
2、关键零部件国产化进展良好
1)和锂电、光伏产业相似,氢燃料电池走向大规模市场化的主要路径是降低成本。根据华经产业研究院数据,氢燃料电池成本构成中,电堆是最大构成部分,占比约60%;在电堆成本构成中,催化剂、双极板和交换膜是主要成本来源,占总燃料电池成本比例分别为23%、16%和8%。
2)当前,氢燃料电池系统的降本主要有两条路径,一是规模效应带来的单位成本下降,二是零部件国产化替代。
3)近年来,燃料电池系统装机增速较高,规模效应逐步显现。根据东兴证券研报,2017年至2023年,中国燃料电池系统年装机功率由37.8MW提升至734MW,6年CAGR为64%。另据中国汽车战略与政策研究中心(以下简称“中汽政研”)7月发布的《“万辆百站”燃料电池汽车示范大数据报告》,我国燃料电池示范车辆已突破1万辆,累计纯氢运行里程2.35亿公里。在政策支持下,当前我国燃料电池系统成本已降低至2000-2500元/kW,较示范前降低了80%以上。
4)关键零部件方面,电堆、空气压缩机、膜电极、氢气循环系统、双极板等五项零部件国产化率已经超过80%,已经打破了国外技术垄断,在部分关键技术和产品应用方面达到国际领先水平。
5)亿华通(688339.SH)是中国燃料电池领域的龙头企业,在国产化降本方面具有丰富经验。在接受第一财经采访时,亿华通常务副总经理于民表示,中国的燃料电池产业起步较晚,公司沿循“整车动力系统-发动机-电堆-双极板&膜电极”的技术路线,逐步进行产品和设备的开发,以及产业链的打通,从而实现了零部件的国产化替代。
6)目前,国产化已经取得了良好进展。以空压机为例,早期进口空压机单价在10万元左右,目前国产空压机降到了1万元,降幅高达90%,甚至吸引了丰田等国外燃料电池厂商前来采购。于民认为这带来了两方面收益,其一是促进了燃料电池的市场推广,其二是避免了受到国外技术专利限制。
7)但少数零部件进口依赖度仍然较高。于民表示,目前碳纸、质子交换膜、催化剂的进口比例分别为80%、93%、98%,后续在这三个环节仍需要加快国产化进程。
8)相关数据显示,国内90%的已运营燃料电池车使用进口催化剂。海外催化剂供应商主要包括日本田中贵金属、英国庄信万丰、比利时优美科,国内催化剂生产厂商包括贵研铂业(600459.SH)、中自科技(688737.SH)等。在质子交换膜领域,美国戈尔占据超八成市场份额,国内生产厂商包括东岳集团、东材科技、泛亚微透、万润股份等。气体扩散层主要材料是碳纸,该领域全球生产厂商数量较少,主要为日本东丽、美国AvCarb、德国SGL,国内生产厂商有通用氢能、金博股份(688598.SH)、江苏天鸟等。
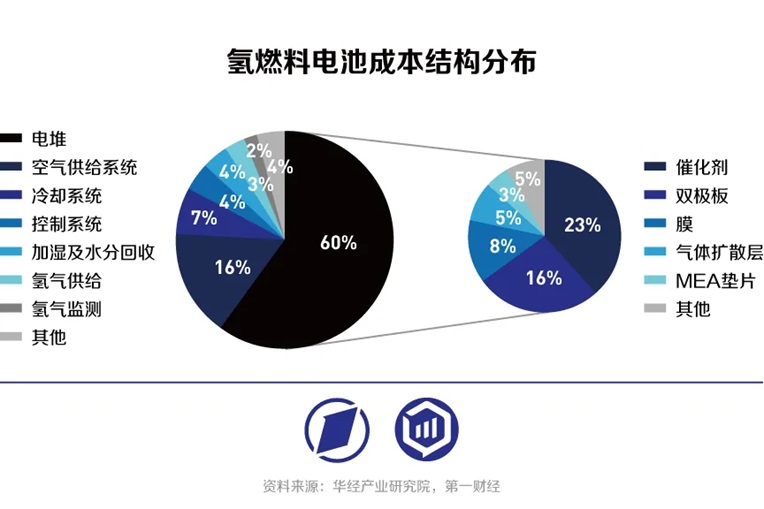
|