污水处理厂芬顿工艺即芬顿氧化法可作为废水生化处理前的预处理工艺,也可作为废水生化处理后的深度处理工艺,芬顿氧化法主要适用于含难降解有机物废水的处理,如造纸工业废水、染整工业废水、煤化工废水、石油化工废水、精细化工废水、发酵工业废水、垃圾渗滤液等废水及工业园区集中废水处理厂废水等的处理。
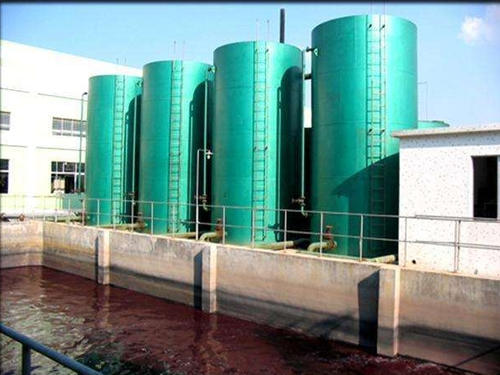
1、芬顿反应原理:1893年,化学家Fenton HJ发现,过氧化氢(H2O2)与二价铁离子的混合溶液具有强氧化性,可以将当时很多已知的有机化合物如羧酸、醇、酯类氧化为无机态,氧化效果十分显著;但此后半个多世纪中,这种氧化性试剂却因为氧化性极强没有被太多重视,但进入20世纪70年代,芬顿试剂在环境化学中找到了它的位置,具有去除难降解有机污染物的高能力的芬顿试剂,在印染废水、含油废水、含酚废水、焦化废水、含硝基苯废水、二苯胺废水等废水处理中体现了很广泛的应用;当芬顿发现芬顿试剂时,尚不清楚过氧化氢与二价铁离子反应到底生成了什么氧化剂具有如此强的氧化能力;二十多年后,有人假设可能反应中产生了羟基自由基,否则氧化性不会有如此强;因此以后人们采用了一个较广泛引用的化学反应方程式来描述芬顿试剂中发生的化学反应的原理和过程:Fe2++H2O2→Fe3++(OH)-+OH·芬顿氧化法是在酸性条件下,H2O2在Fe2+存在下生成强氧化能力的羟基自由基(·OH),并引发更多的其他活性氧,以实现对有机物的降解,其氧化过程为链式反应;其中以·OH产生为链的开始,而其他活性氧和反应中间体构成了链的节点,各活性氧被消耗,反应链终止;其反应机理较为复杂,这些活性氧仅供有机分子并使其矿化为CO2和H2O等无机物;从而使Fenton氧化法成为重要的高级氧化技术之一。
2、进水水质要求:
1】. 芬顿氧化法的进水应符合以下条件: a)在酸性条件下易产生有毒有害气体的污染物(如硫离子、氰根离子等)不应进入芬顿氧化工艺单元;b)进水中悬浮物含量宜小于200mg/L;c)应控制进水中Cl-、H2PO -、HCO3 -、油类和其他影响芬顿氧化反应的无机离子或污染物浓度,其限制浓度应根据试验结果确定。 2】.芬顿氧化法进水不符合条件时,应根据进水水质采取相应的预处理措施:a)芬顿氧化法用于生化处理预处理时,可设置粗、细格栅、沉砂池、沉淀池或混凝沉淀池,去除漂浮物、砂砾和悬浮物等易去除污染物;芬顿氧化法用于废水深度处理时,宜设置混凝沉淀或/和过滤工序进行预处理;b)进水中溶解性磷酸盐浓度过高时,宜投加熟石灰,通过混凝沉淀去除部分溶解性磷酸盐;c)进水中含油类时,宜设置隔油池除油;d)进水中含硫离子时,应采取化学沉淀或化学氧化法去除;进水中含氰离子时,应采取化学氧化法去除;e)进水中含有其他影响芬顿氧化反应的物质时,应根据水质采取相应的去除措施,以消除对芬顿氧化反应的影响;芬顿氧化法用于生化处理的预处理时,若进水水质水量变化较大,芬顿氧化工艺前应设置调节池。
3、芬顿的影响因素
1】、温度:温度是芬顿反应的重要影响因素之一,一般化学反应随着温度的升高会加快反应速度,芬顿反应也不例外,温度升高会加快·OH的生成速度,有助于·OH与有机物反应,提高氧化效果和COD的去除率;但是对于芬顿试剂这样复杂的反应体系,温度升高,不仅加速正反应的进行,也加速副反应,温度升高也会加速H2O2的分解,分解为O2和H2O,不利于·OH的生成;不同种类工业废水的芬顿反应适合的温度,也存在一定差异。处理聚丙烯酰胺水溶液处理时,温度控制在30℃~50℃;研究洗胶废水处理时发现温度为85℃;处理三氯(苯)酚时,当温度低于60℃时,温度有助于反应的进行,反之当高于60℃时,不利于反应。 