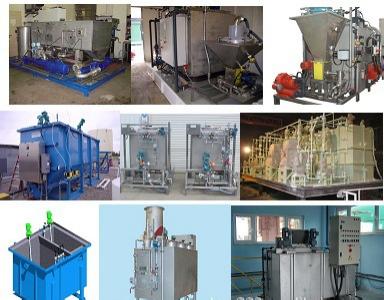
1.用药地点:对于各种污水厂的混凝、沉淀而言,通常需要投加PAC、PAM完成胶体颗粒的混合脱稳、絮凝沉淀过程,同时还伴随着磷的去除(并不一定完全是磷的沉淀反应去除,可能胶体作用去除的比重更大),一般PAC投加量20-50mg/L,PAM投加量为1-2mg/L;对于给水厂而言,有的水厂可能比较担心PAM出水单体残留有毒问题,所以干脆直接不用,尤其是阳离子型的,因此只采用PAC进行混凝处理。当然了也有其它混凝剂的使用,比如PFC等,PAM相对于PAC和PFC而言,混凝过程中多了一个网捕卷扫的功能,它既是混凝剂又是助凝剂,有关PAC与PAM的详细介绍,这里就不必多说了。
对于污泥脱水,通常在脱水之前进行污泥调理,调理方法很多,这里仅以常见的化学调理为例进行介绍,污泥难以脱水主要有三个因素:难沉降性、污泥固体的强压缩性和胞外聚合物(EPS)对水的高亲和性;化学调理是通过加药引发凝聚或絮凝作用,进而提高污泥的沉降性能;原理是加入带正电基团的混凝剂,通过压缩双电层、电荷中和、吸附架桥和网捕作用使污泥胶体脱稳,添加骨架构建并增强污泥的可压缩性,释放EPS中水分或促进污泥中水分的形态转化,实现固液相分离,并通过重力沉降进一步降低污泥含水量。
2.药剂类别及特点:化学调理投加药剂包括无机混凝剂和有机高分子混凝剂。
1)无机混凝剂不宜单独用于脱水机脱水前的污泥调理,原因是形成的絮体细小,压榨脱水时污泥颗粒漏网严重,固体回收率很低。有机高分子混凝剂(如阳离子PAM)可有效地形成抵抗压滤过程中剪切作用的大块絮体,适用于污水厂污泥机械脱水;一般污泥加药以后,应立即混合反应,并进入脱水机,以利于污泥的凝聚。
2)无机混凝剂适用于板框式压滤脱水,因为无机药剂调理后的污泥可产生不可压缩的晶格结构,具有良好的不可压缩性;有机高分子混凝剂适用于带式和离心式机械脱水,尤其是无机沉淀颗粒物可能会对离心机造成一定的磨损。
3)无机混凝剂种类很多,但就成本和效果而言,使用最多的是铁盐,其中FeCl3最为常用,其次是氯化硫酸铁、硫酸铁、硫酸亚铁和铝盐;铁盐是目前处理有机污泥最有效、使用最广泛的药剂。
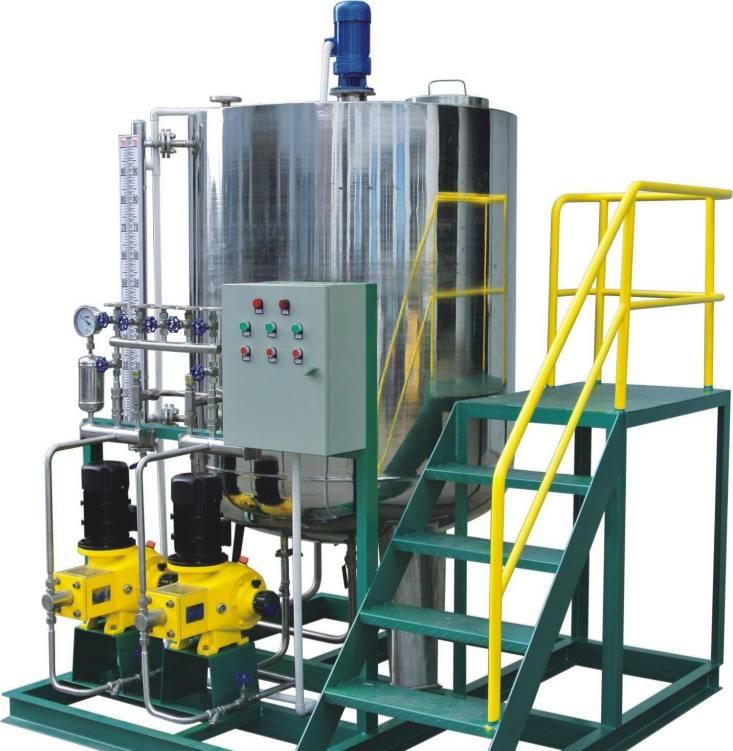
