
1、 IBC 电池通过改变结构提升效率,有望成为下一代主流技术:与 TOPCon、HJT 等其他晶硅电池的钝化思路不同,IBC 电池主要通过结构的改变来 提高转换效率。IBC 电池(Interdigitated Back Contact,指交叉背接触),是指正负金属电极 呈叉指状方式排列在电池背光面的一种背结背接触的太阳电池结构。IBC 电池正面无金属 栅线,发射极和背场以及对应的正负金属电极呈叉指状集成在电池的背面。这种正面无遮 挡结构完全消除栅线电极造成的遮蔽损耗,能够最大限度地利用入射光,从而有效提高电 池效率和发电量。

2、IBC 电池既可使用 N 型、也可使用 P 型硅片作为衬底,以 N 型硅衬底为例的 IBC 电池 结构如下:
1)前表面为磷掺杂的 n+前场结构 FSF(Front Surface Field),利用场钝化效应降 低表面少子浓度,从而降低表面复合速率,同时还可以降低串联电阻,提升电子传输能力, 可通过磷扩散或离子注入等技术形成;
2)背表面为采用扩散方式形成的叉指状排列的硼掺杂 p+发射极 Emitter 和磷掺杂 n+背场 BSF。p+发射极 Emitter 的作用是与 n 型硅基底形成 p-n 结,有效分流载流子,可以 通过硼扩散或旋涂等方式制备;n+背表面场区能够与 n 型硅形成高低结,增强载流子的分 离能力,可通过磷扩散或离子注入形成;背面 p/n 交替的叉指状结构的形成是 IBC 电池的 技术核心,可通过光刻、掩膜、激光等方法实现。
3)前后表面均采用 SiO2/SiNx 叠层膜作为钝化膜,抑制 IBC 太阳电池背表面的载流 子复合;
4)前表面常镀上减反射层,提高发电效率;
5)金属接触部分全都在背面的正负电极接触区域,也呈叉指状排列。
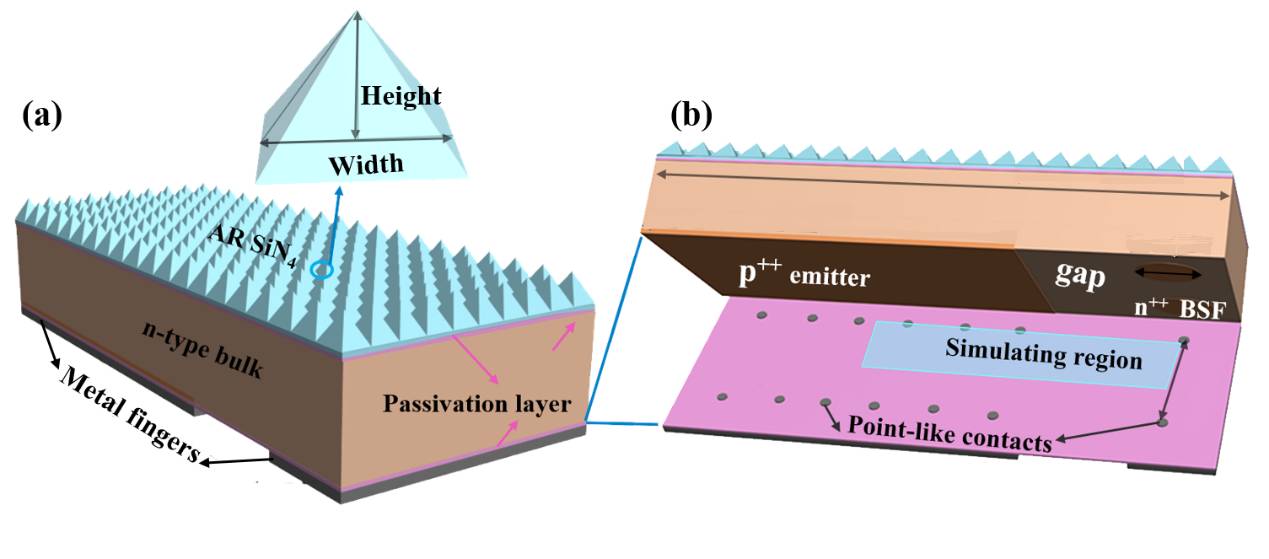
3、受益于正面无栅线的结构设计,IBC 电池转换效率更高、组件封装简单方便且美观。
1)更高的转换效率:有效提升短路电流 Jsc、开路电压 Voc 以及填充因子 FF。
( 1)正面无栅线遮挡,可消除金属电极的遮光电流损失,实现入射光子的最大利用化, 较常规太阳电池短路电流 Jsc 可提高 7%左右;
( 2)由于正面不用考虑栅线遮光、金属接触等因素,可对表面钝化及表面陷光结构进行 最优化的设计,可得到较低的前表面复合速率和表面反射,从而提高开路电压 Voc 和短路 电流 Jsc;
