便捷、有监控画面等诸多优点。
4、导热油系统:导热油系统由导热油炉、导热油循环泵等组成,用来对整条卷材生产线进行供热。导热油炉导热油进出口温差为1O~20 ℃,系统热效率高达 70%以上。一般地区首选燃煤炉,因为生产成本相对较低。基于安全及沥青结焦炭化等因素,导热油系统分两路设计,一路为加热型,主要针对原材料储存系统的沥青储存罐和改性沥青系统的搅拌罐、胶体磨及自洁式过滤器等;另一路为保温型,主要针对伴热管线和卷材成型系统中处于动态工作而又需加热的辊筒等。
5、冷却系统 :冷却系统由冷却塔(制冷机)、循环水池、循环水泵、阀门及循环水管线等组成。冷却系统与卷材成型系统的水表面张力悬浮冷却水槽和辊式冷却机形成闭路 ,采用循环水方式工作,与钢带冷却系统确保冷却效果满足工艺要求,达到卷材卷取包装时卷材温度降到45℃以下且卷材表面无明显水迹。
6、除尘和烟气处理系统:除尘和烟气处理系统包括除尘和烟气处理两个子系统。除尘系统包括除尘器、粉尘收集装置、风机、排放筒及风管等。其中除尘一般采用脉动微震袋式除尘器具有旋风和过滤2级除尘的功能,除尘效率高达99.5%。烟气处理系统包括过滤器、水膜冷凝吸收净化器、活性炭吸附净化器、风机、消声器、风管、排放筒、避雷针等。烟气处理方法有吸收净化法、吸附净化法、过滤法、冷凝法、燃烧法及高压静电捕集法等。其中静电捕集法效果最佳,油烟收集后经过冷凝、吸收 、吸附、过滤等工序处理,沥青烟及废气应符合GB 16297--1996《大气污染综合排放标准》要求。
改性沥青制备系统:
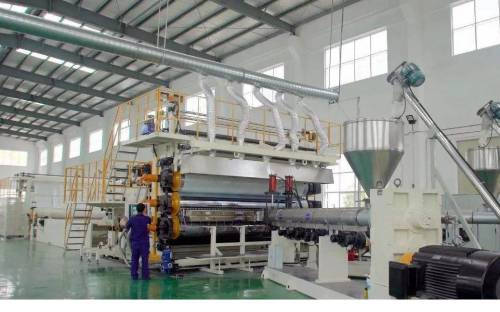
沥青储存系统:
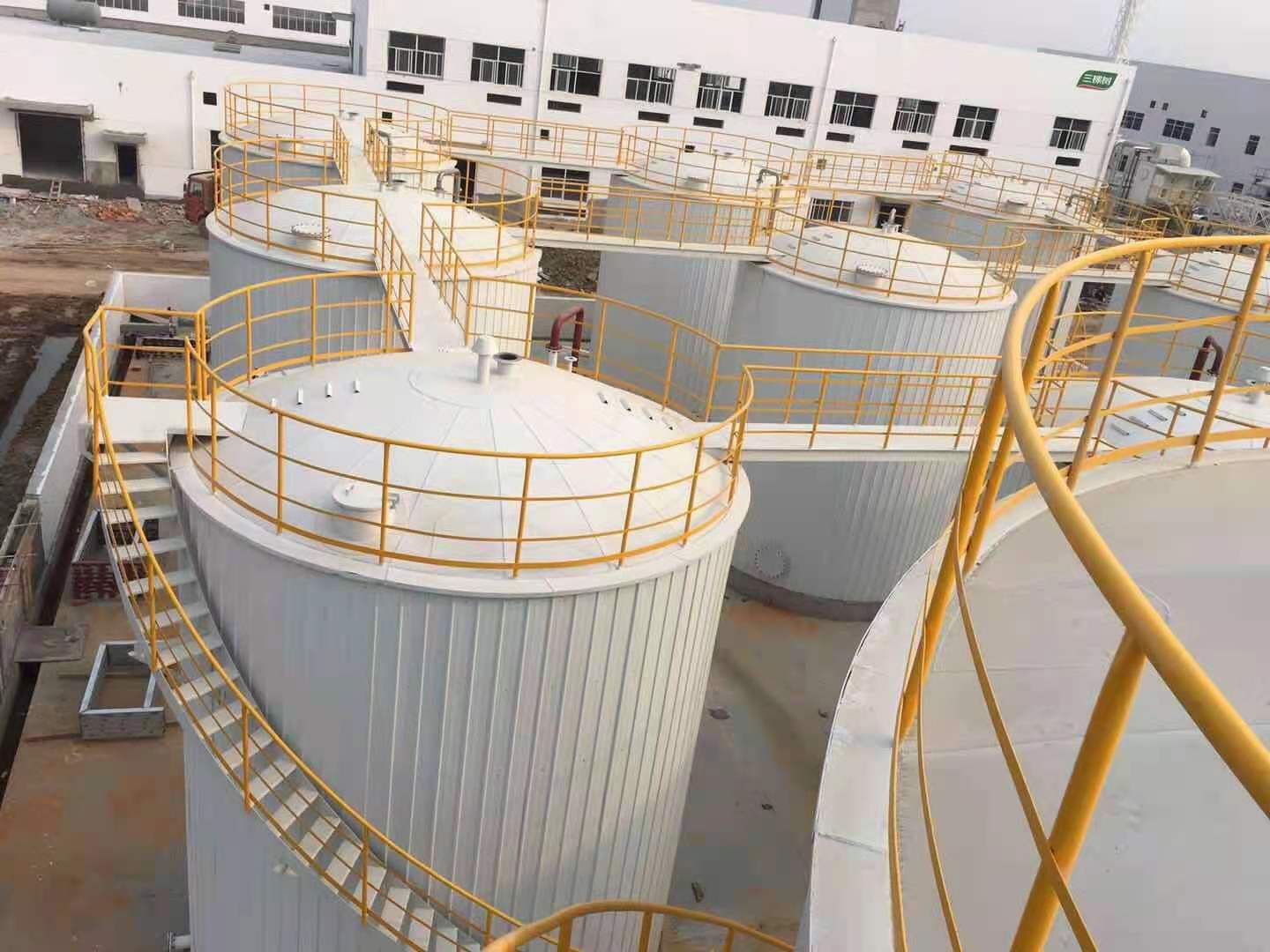
中央控制系统:
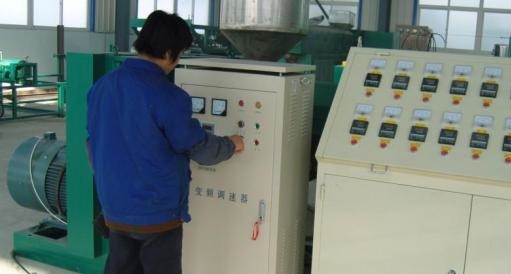
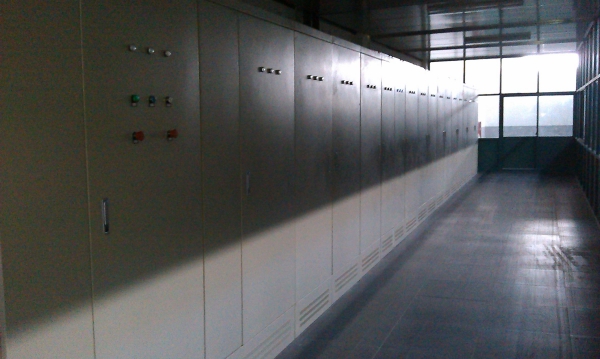
原副料配料系统:
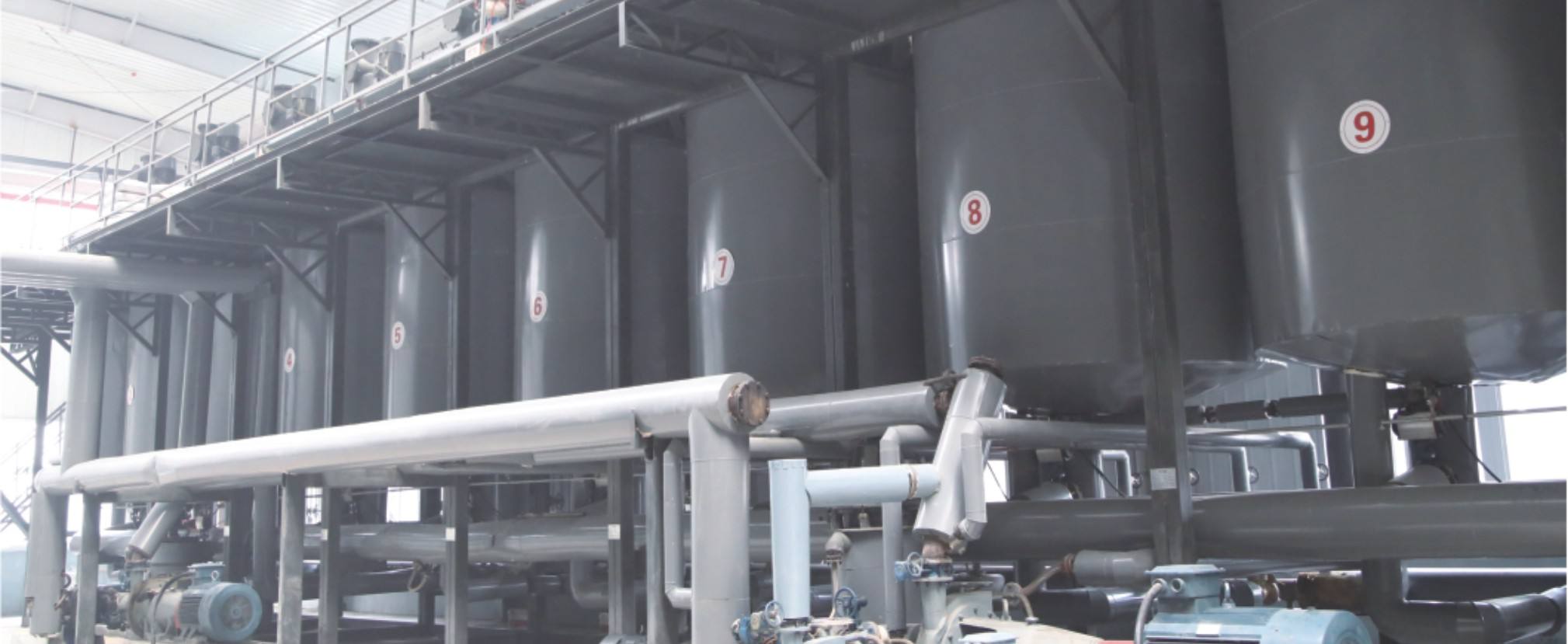
烟气除尘系统:
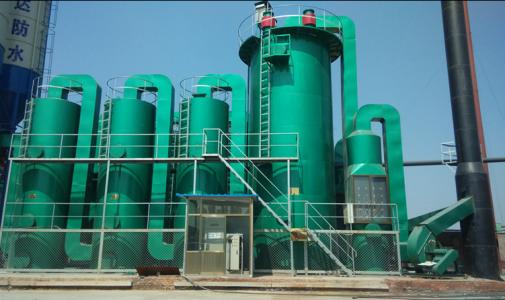
卷材成型系统:
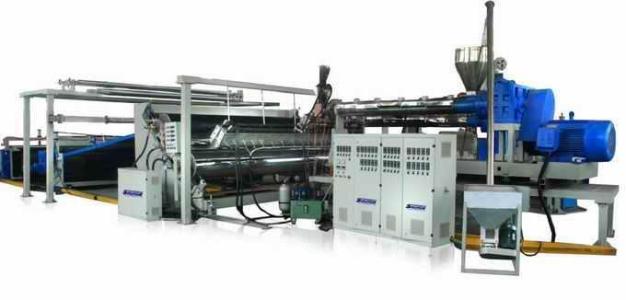
|