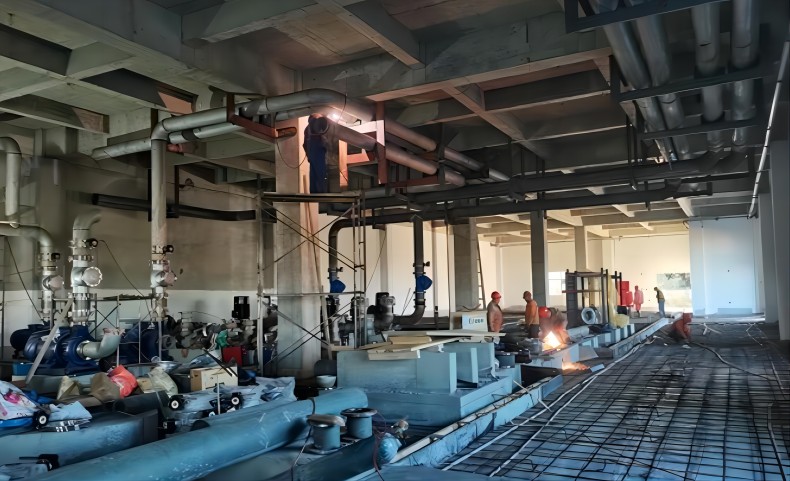
2. 碳化硅工艺难度大,衬底制备是最核心环节:衬底制备是最核心环节,难度集中在晶体生长和衬底切割。从原材料到 碳化硅器件需要经历原料合成、晶体生长、晶体加工、晶片加工、外延生长、晶圆制造和封测等工艺流程。衬底制备是最核心环节,技术壁垒 高,难点主要在于晶体生长和切割;外延生长关键环节,影响最终器件 性能。SiC 晶圆制造与硅晶圆类似,通过涂胶、显影、光刻、减薄、退火 等前道工艺加工成晶圆,经后段工艺制成芯片,用于制造各类器件及模 组,通过验证后即可用于汽车、光伏等应用领域。
2.1. 晶体生长:速度慢可控性差,是衬底制备主要技术难点:SiC衬底是芯片底层材料,主要技术难点在于晶体生长。衬底是沿晶体 特定结晶方向切割、研磨、抛光,得到的具有特定晶面和适当电学、光 学及机械特性,用于生长外延层的洁净单晶圆薄片。SiC 单晶衬底是半 导体芯片的支撑材料、导电材料和外延生长基片,主要起到物理支撑、 导电等作用。生产碳化硅单晶衬底的关键步骤是晶体生长,也是碳化硅 半导体材料应用的主要技术难点,是产业链中技术密集型和资金密集型 的环节。SiC 单晶生长方法主要有:物理气相传输法(PVT)、高温化学 气相沉积法(HTCVD)和以顶部籽晶溶液生长法(TSSG)为主流的高温溶 液生长法(HTSG)。
1)PVT 法技术成熟、原理简单、成本较低,是应用最广、商业化程度最高 的衬底制备方案。目前, Wolfspeed、Ⅱ-Ⅵ、SiCrystal(Rohm 子公司) 和天岳先进、天科合达等企业均采用 PVT 法生产 SiC 衬底。主要技术难 点在于:
(1)粉体纯度要求高,主要采用改进自蔓延高温合成法。PVT 法通过SiC 粉料的高温分解与结晶来实现单晶生长,粉体杂质含量低于 0.001%。改 进自蔓延高温合成法是目前工艺最成熟、使用最广的粉体制备方法。
(2) 长晶速度慢,封闭生长可控性有限。硅棒一般 2-3 天可拉出约 2m 长 的 8 英寸硅棒,PVT 法下 SiC 7 天才能生长约 2cm 晶体。SiC 良品参数 要求高,核心参数包括微管密度、位错密度、电阻率、翘曲度、表面粗 糙度等,但生长过程在密闭高温腔体进行,工艺可控性有限。
(3) 晶型多样,易产生多型夹杂缺陷。SiC 单晶有 200 多种晶型,一般仅 需一种晶型(如 4H),因此需要精准控制硅碳比、温度梯度、外部杂质 引入以及气流气压等,量产性能稳定的高品质 SiC 晶片技术难度大。
(4) 扩径难度很大,扩径可提高晶圆利用率降低制造成本,PVT 法下 SiC 扩径难度极大,随着晶体尺寸的扩大,生长难度工艺呈几何级增长。
2)HTCVD 法可控性较好,国内已有相关设备下线。HTCVD 法利用硅源 和碳源气体的高温化学反应实现单晶生长,优点在于:
(1)可通过连续供 源实现晶体稳定持续生长;
(2)省去粉料合成过程,可以制成一体化设备。
(3) 缺点在于 HTCVD 法和 PVT 一样需要高温条件,需要用到多种气体,成 本较高,而且生长过程存在多种附带。
(4)目前,意法半导体、丰田集团和 电装集团等已实现 HTCVD 规模化生产碳化硅晶体,国内江苏超芯星已 研制出 HTCVD 碳化硅单晶生长设备。 TSSG法有望成为制备大尺寸、高结晶质量且成本更低的衬底制备方法。 高温溶液生长法通过 Si 和 C 元素在高温溶液中的溶解、再析过程实现 SiC 单晶生长,其中 TSSG 法由于具有生长温度低、易扩径、晶体质量 有高、易实现 p 型掺杂等优点,为业界所看好。目前,液相碳化硅晶体 生长的研发主要集中在日本、韩国和中国,主要包括日本住友金属、丰 田汽车、三菱电机、东京大学和名古屋大学等,韩国陶瓷工程技术研究 所、东义大学、延世大学等,以及中国中科院物理所、北京晶格领域和 常州臻晶半导体等。
2.2. 晶体加工:切割是技术难点,研磨抛光提高表面质量:由于 SiC 材料硬度高、脆性大、化学性质稳定,加工难度大。碳化硅晶 锭需要借助 X 射线单晶定向仪定向再磨平、滚磨成标准尺寸的碳化硅晶棒。
1)晶棒要制成 SiC 单晶片,还需要以下几个阶段:切割—粗研—细研 —抛光,简称切抛磨,切抛磨工艺环节难度相对较小,各家差距不大, 工艺路线基本一样。SiC 切抛磨工艺的挑战在于:
(1)硬度大:SiC 单晶 材料莫氏硬度分布在 9.2-9.6 之间,仅比金刚石硬度低 0.5 左右,因此切割速度慢,切一片要 2 天,且易破碎,一般要损失掉一半左右。
(2)化 学稳定性高:几乎不与任何强酸或强碱发生反应,室温下能抵抗任何已 知的酸性腐蚀剂;
(3)加工机理及缺陷扩散的研究欠缺。
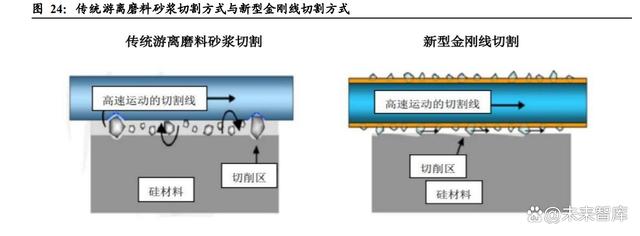
2) 切割是首道加工工序,固结磨料金刚线切割应用最广:切割是衬底加工中首要关键的工序,成本占总加工成本50%以上。切割 是碳化硅晶棒第一道加工工序,决定了后续研磨、抛光的加工水平,切 片后需要使用全自动测试设备进行翘曲度(Warp)、弯曲度(Bow)、厚 度变化(TTV)等面型检测。
3)切割工艺的演进主要经历了:(1)传统的内 圆锯切割和金刚石带锯。(2)目前较多提及且较有效的电火花切割、线锯 切割(包括游离磨砂线锯切割和金刚石线锯切割)、激光切割、冷分离工 艺等。(3)水导激光切割等具备未来应用前景的新型工艺。
4) 传统锯切工具缺陷多效率低,不适用于碳化硅晶体切割。内圆切割机使 用环形不锈钢内圆刀片,内刃口镀金刚砂颗粒,周边采用机械方式张紧, 切缝宽、翘曲度大、表面质量差、精度低、噪声大而且仅可切割直线表 面。
