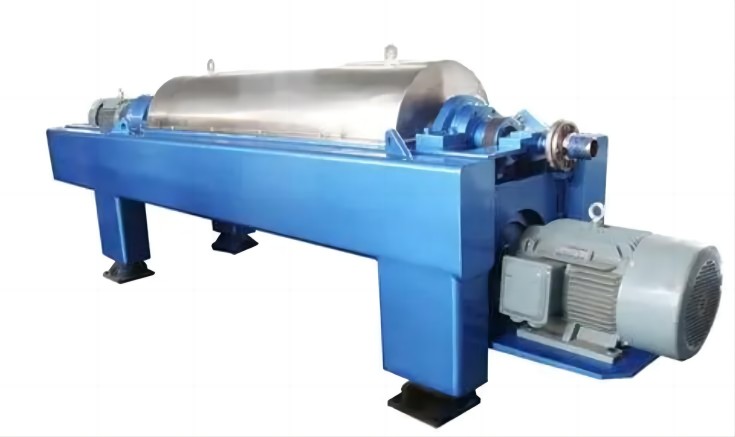
上文开始对污泥脱水机的卧式离心机的工艺管理细节进行讨论,现在将继续讨论卧式离心机的管理内容;在卧式离心机的脱泥过程中,高速旋转的转鼓在转鼓内壁上形成的液环层和固环层,依靠两者的速度差完成的泥水分离的过程。
1、在实际的运行操作中,当进泥量一定时,液环层越厚,污泥在液环层内进行分离的时间越长,会有更多的污泥被分离出来;
2、另一方面,液环层变厚,会降低某些受扰动的小颗粒随分离液流失的可能性。
综合以上两方面的作用,液环层增厚一般会提高脱水的固体回收率。但液环层增厚,相应会使干燥区缩短,使脱离液环层的污泥没有充足的时间被“甩干”,因此泥饼含水率就会升高。
3、在实际运行中,运行人员控制液环层厚度时应在高固体回收率与泥饼水率之间权衡,经过离心澄清的形成的液相的液环层流到转筒圆锥端并通过转筒盖中的开孔排出机外。卧式离心机设置了便于调节并具有很高精度的堰板(溢流堰板),使得转筒内液环层深度的调节变得很精确。通过溢流堰板的溢流排入集液管并在重力作用下排出机外。
4、现在的污水厂采用卧螺机只是完成污泥脱水过程,达到80%的含水率就行,所以固体回收率则越高越好,因此液环层厚度应尽可能调大一些。通过调整溢流板,控制液环层的厚度,来达到运行的预期目标。

5、离心脱水一般采用高效的人工合成高分子絮凝剂,而不采用无机盐类混凝剂。其原因是添加无机类混凝剂的桥接作用会使得污泥体积膨胀,而离心机为封闭式强制脱水,对进泥量有较严格的要求,因此如果采用无机盐类混凝剂会使离心机的脱水能力大大降低。特别是现阶段除磷药剂的大量使用,化学污泥中残留的混凝剂可能会影响卧螺机的运行效果。
6、在允许的范围内,当进泥的泥质及絮凝剂的化学调质效果一定时,进泥量越大,固体回收率和泥饼含固量越低;反之,进泥量降低,则固体回收率和泥饼含固量将提高。另外,每台卧螺机都有一个极限最大入流固体量。如果当由于进泥含固量升高等原因导致入流固体量超过极限值,将由于扭矩过大,使离心机超载而停车。
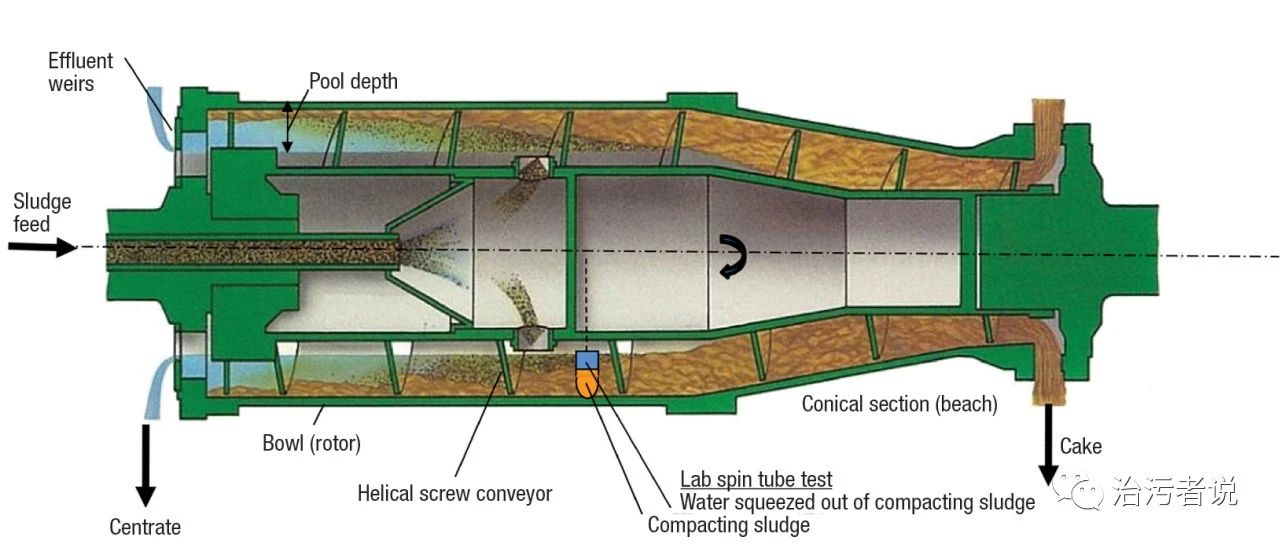
7、在实际运行中,运行人员选择适当的污泥流量的方法:首先将污泥流量调到较小值,然后启动卧螺机并工作一段时间,至泥饼出料的速度一定。观察泥饼量及出料速度是否合适,如果不合适,则相应改变进泥流量,直到泥饼出料量及出料速度合适,此时的进泥流量通常为适当的值,有时候该值可能很小。
