
软包电池组装线是锂电池制造的中后段工序,主要对接叠片或卷绕后的裸电芯,对其进行极耳焊接、贴胶、冲壳、顶侧封装等工序;组装线设计原理主要是依据锂电池的生产工艺流程进行产线的大致布局,具体取决于电芯的尺寸、结构和设计的生产效率等因素。
1 、软包组装线概述 1.1 、组装线设计原理及原则
1)目前针对组装线的形式的选择主要取决于电芯的大小规格,对于长度在390mm以下的电池规格,极耳焊接机、包装机以及包装机后段一般采用凸轮分割器驱动的转盘结构方式,此种结构布局方式结构紧凑,占地面积小,局限于转盘精度,转盘越大,对于电芯的装配精度越差,同时负载的加大也制约了转盘的启停难度和效率。转盘式组装线布局如图1所示。
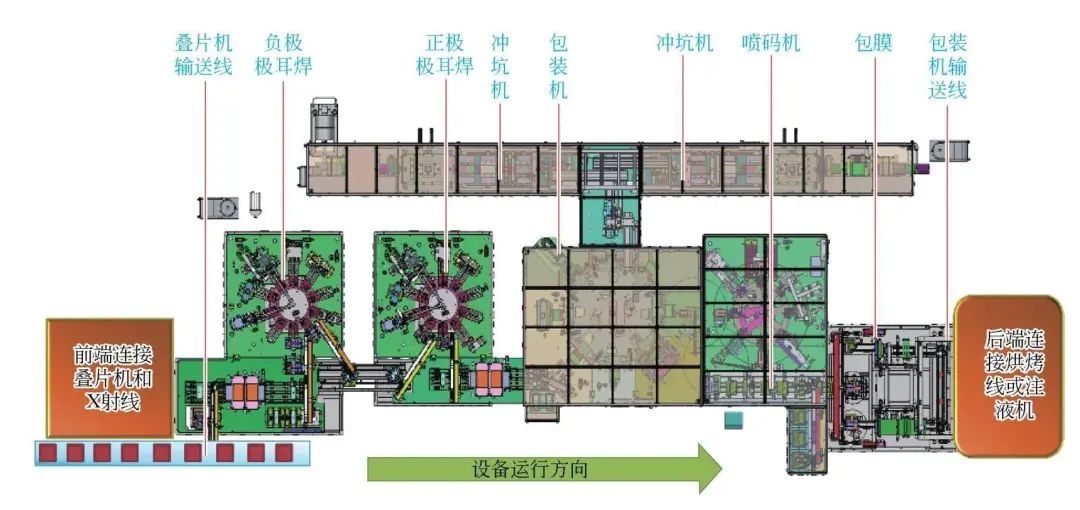
图1 转盘式组装线布局
2)对于长度在390mm以上的电池规格,极耳焊接机、包装机以及包装机后段一般采用直线结构方式,此种布局方式能够满足大电池工位切换的定位精度,工位切换效率高,有更好的生产效率提升空间。缺点在于占地面积比较狭长,工位切换的驱动机构较复杂,成本相对较高。直线式组装线布局如图2所示。
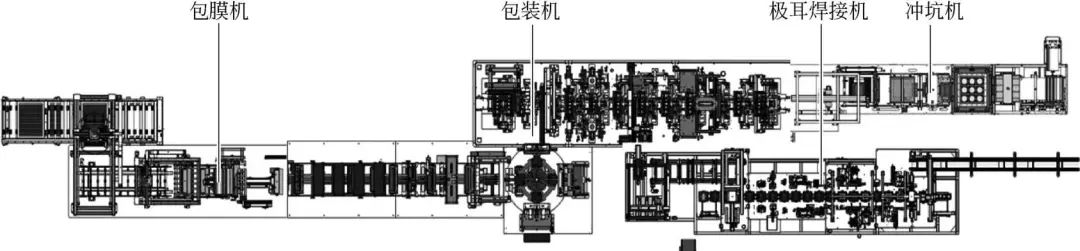
图2 直线式组装线布局
1.2 、组装线节拍分配:在组装线的设计过程中,对于节拍的控制主要取决于各工位生产的瓶颈工位的限制,例如实际产能需求为8PPM,考虑到设备的综合稼动率问题,一般实际按照10PPM进行设计,针对瓶颈工位会采用多工位的方式进行,例如焊接机段的极耳预焊中的保护片上料机构、Tab焊接中的Tab上料机构、包装机中的顶底封封装时间、侧封封装时间等。在对比产能要求后,计算出每个工位所需要的工艺时间,在不满足的情况下就需要进行多工位设计。例如当设备效率要求12PPM时,每个电芯的工艺生产时间为5s,某些客户对封装的时间要求就达到了4~5s,加上电芯工位的切换时间以及封装机构的动作时间,是无法满足生产效率要求的,因而此工位需要设计双工位才能满足生产效率要求,其他工位在节拍分配上同理。在设计时,在理论上需要进行节拍的分配分析,图3为极耳焊接机段的时序图。