5)金刚石带锯需要频繁停止和换向,切削速度非常低,一般不超过 2 m/s,机械磨损大,维修费用高,而且受限于锯条宽度,切割曲率半径不 能太小,只能进行单片切割,不能进行多片切割。传统锯切方式材料损 耗大、加工效率低,不适用于工业化碳化硅晶片切割。
6)固结磨料金刚线切割成为主导,但存在损耗率及效率问题。20世纪90 年代中期,游离磨料砂浆切割取代传统锯切工艺,并随着光伏行业兴起 而爆发,逐渐广泛应用于半导体行业。游离磨料砂浆切割利用线锯快速 运动,将砂浆中的磨料颗粒带入锯缝达到“滚动-压痕”机制以去除材料, 实现了多片同时切割,产率高且耗损率低,已广泛用于单晶和多晶硅切 割,缺点是存在切割速度低、精度差、晶片厚度不均匀、砂浆回收难造 成环境污染等问题。固结磨料金刚线切割通过电镀、树脂粘结、钎焊或 机械镶嵌等方式将金刚石磨粒固结在切割线上,借助金刚线高速运动完 成切割,根据金刚线运动方式不同可分为单向式、往复式和环形式,往 复式切割单位长度有效利用度高、速度快,成为目前 SiC 晶体切割主流工艺。
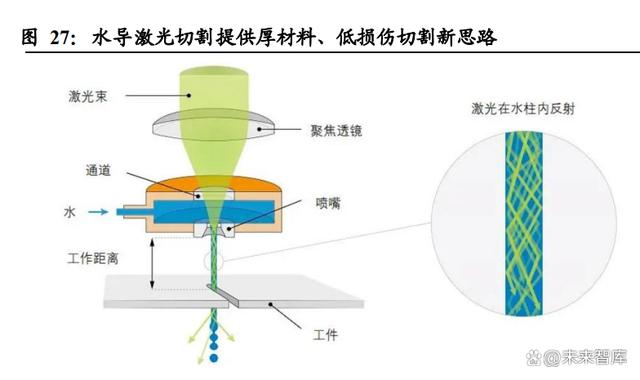
7)激光切割逐渐兴起,工艺精细效率更高。目前针对 SiC 材料较为有效的 切片方法除了固结磨料金刚线切割,还有电火花切割、激光切割、冷分 离工艺等。电火花切割主要利用脉冲放电的电蚀作用进行切割,但存在 切缝宽、表面烧伤层厚度大等缺点。激光切割是通过激光处理,在晶体内部形成改性层从碳化硅晶体上剥离出晶片,属于非接触无材料损失加 工,并且具有切割断面质量好、切割效率高、清洁安全无污染等优点。 冷分离切割利用激光在晶锭内部形成角质层点平面,在上表面涂覆特制 分离材料并冷冻,遇冷收缩分离晶圆薄片。
8)为提高切片效率,国外企业开始采取更为先进的激光切割技术。2016年 日本 DISCO 开发了新型激光切片技术 KABRA,通过激光连续照射钢 锭,在指定深度形成分离层分离晶片,可用于各类 SiC 铸锭。优势主要 有:
(1)显著提高切割效率,现有工艺 3.1h 才能切割 1 片 6 英寸 SiC 晶 圆,而 KABRA 技术仅需 10 分钟。
(2)省去研磨过程,因为分离后的晶 圆波动可控。
(3)晶圆生产数量相比现有工艺增加了 1.4 倍。2018 年 11 月,英飞凌以 1.24 亿欧元收购晶圆切割初创企业 Siltectra GmbH,后者 开发了冷裂工艺(Cold Split),通过专利激光技术定义分裂范围、涂覆专 用聚合物材料、控制系统冷却诱导应力精准分裂材料和研磨清洗等实现 晶圆切割。冷裂可将 SiC 产能提升 3 倍以上,每片晶圆损失低至 80μm, 而且晶圆减薄仅需几分钟,对晶锭采用冷裂工艺可降低损失比例 50%。