8、例如一台10m3/h处理量的卧螺机,由于进料悬浮液的含固量很高,实际合适的进料流量可能只有2m3/h左右。
泥泥饼的含水率、污泥离心清液的控制除去在工艺流程中对产生污泥的各个环节进行工艺调控以外,对于脱水机设备本身主要通过离心机的转速、
差转速、液环层等可调节因素来对设备的运行效果进行调整,从而得到需要的泥饼含水率。
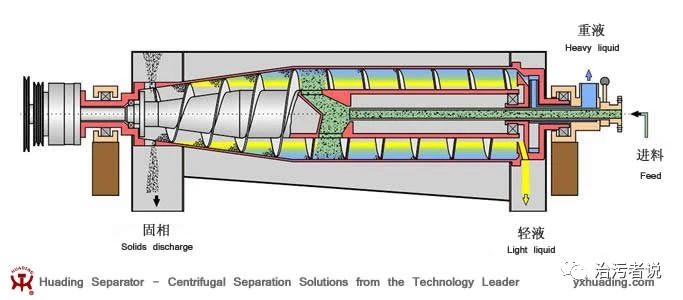
1)转鼓转速转鼓转速的调节通常通过变频电机来实现。转速越大,离心力越大,有助于提高泥饼含固率。但转速过大会使机械剪切力增加,也会使污泥絮凝体被破坏,反而降低脱水效果。同时较高转速对材料的要求高,对机器的磨损增大,动力消耗、振动及噪声水平也会相应增加,一般运行人员要认真学习阅读脱水机的使用说明,严格将设备转速控制在设备的最佳运行速度内,不能追求过高的转速导致设备损坏。
2)差速度直接影响排渣能力、泥饼干度和滤液质量。提高差速度,有利于提高排渣能力,但沉渣脱水时间会缩短,脱水后泥饼含水率大,时过大差速度会使螺旋对澄清区液池的扰动加大,滤液质量相对差一些。降低差速度,会加大沉渣厚度,沉渣脱水时间增长,脱水后泥饼含水率降低,同时螺旋对澄清区污泥沉积颗粒的扰动小,滤液质量也相对好些,但会增大螺旋推料的负荷,应防止排泥量减小造成离心机内沉积污泥不能及时排出而引起的堵料现象,导致滤液大量带泥,这时就必须减小进料量或提高差速度。因此应根据污泥性质、处理量大小、处理要求及离心机结构参数来确定差速度大小。一般认为泥饼在干燥区的脱水时间应控制在4~6S秒之间,时间再长效果也不会明显变化。
3)环层厚度是工艺优化的一个重要参数,直接影响离心机的有效沉降容积和干燥区长度,进而影响离心机的处理效果。一般在停机状态下通过手动调节液位挡板的高低来实现,调整时必须确保各个液位挡板的高低一致,否则会导致离心机运行时剧烈振动,也有部分国外厂商的产品可以实现液环层厚度的自动调节。
4)液环层厚度增加,会使沉降面积增大,物料在机内停留时间也会相应增加,滤液质量提高,但同时机内的干燥区长度缩短,导致泥饼干度降低。相反,调低液环层厚度可获得较高的泥饼含固率,但要以牺牲滤液质量为代价。因此应合理地调节液位挡板的高低使泥饼干度与滤液质量达到最佳组合。
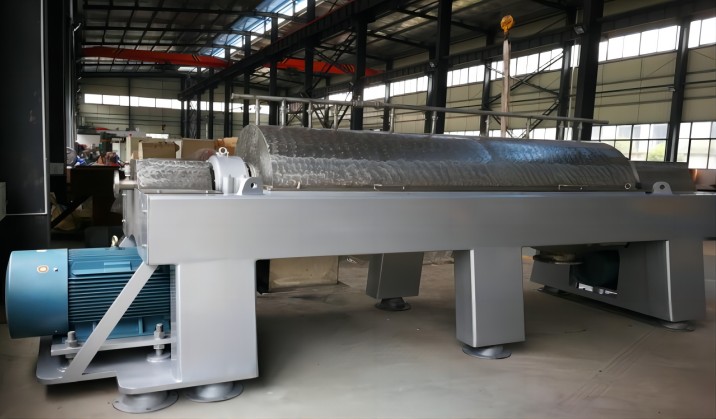
|