( 3)正负电极均位于电池背面,不必考虑栅线遮挡问题,可以对金属栅线结构做最大程 度优化,例如适当增大栅线宽度、优化栅线形状以降低电池串联电阻,并增强对长波光子 的背反射功能,从而提高电池填充因子 FF 和短路电流 Jsc; 2)组件封装更为方便灵活,避免常规的复杂封装流程。常规电池在组件封装过程 中,需要用涂锡带从电池片的正面焊接到另一块电池的背面。IBC 电池由于其正负电极均 排布在电池背表面,可以避免常规的复杂封装流程,降低自动化生产的难度,从而提高生 产率。该结构特点还可减小电池片的间隔距离,增大组件的封装密度,进而提高光伏组件 单位面积的发电量。 3)外形美观,尤其适用于对双面率要求较低而对美观度有一定要求的分布式场景。 IBC 电池组件封装可以尽可能减小电池间隙,提高单位面积电池密度,并且正面色调更均 匀美观,适用于光伏建筑一体化,具有很好的商业化前景。
4) 制备工艺流程复杂、成本高,进入壁垒显著提升,IBC 电池的生产制造难度大、壁垒高,主要体现在:
(1)对基体材料要求较高,需要较高的少子寿命。因为 IBC电池属于背结电池,为使 光生载流子在到达背面p-n结前尽可能少的或完全不被复合,就需要较高的少子扩散长度。
(2)对前表面的钝化要求较高。如果前表面复合较高,光生载流子在未到达背面 p-n 结区之前已被复合掉,将会大幅降低电池转换效率。
(3)制备工艺流程复杂、生产成本高。需要通过扩散掺杂、钝化镀膜和金属化栅线 等工艺在电池背面制备出叉指状间隔排列的 P 区和 N 区,分别形成金属化接触和栅线,过 程中需要进行多次掩膜和光刻。
5)IBC 电池的衬底硅片要求更高的少子寿命。由于其器件结构的特殊性,IBC 电池前表 面的光生载流子必须要穿过衬底远距离扩散到背表面的 P-N 结才能形成有效的光电流,从 而需要保证前表面的光生载流子在运动到 P-N 结之前不被复合,因此要求衬底材料中少子 的扩散长度比器件厚度大,并且电荷的表面复合速率低。相比于 P 型衬底晶硅电池,N 型 晶硅电池少数载流子寿命更长、对杂质容忍度更高、更易于钝化、电学性能更优异。为提 高转化效率,IBC 太阳电池的硅基体一般选用高质量的 N 型直拉单晶硅片。
6)IBC 电池量产工艺的核心在于,如何低成本地在电池背面制备出呈叉指状间隔排列的 P 区和 N 区,以及在其上面分别形成金属化接触和栅线。相较于其他晶硅电池技术,IBC 电池工艺流程更为复杂,且不同厂商采用制备工艺差异化程度较高。IBC 电池量产工艺的 核心难点,在于如何低成本地在电池背面制备出呈叉指状间隔排列的 P 区和 N 区,以及在 其上面分别形成金属化接触和栅线,重点主要集中在扩散掺杂、钝化镀膜、金属化栅线三 个方面。业内企业曾尝试过掩模光刻、离子注入、炉管扩散、CVD 原位掺杂、激光掺杂等 不同的设备和工艺,来制备 IBC 电池背面 P 区和 N 区。

|