9)水导激光切割等新型工艺提供厚材料、低损伤切割新思路。水导激光加 工(Laser MicroJet,简称 LMJ)利用导水激光器将激光聚焦并导入微型 水柱中,水柱可以在稳定范围内加工,而且长有效工作距离特别适合于 厚材料切割。水导激光切割可以利用水流带走热量和切屑,规避传统激 光切割两侧热损伤问题。理论上水导激光切割具备应用前景,但现阶段 由于技术难度较大,相关设备成熟度不高等,尚不适用于碳化硅晶片制造。
10)设备端以金刚线切割机为主,激光切割逐渐发展,国产品牌发展迅速。 2016 年以前,光伏切割设备领域占主导地位是以瑞士 Meyer Burger 公 司、HCT 公司,日本高鸟、小松 NTC 等为代表的国际厂商;激光切割 方面则由日本半导体设备巨头 DISCO 主导。近年来国产品牌发展迅速, 国产光伏切割设备已经占据市场主导地位。目前国内碳化硅切割设备主 流为金刚线切割设备,主要集中于高测股份、上机数控、连城数控、宇 晶股份等国内企业;激光切割设备目前试产份额较小,主要集中于德龙 激光、大族激光等国内企业。
11)研磨抛光清洗工序,保障晶片表面质量和精度要求:切割片存在损伤层,需要通过磨削、研磨、抛光和清洗环节提高表面质 量和精度。切割片通常采用砂轮磨削和研磨相结合来去除刀痕及表面损 伤层,超声振动辅助磨削和在线电解修整辅助磨削可以提高磨削质量。 研磨分为粗磨和精磨,粗磨使用粒径较大磨粒,可有效去除刀痕和变质 层;精磨使用粒径较小磨粒,可改善表面光洁度和平整度。抛光进一步 消除表面划痕、降低粗糙度和消除加工应力,化学机械抛光工艺(CMP) 是实现 SiC 单晶片全局平坦化最有效的方法,是实现加工表面超光滑、 无缺陷损伤的关键工艺。抛光后需借助 X 射线衍射仪、原子力显微镜、表面平整度检测仪、表面缺陷综合测试仪等设备检测各项参数指标来判 定晶片等级。随后需在百级超净间内,使用清洗药剂和纯水清洗,去除 微尘、金属离子、残留抛光液等沾污物,再借助超高纯氮气和甩干机吹 干、甩干,并封装在洁净片盒内。
12)外延生长:极大影响器件性能,向低缺陷高耐压发展。外延层是晶圆上生长的微米级单晶层,极大影响器件性能。SiC器件制 作工艺不同于传统硅基器件,不能直接制作在 SiC 单晶材料上,必须基 于单晶衬底额外生长特定的一层微米级新单晶,再在外延层上制造器件。 外延层主要作用在于消除 SiC 晶体生长和加工过程产生的表面或亚表面 缺陷,使晶格排列整齐,大大改善衬底表面质量。SiC 衬底上可异质生 长 GaN 外延层,主要用于制造中低压高频功率器件(小于 650V)、大功 率微波射频器件以及光电器件;也可同质生长 SiC 外延层,主要用于制 造功率器件。由于宽禁带半导体器件几乎都做在外延层上,所以外延层 质量对器件性能有很大影响。