4)无机混凝剂,价廉易得,但调理效果受pH的影响大,投加量较大,一般为污泥干固体重量的5-20%,导致滤饼质量增加15-30%,而且会显著降低污泥的肥效和热值,当污泥最终处置方式为土地利用或焚烧时,采用无机混凝剂进行污泥调质会产生不利影响。当污泥采用焚烧方式处置时,脱水过程应严格控制三氯化铁等含有氯离子药剂的投加量。在选择调理药剂时,还应充分考虑调理药剂中的重金属含量问题。有机高分子混凝剂,如阳离子PAM,其用量通常为污泥干固体重量的0.1-0.5%,它很少产生额外的污泥质量,如果脱水泥饼用于焚烧,热值不会有所下降。它还能和带负电的溶解物进行反应生成不溶性盐,经其调理脱水后的污泥水无色透明,泥水分离效果良好。
3.调理分类:根据出泥泥饼含水率而言,分为一般调理和深度调理,类似于一般脱水(泥饼含水率<80%)与深度脱水(泥饼含水率<60%)。
1)简单调理:单纯为了实现泥饼含水率<80%,后续把泥饼拉去污泥处理中心进行深度处理,一般就采用纯粹的阳离子PAM混凝了,之后直接上脱水设备,如带式脱水机、叠螺式脱水机、卧螺式离心脱水机,这三个比较常见;需要注意的是阳离子PAM加药的方式,带式机可在脱水机前采用管式混合器混合后进入,叠螺式前自带混合槽,进行短暂混合后直接进入脱水机,卧螺式可直接将PAM加注至进口处;PAM用量通常为污泥干固体重量的0.1-0.5%,投加浓度宜为0.1-0.3%,采用由干粉投加系统、进水分配系统、组合式三联箱体、自控系统等组成的一体化PAM投加系统进行投加。
2)深度调理:深度调理就是在简单调理并进行污泥浓缩后,更进一步的调理,这里需要注意的是,深度调理之前是污泥浓缩,不是污泥脱水,如果前面进行脱水了,后面可能还要稀释。尽量保证深度调理前的污泥含水率在92-98%之间,如果含水率低,则会影响深度调理过程的传质效果和污泥的流动性。对于外来脱水污泥,调理前应稀释至适宜含固率,稀释用水宜采用中水或者滤液,也可采用自来水。部分污泥深度脱水工程同时处理高含水率污泥(含水率95%以上)和外运来的脱水污泥(含水率80%左右),也可采用高含水率污泥稀释脱水污泥;深度调理最常用的调理药剂就是FeCl3和石灰(生石灰或熟石灰)了,多价金属盐和石灰的使用优于其它调理方法,因为两者的结合可以更好地调理质量差异极大的污泥。EPA指南中关于铁盐投加量建议值为污泥干固体重量的2-5.3%,石灰(CaO)为7.5-27.7%,且宜先投加铁盐,后投加石灰。《城镇污水处理厂污泥深度脱水工艺设计与运行管理指南》中铁盐投加量宜为污泥干重的6-15%,石灰投加量宜为8-40%。
4.FeCl3作用:FeCl3溶液水解过程可形成带正电荷的可溶性铁络合物,进而中和带负电荷的污泥固体,从而使污泥聚集脱稳聚集。FeCl3还与污泥中的碳酸氢盐碱度反应,形成作为混凝剂的氢氧化物,如下:
2FeCl3+3Ca(HCO3)2→2Fe(OH)3+3CaCl2+6CO2