2】、pH一般来说,芬顿试剂是在酸性条件下发生反应的,在中性和碱性的环境中Fe2+不能催化氧化H2O2产生·OH,而且会产生氢氧化铁沉淀而失去催化能力。当溶液中的H+浓度过高,Fe3+不能顺利的被还原为Fe2+,催化反应受阻。多项研究结果表明芬顿试剂在酸性条件下,特别是pH在3~5时氧化能力很强,此时的有机物降解速率快,能够在短短几分钟内降解。此时有机物的反应速率常数正比于Fe2+和过氧化氢的初始浓度。因此在工程上采用芬顿工艺时,建议将废水调节到=2~4,理论上在为3.5时为佳。 3】、有机底物针对不同种类的废水,芬顿试剂的投加量、氧化效果是不同的;这是因为不同类型的废水,有机物的种类是不同的;对于醇类(甘油)及糖类等碳水化合物,在羟基自由基作用下,分子发生脱氢反应,然后C-C键的断链;对于大分子的糖类,羟基自由基使糖分子链中的糖苷键发生断裂,降解生成小分子物质;对于水溶性的高分子及乙烯化合物,羟基自由基使得C=C键断裂;并且羟基自由基可以使得芳香族化合物的开环,形成脂肪类化合物,从而消除降低该种类废水的生物毒性,改善其可生化性;针对染料类,羟基自由基可以打开染料中官能团的不饱和键,使染料氧化分解,达到脱色和降低COD的目的;用芬顿试剂降解壳聚糖的实验表明当介质pH值3~5,聚糖、H2O2及催化剂的摩尔比在240:12~24:1~2时,芬顿反应可以使壳聚糖分子链中的糖苷键发生断裂,从而生成小分子的产物。
4】、过氧化氢与催化剂投加量:芬顿工艺在处理废水时需要判断药剂投加量及经济性;H2O2的投加量大,废水COD的去除率会有所提高,但是当H2O2投加量增加到一定程度后,COD的去除率会慢慢下降。因为在芬顿反应中H2O2投加量增加,·OH的产量会增加,则COD的去除率会升高,但是当H2O2的浓度过高时,双氧水会发生分解,并不产生羟基自由基;催化剂的投加量也有与双氧水投加量相同的情况,一般情况下,增加Fe2+的用量,废水COD的去除率会增大,当Fe2+增加到一定程度后,COD的去除率开始下降。原因是因为当Fe2+浓度低时,随着Fe2+浓度升高,H2O2产生的·OH增加;当Fe2+的浓度过高时,也会导致H2O2发生无效分解,释放出O2。
4、工艺操作及设计:芬顿氧化法废水处理工程工艺流程主要包括调酸、催化剂混合、氧化反应、中和、固液分离、药剂投配及污泥处理系统,工艺流程示意图见图。
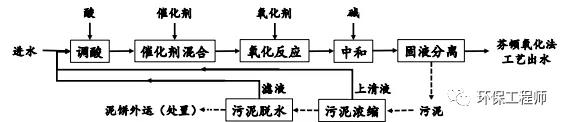
1】、调酸:根据氧化反应池最佳pH值条件要求,应通过投加浓硫酸或稀硫酸来调整废水的pH值,pH值宜控制在3.0~4.0;调酸池宜采用水力搅拌、机械搅拌或空气搅拌,混合时间不宜小于2min。浓硫酸或稀硫酸宜采用计量泵投加,采用在线pH值控制仪等自控系统自动调节投加量。
2】、催化剂混合:催化剂可采用硫酸亚铁,在催化剂混合池完成混合过程,催化剂混合池宜采用水力搅拌、机械搅拌或空气搅拌,混合时间不宜小于2min;硫酸亚铁溶液质量百分浓度宜小于30%,宜采用计量泵定量投加。
3】、氧化反应:应投加过氧化氢溶液,在氧化反应池中完成氧化反应,氧化反应池可采用完全混合式或推流式,完全混合式氧化反应池不宜少于2段,通过溢流或穿孔墙连接;氧化反应池池型应根据废水处理规模、占地面积和经济性等因素综合确定,氧化反应池采用塔式时,宜采用升流式反应器,钢结构塔体应采用不锈钢316L材质和涂衬玻璃鳞片防腐处理。