南方某污水处理厂提标改造后,排放标准从一级B提高至一级A标准和广东省地标两者之严者;总氮、氨氮、总磷的排放值分别比原标准降低了 25%、37.5%、50% ,而该厂提标后 的主体工艺仍然为改良AAO氧化沟,这对污水处理厂的运行管理提出很大挑战;通过污泥硝化速率分析,总氮、总磷成分检测,精确加药,跌水复氧分析及改造等措施优化工艺运行后,运行效率明 显提升,在确保水质稳定达标的同时,节约了生产成本,对同类污水处理厂的工艺优化改造具有一定的参考意义。
1、污水处理厂概况:广东珠海某污水处理厂分一、二两期建设,一期处理规模为3x104m3/d,于2010年7月正式运行;二期建设规模为5x104m3/d,二期扩建和一期提标改造同步进行,于2018年4月完成,并于6月底通 过竣工环保验收;提标扩建后该厂总设计处理规模为8 x104 m 3/d,采用的主体工艺是改良AAO氧化沟+精密过滤池,出水排放标准从(城镇污水处理厂污染物排放标准》(GB 18918—2002) 一级B标准提高至一级A标准和广东省(水污染物排放限值》(DB44/26—2001)中的第1时段一级标准两者之严者
1.1设计进、出水水质报告单
项目 |
COD |
BOD5 |
SS |
NH3-N |
TN |
TP |
pH值 |
一期设计进水水质 |
300 |
130 |
150 |
30 |
40 |
4.5 |
6〜9 |
一期设计岀水水质 |
60 |
20 |
20 |
8 |
20 |
1.0 |
6〜9 |
扩建后总的设计进水水质 |
400 |
180 |
150 |
35 |
45 |
4.5 |
6〜9 |
扩建后总的设计出水水质 |
40 |
10 |
10 |
5 |
15 |
0.5 |
6〜9 |
1.2提标后的污水处理工艺流程图

1.3工艺流程分析:AAO工艺运行管理的核心是脱氮除磷,提标后,总氮、氨氮、总磷的排放值比原标准分别降低了25%、37.5%和50%;对氨氮、总氮指标而言,只能通过生物降解;由于上游的污水收集系统为雨污合流制,雨季时进水有机浓度普遍较低,同时该厂进水中有约20% - 30%的工业废水,且以化学制药和电镀行业废水为主,该类废水中重金属及复杂难降解有机物等有毒有害物质含量高,由于监管不严,企业时有违规排放,对该厂的生物系统产生冲击和毒害,造成生物池污泥活性低,絮凝性长期较差;偶尔会有进水总氮和氨氮超标波动的情况,所以脱氮是该厂提标后工艺运行的控制难点;此外提标后总磷排放标准降至0.5mg/L,由于该厂进水中的总磷浓度长期较高,为了确保该项 指标稳定达标,需要投加大量的除磷药剂(聚合氯化铝,PAC);一方面成本增加很大,另一方面也会对生物系统产生影响;所以如何在保证总磷排放达标的前提下做到精确加药,也是提标后运行管理的一个难题。
2、工艺运行优化
2.1总氮成分及污泥硝化速率分析:该厂上游管网服务片区的工业企业有制药厂和 线路板厂,自投产以来长期存在进水总氮、氨氮波动 较大的情况,对工艺出水达标造成影响;提标后,总氮和氨氮指标从20&8 m/L分别降至15&5 m//L,如何确保工艺脱氮的长期稳定性和去除效率 是该厂提标后面临的第一大难题。针对该问题,该 厂坚持对进、出水氮的成分进行长期分析,结果分别见图2、3。
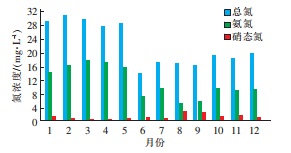
图2 2018年月度进水氮成分分析 图3 2018年月度出水氮成分分析
通过分析可知,2018年进水总氮年均值22.6m//L,氨氮年均值为11.6m/L,氨氮占比51.3%,硝态氮为1.46m/L,占比6.5%;出水总氮年均值为9.77mg/L,氨氮年均值为1.16mg/L,占比11.9%,硝态氮为4.66m//L,占比47.6%;根据以上分析可知,经过工艺处理后,有机氮的占比基本不变,约为40%,出水有机氮含量相对较高,也证明该厂进水中部分工业废水所含难降解有机氮成分高,在日常的运行管理中需要特别关注;氨氮和硝态氮在总氮中的占比发生了调换,基本符合氮在AAO工艺处理中的变化规律;通过对氮成分进行日常分析,可为工艺调控提供精准科学的指导,尤其是在进水不可降解有机氮 浓度较高时,应及时降低负荷,确保系统稳定运行。 