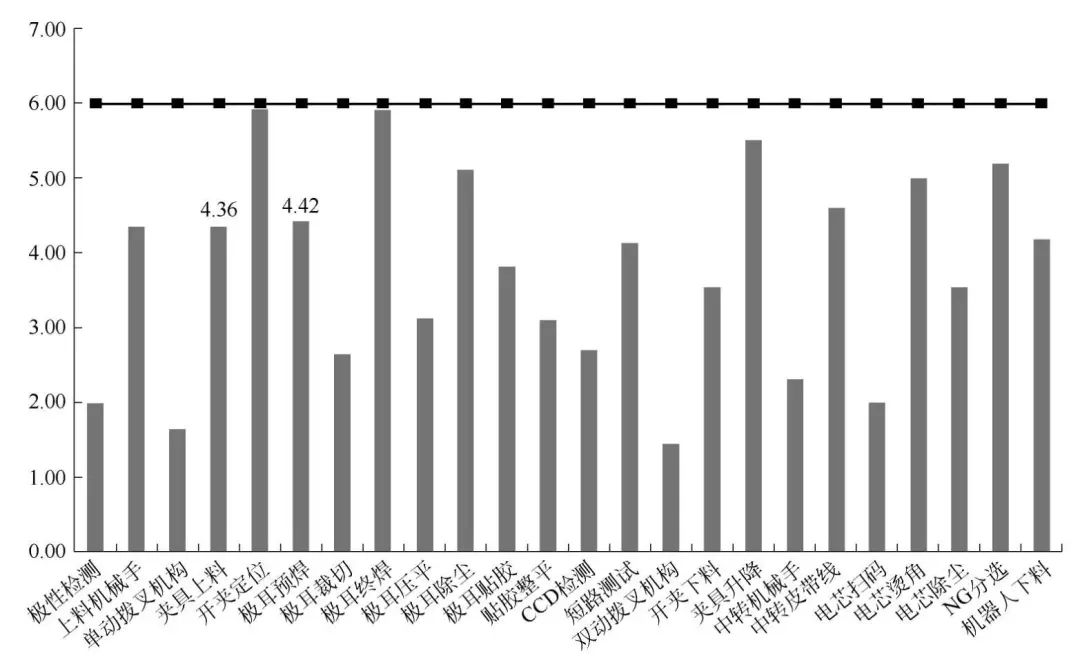
图3 极耳焊接机段的时序图
1.3 物流方式:电池在组装时,必然需通过物流进行各工位上的流转和切换。因而需要对不同状态下的电芯进行合理的物流方式的选择。
①对于叠片机出料的裸电芯而言,为了保证电芯的输送效率以及保护电芯的安全性,常规以倍速链+电芯夹具的方式进行,倍速链具备输送效率高、适合长距离输送、负载大、维护简单等优点,且倍速链型材对于设置挡停以及其他辅助结构安装调节具有很大的灵活性。缺点在于倍速链容易摩擦产生粉尘,有个别厂家为规避粉尘对电芯的影响,选用磁悬浮输送线进行裸电芯的输送,但价格昂贵。
②电芯从叠片机输送过来进入焊接机,焊接机上的每个工位对电芯的定位精度有较高要求,电芯被装入焊接夹具内,采用步进式输送方式,为保证精度要求,驱动采用伺服电机+拨叉的循环结构。
③在电芯从焊接机下料后,一般采用伺服电机+同步带的输送方式,这样可保证电芯输送的等间距性,方便机械手的下料和上料抓取位置的准确性,同理,在包装机之后也采取同样的方式进行,经济且高效。
1.4、 电芯定位方式及原则
1)在电芯组装线上,电池厂家在工艺上对电芯有一定的尺寸精度要求,因而在电池进组装线之前需要对电芯进行定位,以同一个基准进行电芯的定位,后面各工位的调整也以此为基准,以确保电芯组装的一致性。
2)电芯本体的形状为矩形,因而在定位形式上通常采用两边为定位基准,另外两边以推的方式进行电芯的定位。也可以采用电芯本体中心定位方式,前后左右同时进行推电芯本体,在定位方式的选择上一般取决于电芯的工艺尺寸要求,以及在结构设计上的便利性,只要保证基准一致即可。
1.5、 粉尘控制:在电池生产过程中,最致命的危害莫过于金属粉尘进入电芯本体内,引发一系列的问题,如电池的短路起火等。为了避免这种情况的发生,需要对组装线段的粉尘产生源进行严格控制和尽可能清除,控制粉尘,首先得找出粉尘的产生源,然后进行针对性措施。