塔式反应器包含芬顿试剂混合区、布水区和反应区;混合区混合速度梯度G值应不小于500s-1,布水区应配水均匀,配水孔出口流速应为1.0m/s~1.5m/s,回流比应不低于100%;塔式反应器高径比宜在1.0~5.0之间,高度应不高于15m;氧化反应池池体有效容积可按下式计算:V=Q.T式中:V—池体有效容积m3;Q—设计水量m3/h;T—水力停留时间h;氧化反应池有效面积可按下式计算:F=V/H式中:F—池体有效面积m2;H—池体有效水深m,完全混合式宜为2.5m~6.0m;氧化反应池水力停留时间应根据进水水质、组成以及出水要求,通过试验确定;用于预处理时,氧化反应池水力停留时间宜为2.0h~8.0h;用于深度处理时,氧化反应池水力停留时间宜为 2.0 h~6.0h;混合可采用水力搅拌、机械搅拌或空气搅拌,确保混合均匀,防止出现短流和死水区;芬顿氧化反应中药剂投加量与投加比例应经试验确定,在缺乏试验数据的情况下投加比例c(H2O2,mg/L):COD(mg/L)宜为1:1~2:1;c(H2O2,mg/L):c(Fe2+,mg/L)宜为1:1~10:1。
4】、中和:中和池投加碱液调整pH值至中性,碱液宜采用氢氧化钠溶液、碳酸钠溶液,不宜采用氢氧化钙溶液;当芬顿氧化法出水直接排放时,pH值应调整至满足固液分离要求和排放要求;当芬顿氧化法出水进入后续处理工艺时,pH值应调整至满足固液分离要求和后续处理工艺要求;中和池可采用水力搅拌、机械搅拌或空气搅拌,混合时间不宜小于2min;氧化反应和中和工序未采用空气搅拌时,应设空气搅拌脱气池,水力停留时间不宜小于15min,气水比不宜小于5:1。 5】、固液分离:可采用沉淀或气浮完成固液分离,若分离效果不佳可投加混凝剂或助凝剂,混凝剂宜采用聚合氯化铝(PAC),投加量宜为100mg/L~200mg/L;助凝剂宜采用聚丙烯酰胺(PAM),投加量宜为3mg/L~5mg/L;药剂种类和投加比例有条件时应依据试验确定。
6】、药剂投配:芬顿试剂、酸碱试剂、混凝剂、助凝剂等药剂的用量,应根据废水特性,经试验后确定;芬顿试剂和助凝剂的投加方式宜选择计量泵投加,并安装流量计。芬顿试剂和助凝剂投加系统应包括药剂的储存、调制、输送、计量和投加设施(备)。 投药混合采用水力搅拌、机械搅拌或空气搅拌等方式时,要求搅拌的速度梯度 G值应控制在 1000s-1~500 s-1之间。采用水力搅拌、机械搅拌或空气搅拌等方式进行化学反应或凝聚反应时,搅拌的速度梯度 G值应控制在 70 s-1~50 s-1之间,逐段减低。 7】、药剂调制:a)药剂(如硫酸亚铁、氢氧化钠、PAC和PAM等)的溶解和稀释方式应按投加量大小、药剂性质确定。溶解和稀释宜采用机械搅拌方式,也可采用水力或空气搅拌等方式;b)应依据不同溶解度、凝固点合理选择溶药浓度,硫酸浓度应保证该浓度下硫酸凝固点低于冬季最低气温(硫酸凝固点见表1);硫酸亚铁溶药浓度宜按质量百分浓度≤30%配制, 水温较低时宜按质量百分浓度≤20%配制;过氧化氢质量百分浓度宜≤30%;液碱浓度宜≤30%。若调制药品用水碱度较大导致硫酸亚铁结晶,可在溶解时加入适量硫酸以减少溶解池和投配池中的硫酸亚铁结晶沉淀;c)水力调制的供水水压应大于0.2 MPa;d)压缩空气调制可用于水量较大的废水处理厂(站)的药剂调制,曝气强度宜控制在3L/(m2·s)~5 L/(m2·s);e)硫酸溶液宜采用成品溶液,避免在污水处理厂内稀释调制;不具备成品供应条件,需现场调制时,应考虑其腐蚀性及溶解过程的放热,使用专用设备调制;f)双氧水的储存装置应远离热源、避免阳光直射。
表 不同质量分数下硫酸的凝固点(0.1 MPa)
质量分数(%) |
0 |
12.5 |
25 |
37.5 |
50 |
62.5 |
75 |
87.5 |
98 |
凝固点(℃) |
0 |
-8 |
-27 |
-70 |
-36 |
-29 |
-40 |
-14 |
6 |