此外,该厂在进水氨氮、总氮达到40m/L左右时,即使DO、ORP等过程参数控制正常,出水数值经常会有一个缓慢稳定升高的过程;提标后这种轻微的波动也会影响水质达标;针对这个问题该厂参考了陈卫等的硝化速率测定方法:取好氧池污泥混合液4L加自来水至8L并加入1.2gNH4C1和1gNaHCO*,在一定转速下反应搅拌并曝气,控制DO为3~5mg/L,在不同的时间点测定混合液中的硝酸盐浓度,得到硝化曲线后,进行线性回归,得到曲线斜率,再根据污泥浓度推算出硝化速率,一期、二期污泥硝化速 率分析分别见图4、5;根据测定的硝化速率,结合该厂一、二期好氧段的水力停留时间(9.3h和11.5h),经核算在该分析周期内二期工程可以消解的氨氮值为44.4mg/L。根据硝化速率的分析,可得出不同阶段污泥的硝化性能,在进水氨氮、总氮发生异常时可以进竹基于污泥硝化性能的精确水量调控,确保水质稳定达标,一、二期生物池硝化速率分析见表2
一、二期生物池污泥硝化速率分析(表2)
项目 |
斜率 |
硝化速率 |
反应时间/min |
MLVSS |
MLSS |
一期 |
4.662 9 |
3.54 |
60 |
1 318 |
3 816 |
二期 |
3.921 4 |
2.62 |
60 |
1 495 |
3 622 |
在2019年工艺优化调控中坚持运用以上总氮控制原理和方法,2019年全年进水BOD平均值为93.5mg/L,进、出水总氮分别为18.0、5.88mg/L,年平均BOD5/TN为5.2,去除率为67.3%,具体数值见表3。2018年全年进水BOD5平均值为111mg/L,年平均BOD/LN为4.92,总氮去除率为56.8%;对比发现在脱氮条件基本稳定的情况下,2019年的总氮降解率同比升幅较大。
2.2 2019年月平均进水BOD)及进、出水总氮值分析
2019年月平均进水BOD)及进、出水总氮值(表3)
项目 |
1月 |
2月 |
3月 |
4月 |
5月 |
6月 |
7月 |
8月 |
9月 |
10月 |
11月 |
12月 |
进水BODs |
110 |
95.5 |
102 |
113 |
78.2 |
89.3 |
85.5 |
87.6 |
66.0 |
87.8 |
110 |
96.9 |
进水总氮 |
20.4 |
20.7 |
23.0 |
17.7 |
13.3 |
14.5 |
16.0 |
13.5 |
13.4 |
16.9 |
22.0 |
24.4 |
岀水总氮 |
5.82 |
5.78 |
6.33 |
4.83 |
3.92 |
5.93 |
6.64 |
6.00 |
5.93 |
5.44 |
5.84 |
8.16 |
2.3跌水复氧改造:跌水复氧是污水处理厂普遍存在的一个现象,主要发生在预处理单元,该现象会加快进水中快速碳源的消耗,进而对系统的脱氮除磷效率产生不利影响;以脱氮为例,基于反硝化理论,不考虑生物同化作用下,去除1gNO3--N需要消耗2.86g COD;提标后总氮排放指标降至15 mg/L,南方地区的污水处理厂在雨季时段进水有机浓度普遍很低,为确保总氮达标,需额外投加碳源(乙酸、乙酸 钠等),对跌水复氧进行分析研究和改造,对工艺优化、成本节约具有非常重要的意义;经初步分析发现,该厂曝气沉砂池出水口末端 存在明显的跌水复氧;为此对跌水前后和不同跌水高度内的溶解氧变化进行分析,结果见图6。
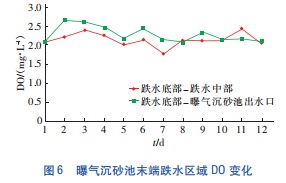 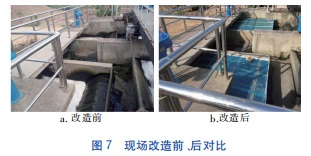