(1)化学气相沉积法(CVD)工艺可控性强,是外延生长的主要方法。外延 生长方法包括:蒸发生长法、液相外延生长(LPE)、分子束外延生长 (MBE)、化学气相沉积(CVD)。 CVD 是同质外延批量生产的主要方 法,优势在于可以很好地控制 C/Si 原子比率、反应室温度与压力,精准 控制外延层厚度、背景掺杂浓度和掺杂类型。早期 CVD 法采用无偏角 衬底方式生产外延,但存在严重的多型夹杂缺陷;台阶控制外延法通过 特定偏角斜切衬底,可实现低温条件下(1200℃)复制衬底的堆垛次序 消除多型体共存缺陷。为了提升外延生长速度,TSG 法应运而生,主要采用采用三氯氢硅(TCS)作为硅源,比起常规的硅源它的外延速率会提 高 10 倍以上。
(2)随着功率器件制造要求和耐压等级提高,SiC外延向低缺陷、高厚度方 向发展。随着器件耐压等级提升,外延厚度随之增加。在 600V 低压领 域,所需外延层厚度约 6µm;在 1200~1700V 中压领域,所需外延层厚 度约 10-15µm;在 10000V 以上高压领域,所需外延层厚度达到 100µm 以上。目前中低压外延技术较成熟,可以满足中低压的 SBD、JSB、 MOSFET 等器件需求;而高压领域还有不少难关需要攻克,主要体现为 缺陷控制方面。目前, Wolfspeed、Ⅱ-Ⅵ、ROHM、英飞凌等国外厂商 多为衬底+外延垂直整合模式,国内衬底与外延分属两个不同环节,代表 厂商为瀚天天成、东莞天域。外延设备则基本由海外企业垄断,意大利 LPE、德国 Aixtron、日本 Nuflare 市场占比高达 87%,国内设备厂家如 中电科 55 所、三安集成、苏州希科等产品逐渐得到认可。
2.3. 晶圆制造:工艺与硅基类似,需要特定工艺和设备/工艺流程与硅基器件大体类似,材料不同要求特定工艺与设备。碳化硅 器件也包括器件设计、晶圆制造和封测等环节,晶圆制造主要包括涂胶、 显影、光刻、清洗、减薄、退火、掺杂、刻蚀、氧化、磨削、切割等前 道工艺约三百多道工序。由于材料特性的不同,部分工序需要特定设备 和特定工艺,与硅制程设备无法完全通用。主要差异在于:
1)光刻对准:双面抛光的 SiC 晶圆是透明的,光刻工艺难以适应,各设 备传送、取片难以定位,CD-SEM 和计量测量变得, 复杂。
2)蚀刻工艺: SiC 在化学溶液中呈惰性,只有干法刻蚀可行,需重新 开发掩膜材料、混合气体、侧壁斜率、蚀刻速率、侧壁粗糙度等。
3)掺杂工艺:SiC 扩散温度远高于 Si,高温高能离子注入成为唯一的 SiC 制造掺杂方法,但这会破坏材料的晶格结构,所以还需要在 1600℃的条 件下使用高温退火工艺恢复结构,是否具备高温离子注入机是衡量碳化 硅生产线的重要标准之一。
4)MOSFET 栅极氧化:SiC-MOSFET 器件的栅氧质量直接影响沟道的 迁移率和栅极可靠性,导致阈值电压不稳定,需要开发钝化技术,以提 高 SiC/SiO2 界面质量。
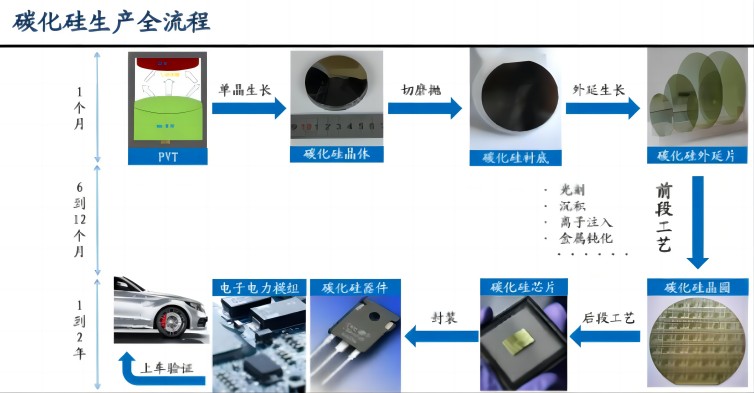
|