①叠片机输送线(倍速链)。由于在输送过程中,倍速链条会与倍速链型材摩擦产生较多粉尘,针对这类粉尘需要对倍速链线体加装防尘板,防止粉尘掉落到电芯上,同时电芯夹具尽可能采用上下包夹的方式进行输送,对于回流线体上的空夹具进行定点除尘,除尘方式采用吹+吸的方式进行,由于线体比较长,需要增大人工清洁频率,以防止粉尘堆积等。
②组装线。电池在组装线中进行流转时,有一些工位本身就能产生粉尘,比如极耳的预焊、裁切、Tab焊接、焊印压平等工位,只要存在裁切或者焊接的工位都会设置专门的除尘机构进行不间断的吸尘处理,图4为除尘工位图。
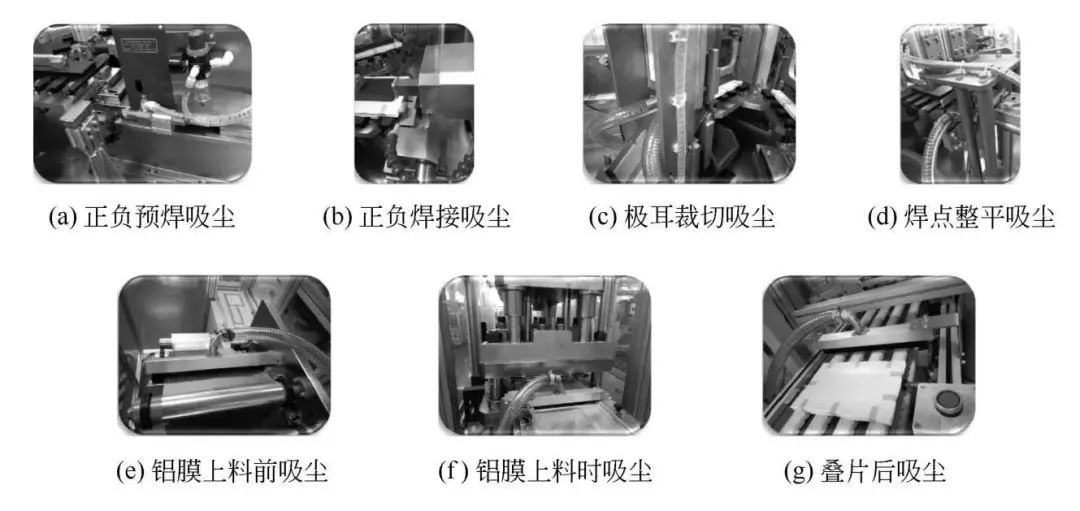
图4 除尘工位图
1.6 、质量监控 :为了电池生产质量的稳定性和一致性,在电池生产的各个环节都会有相应的检测传感器来进行质量控制。对于组装线来说,具体体现如下: ①通过颜色传感器对电芯来料的极性进行检测,主要是为了防止人工干预后的电池放反。 ②电芯的扫码,保证电芯信息及时上传到MES系统中,便于电池生产的信息跟踪。 ③电芯的X射线检测,用来检测电芯的对齐度,防止错位严重的电池往后接着生产。 ④Tab片的极性检测以及正反检测,避免焊接错误。 ⑤Tab焊接后的贴胶检测,避免后面封装时焊印直接接触铝塑膜。 ⑥Tab焊接后的CCD尺寸检测,保证电芯生产的尺寸一致性。 ⑦焊接后电芯的Hi-pot测试,确保焊接后的电芯两极无导通。 ⑧铝塑膜纠偏控制,保证铝塑膜的冲坑良品率。 ⑨封装后电池的CCD尺寸检测,保证电池外观尺寸的一致性。 ⑩封装后电池的Hi-pot测试,确保封装后的电芯两极无导通。 ⑪封装后电池的绝缘测试,确保封装后的电芯两极与铝塑膜之间无导通。 ⑫封装后电池的封印厚度检测,确保封装后电池封印的一致性。
通过上述的一系列控制方式和点位,可以对电池在整个组装线上的质量进行有效控制。

|