根据分析可知,从跌水区底部到中部的DO平 均增加值为2. 14 m//L,而跌水区底部到曝气沉砂 池出水口处的DO增加平均值为2.29 m//L;且跌水 复氧增幅在整个分析周期内比较接近,变化趋势也 很稳定,根据该结果可知跌水复氧主要发生在跌水底部区域;目前关于跌水复氧的原理普遍认为是跌水改变了区域的空气交换流态,基于此该厂进行了改造尝试,通过在沉砂池出水口区域贴近水面处加装盖板,阻断、改变跌水复氧区域的正常空气交 换,以降低复氧值。改造采用普通的废旧遮阳板,四周用玻璃胶密封,同时在盖板上开小孔,便于DO仪探头测量,现场改造前、后对比见图7;改造完成后,立刻进行DO值变化测定,以验证改造效果(见图8);经过20 d的测定,改造后曝气沉砂池出水口和跌水底部的DO差值明显减小,且数值变化规律一致。需特别说明的是,图8中后半 段DO值明显升高,是因为外部污水管网改造,造成 该段时间进水量降低,且进水中砂砾含量多。为避 免后续工艺影响,加大了沉砂池的曝气强度,导致前 段进水的DO值明显升高。经检测,该段分析周期内曝气沉砂池出水DO 值为3. 61 mg/L,跌水底部DO平均值为4.32mg/L,增加约0.71 mg/Lo跌水复氧增加值从2.29 mg/L 降至0.71 mg/L,通过此次改造直接节省COD约 1.58mg/L,说明此次跌水区域的改造达到了预期效 果;基于这种原理,对曝气沉砂池的设计曝气量进 行了调整,在进水中含砂量较低时,及时降低罗茨风 机的工作频率,确保曝气充氧量尽可能低,减少进水 中快速碳源的消耗。
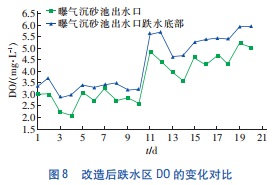 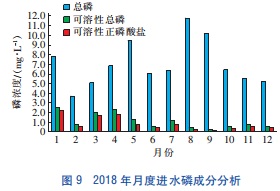
以该厂8x 104 m3/d的设计规模计算,将节省的COD以乙酸计,改造后每年至少可节省的乙酸费用约为40万元,且理论上可提高系统脱氮量1.1mg/Lo该厂根据以上改造优化原理,对提升泵房出 水管排口跌水进行了类似改造,以上项目实施前,该 厂每年为确保总氮稳定达标需额外投加乙酸约200 万元,改造后可节省20万元/a,效果显著,该方法 简单实用,对南方地区进水有机浓度较低、进水预处 理段存在明显跌水复氧,碳源不足污水厂的类似改 造具有借鉴意义,也为污水厂内部碳源的开发利用和工艺优化探索了新的方向。
2.4进水总磷的成分分析及药剂投加:由于该厂进水中含有部分工业废水,生物除磷的效果较差,提标后总磷的浓度从1mg/L降至0.5mg/L,因此对总磷的达标去除主要通过投加PAC;根据相关研究,化学辅助除磷可以采用前置、后置和同步投加,该厂采用常规后置投加,投加点为生物池好氧区末端;但是该厂2018年全年进水总磷 平均值为7.08 mg/L,超过了设计进水浓度。按照全部总磷通过化学除磷控制,且出水内控指标为0.4 m//L以下,理论投加比1:1计算,至少需要投加液体PAC(有效含量10))165m//L才能保证总磷达标。通过对进水磷成分不同形态占比进行分析(见图9),全年内进水总磷中可溶性总磷的年平均浓度仅为1.09m/L,正磷酸的年均浓度为0.83m/L,进水总磷中可溶性总磷占15., , SPAN>4),正磷酸盐占 11.7%,可溶性总磷以正磷酸盐为主,占比达到76.1%。基于进水总磷的不同形态比例分析,发现该厂进水总磷以不可溶解的悬浮形态总磷为主,进水可溶性总磷中复杂形态有机磷等的比例较低,通过投加常规PAC,可以保证出水达标;同时根据进、出水正磷酸盐含量进行加药量控制,2018年该污水厂 平均加药量仅, 为114mg/L,且出水总磷值在6月份通过环保验收后,可以稳定达到0.3mg/L以下(见图10)。
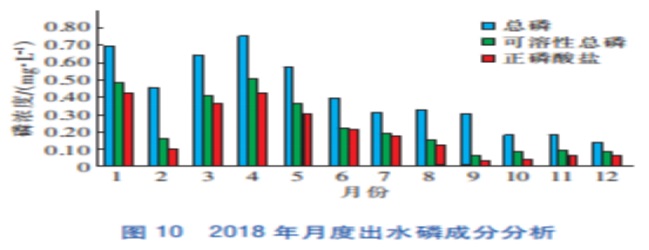
经初步计算,通过基于正磷酸盐含量的精确加药,该厂2018年节约PAC投加费用约135万元;此外根据出水总磷的形态分析可知,出水总磷 中可溶性总磷占56.9%,正磷酸盐占47.0%,正磷酸盐出水年均浓度为0.2 mg/L;各形态磷的占比趋势与进水一致,但比例稍有降低,说明基于形态分 析的总磷控制和精确加药是完全合理可行的,同时也为未来总磷更加严格排放标准的实施,深度处理工艺的科学选择打下了良好的基础。
3、, STRONG>结语:当前污水厂排放标准从一级B到一级A的提标工程在全国各地已经铺开,提标的工艺主体以常规生物处理加深度过滤为主。对污水处理而言,生产运行核心仍然是做好工艺脱氮除磷的管理,更加严格的标准也要求从业者必须转变认识,从粗放式经验式的管理向科学化、精确化的理念转变;在提标扩建后,出水排放标准压力越来越大的情况下,该厂从总氮、总磷成分分析,污泥硝化速率检测,精确 加药,跌水复氧改造方面优化工艺运行,在确保水质 稳定达标的同时,节约成本,对同类污水厂的工艺优化和效率提升具有一定的参考意义。
|