FeCl3适用的pH范围广,但腐蚀性较强,且固体产品易吸水潮解,不易保存。工业用FeCl3溶液质量浓度不低于38%。
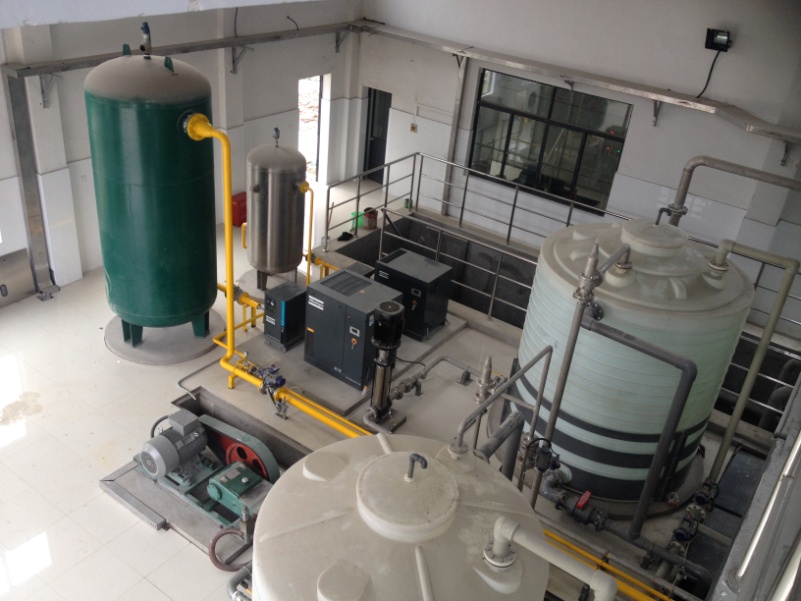
5.石灰作用:对石灰作用的理解主要源自石灰稳定这一块儿的内容,如下:
1)气味控制:投加石灰后的污泥pH值很高,从而可以消除或抑制产生恶臭气体(H2S)的微生物的生长。随着污泥pH值的升高,H2S形式的总硫化物的比例从50%(pH=7)下降到至0附近(pH=9),pH>11时,几乎没有臭气,但pH有所下降的话,气味通常会重新产生,一般pH需保持在12.0以上30分钟才能有效抑制臭气的产生。
2)减少病原体:当经过石灰处理至pH=12.0时,污泥中病原体的数量得到有效减少,石灰稳定使总大肠菌群、粪便大肠菌群和粪便链球菌的浓度降低了99.9%以上。
3)钝化重金属离子:投加石灰后的污泥呈碱性,可以结合污泥中的部分金属离子,钝化重金属。
4)改善污泥的脱水性能:当使用石灰调节时,污泥比阻降低了大约四倍。石灰浆可以稀释污泥浓度,并导致污泥中一些挥发性成分逃逸至大气中。污泥蛋白质的水解和氨基酸的破坏都是通过与强碱反应而发生的,可能会导致此过程形成的氨、水和低分子量胺或其它挥发性有机物逃逸至大气中。
5)对于污泥化学调理而言,石灰通常与铁盐搭配使用,尽管石灰对胶体有一些轻微的脱水作用,但其对污泥调理的主要作用是它可以控制 pH 值、减少气味并进行消毒,CaCO3由石灰和碳酸氢盐反应形成,提供颗粒状结构,增加污泥孔隙率并可降低污泥可压缩性。
6.石灰种类:石灰主要有生石灰和熟石灰两种。生石灰很少直接应用于污泥处理,通常它通过熟化反应转化为熟石灰,在熟化过程中,较粗的CaO颗粒破裂,分裂成细小的Ca(OH)2颗粒,这些较小的颗粒具有较大的总表面积和较高的反应活性。
生石灰和熟石灰都会与CO2反应,生石灰还会在潮湿环境下会发生潮解,这将导致两个问题:石灰功效下降,因为反应产物CaCO3不能有效提高pH值;潮解将导致石灰结块,进而影响到石灰的熟化和进料。因此,石灰储存、熟化和进料设备应尽可能密封,以防止石灰与大CO2和水蒸气接触,这在使用生石灰时要尤其注意,因为其与外部环境接触时变质更快。
7.石灰投加:将干的生石灰直接添加到污泥中,其优势是消除了消解设备和并产生大量热量,可减少病原体数量,并通过温度升高而加快水的蒸发,进而提高脱水速度。而EPA建议污泥调理时,采用熟石灰并以石灰乳形式注加至污泥池内,石灰乳可以一次投放至污泥中,也可以通过进料泵计量加入到池中,这样的话会更均匀。