8】、药剂溶解池与溶液池的容积计算a.溶液池容积按下式计算: W1=(0.2~0.3)W2;式中:W1—溶液池容积m3;W2—溶解池容积m3.b.溶解池容积按下式计算:W2=(2400xaxQ)/(100000xcxn)=(axQ)/(417xcxn)式中:a—药剂最大投加量,按无水产品计mg/L;Q—设计水量m3/h;c—溶液浓度%;n—每日调制次数,应根据药剂投加量和配制条件等因素确定,一般不宜超过3次。
5、设备与材料的选择
1】、本体建(构)筑物池体可采用钢筋混凝土结构或钢结构,处理规模较大可采用钢筋混凝土池体,处理规模较小可采用钢结构罐体;各单元建(构)筑物池体以及所采用的材料、设备与连接管道应具有相应的耐酸碱腐蚀和抗氧化腐蚀能力;钢筋混凝土池体内壁可采用涂衬环氧树脂玻璃钢防腐,钢制罐体内壁可采用316L型不锈钢材质或涂衬玻璃鳞片防腐。药剂投配系统中的溶解池及溶液池内壁可采用涂衬环氧玻璃钢、辉绿岩、耐酸胶泥贴瓷砖或聚氯乙烯板等,当所用药剂腐蚀性不强时, 可采用耐酸水泥砂浆;药剂投配系统的设备、管道应根据药剂的性质采取相应的保温或隔热措施。
2】、泵阀:废水提升泵过流部件应耐酸碱腐蚀;氧化反应池循环泵过流部件应耐酸碱、抗氧化,宜采用316L型不锈钢材质;药剂投配系统中加药泵等均应采用耐腐蚀材质;其中浓硫酸溶液加药泵过流部件可采用聚四氟乙烯、铸铁材质;双氧水溶液加药泵过流部件可采用316L型不锈钢材质;硫酸亚铁溶液加药泵过流部件可采用316L型不锈钢、聚丙烯、聚氯乙烯材质;氢氧化钠溶液加药泵过流部件可采用 304型不锈钢材质。药剂投配系统中阀门过流部件内衬材质可与相应提升泵、加药泵相符。
3】、机械搅拌机:机械搅拌机(如框式搅拌机、桨叶式搅拌机等)的功率与转速应根据工艺设计要求选用,宜采用无级变速搅拌机。机械搅拌机水下部件宜采用 316L型不锈钢材质、玻璃钢材质。
4】、管道:废水输送管道宜采用316L型不锈钢、聚乙烯、聚丙烯或聚氯乙烯材质的管路和管件;浓硫酸(98%)输送可采用聚四氟乙烯管道或其他耐浓硫酸腐蚀的管道以及与之配套的管件,过氧化氢溶液输送应采用316L型不锈钢材质管道以及与之配套的管件,其他药剂输送管道宜采用聚乙烯、聚丙烯或聚氯乙烯材质的管路和管件;药液输送管应设置必要的过滤器,防止计量泵和管路堵塞。
6、污泥的计算及处置:污泥产生量主要与水量、悬浮物浓度、有机污染物种类和药剂投加量等因素有关;因废水水质不同污泥产生量差别较大,宜通过多组试验确定污泥产量;不具备试验条件时,可按下式估算干污泥产量:TS=B×(S+K1F+K2A+P)×Q×10-6 式中:TS—干污泥总量,t/d;S—通过芬顿氧化法去除的悬浮物浓度,mg/L;K1—亚铁盐转化为污泥量的系数,取1.9,Fe2+与Fe(OH)3的换算系数;F—亚铁盐投加量,以Fe2+计,mg/L;K2—混凝阶段混凝剂转化为污泥量的系数,若采用铝盐,取1.53,Al2O3与 Al(OH)3的换算系数;A—混凝阶段混凝剂的投加量,若采用铝盐,以Al2O3计,mg/L;P—混凝阶段助凝剂(一般采用PAM)投加量,mg/L;Q—设计水量,m3/d;B—安全系数,取1.1~1.2;污泥脱水前应加药调理,投加药剂的种类和投药量应根据试验或参照同类型污泥脱水工艺的数据确定;污泥脱水机选型应根据污泥性质、污泥产量、脱水要求确定,脱水污泥含水率应满足污泥处理及处置的要求;固液分离系统分离出的污泥不应回流进入生物处理系统。脱水后的污泥应按国家相关规定进行无害化处置;列入《国家危险废物名录》的污泥和经鉴定属于危险废物的污泥,应按照有关规定贮存和处置,其他污泥应按GB18599的规定,因地制宜妥善贮存与处置。
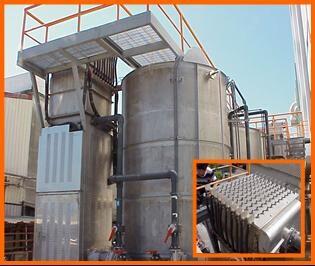
|