输送石灰乳液管道流速不宜低于1.0m/s,以防止杂质在管道内沉积,并宜在管道上增加冲洗及放空接口,便于疏通。为实现药剂与污泥的最佳混合,可采用浓度为50-80g/L的石灰浆,以将药剂更容易地分散到污泥中。
8.调理池
1)调理池的搅拌速率和频率决定了调理剂与污泥反应的时间和充分程度,影响调理效果的好坏,搅拌时间过长、强度过大会降低调质后污泥的过滤性能,一般来说,铝盐、铁盐、石灰等无机药剂与污泥的反应时间不宜小于0.5h。
2)实际工程中应针对调理后的污泥特性提供优化的搅拌参数,能保证污泥与药剂充分混合,污泥在调理池中不发生沉积。调理过程中应搅拌,搅拌器应采用立式安装,电机和减速机安装于调理池顶,桨叶可采用双层桨叶,搅拌功率宜为150-300W/m3,但不宜过高。
3)若调质后储存过久,其过滤性能也会变差,特别是没有经过石灰充分处理的新鲜污水污泥,其过滤性能很可能变得更差,调理后的污泥宜在6h内进入压滤机。
4)输送絮凝污泥时,要避免絮体遭到破坏,避免采用离心泵建议采用螺杆泵。
9.总结:
1)板框压滤机一般用在了污泥的深度处理上,在前处理完成较好的情况下,其泥饼含水率最低(<60%)。
2)简单脱水一般只投加阳离子PAM进行调理,无机的也不合适。深度脱水的后续药剂投加一般采用FeCl3+Ca(OH)2,现也会看到PFC替代FeCl3的方案。
3)药剂的投加量还是以实际调试为准,给出的数据仅供参考。
4)关于深度处理泥饼增加量:得利满指南中介绍FeCl3投加量的60-70%会保留在泥饼中;Ca(OH)3投加量的80-90%会保留在泥饼中,其余则溶解于滤液中排出。EPA指南中则均以投加量的100%保留在泥饼中来考虑增加的泥量。
5)其实一直在想,为了达到<60%含水率,能不能一步到位,否则真是折腾,前面浓缩弄得太好,后面还可能需要稀释来保证深度处理前的化学调理效果。应该有这样的脱水设备了,一步到位,储泥池+化学药剂调理池+深度压榨脱水(<60%),否则可能会造成混凝剂巨大浪费,且处理流程过长,占地方,还费钱。
6)污泥处理中大规模的使用FeCl3和石灰这两种材料,可能会对环境造成巨大的伤害,虽然污泥脱水过程中,采用两者化学药剂可能造价上最低,性价比最高;但FeCl3的生产会产生大量废酸,是一种有污染性的化工原料,石灰石的焙烧,属于重污染,高能耗的工业,两者的生产可能会对环境产生较大的不利影响;目前来看好像还没有更好的替代品,这一点从EPA和IWA的官方指南也可以看出;通常它通过熟化反应转化为熟石灰,在熟化过程中,较粗的CaO颗粒破裂,分裂成细小的Ca(OH)2颗粒,这些较小的颗粒具有较大的总表面积和较高的反应活性。
|