3)粉尘来源只考虑三个方向,设备、环境和人;设备是粉尘来源最大可能的,车间多是物流线运输,在摩擦的过程中会对表面进行磨损,而车间设备很多是不锈钢涂层,表面是Cr或者Ni合金,这类粉尘在电池制造中混入了卷芯。
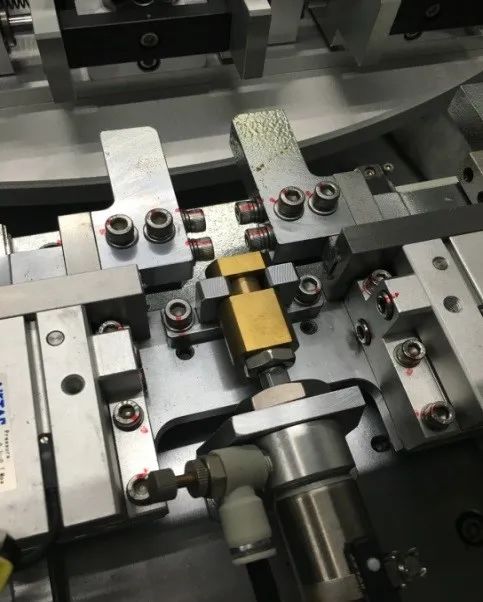
4)还有一些地方比如辊压和制片的分切环节、制片的激光切环节、卷绕的极片分切环节、后面的极耳焊接盖板焊接环节等,这些在制造过程中会产生大量的粉尘,如果除尘不及时,有可能会导致这些颗粒落入到极片和卷芯中。
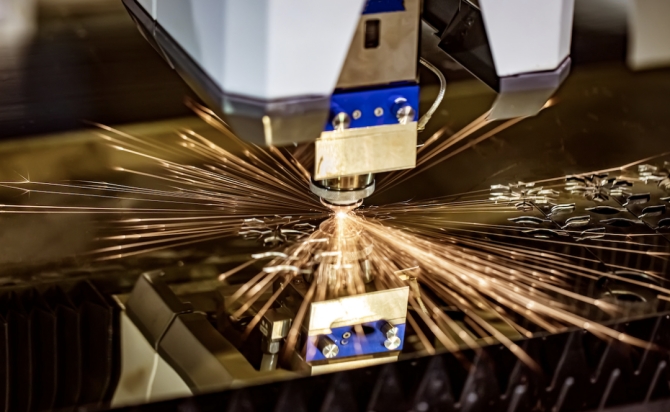
5)故而生产过程中,要做好设备的清洁度管理。曾经做过产线设备使用物质的调查,早期很多设备还有铜、锌等材质或者涂层,故而后面和设备签订技术协议时候,设备材质也考虑进去,尽可能少的使用一些禁用物质。
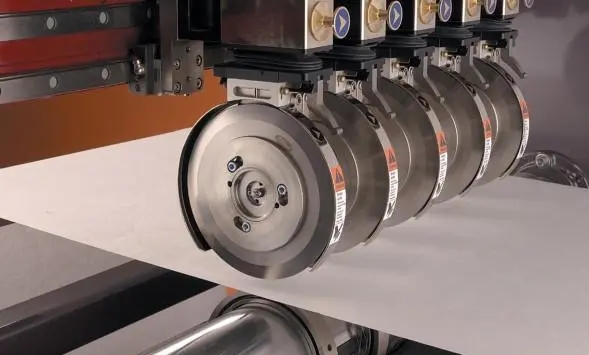
6)环境主要考虑浮尘,车间设备、钢结构、地面等产生的粉尘可能会在带动下漂浮在空气中落到电池极片、卷芯表面,现在车间都有洁净度要求,装有空气过滤设备,10万级,5万级能够满足车间的要求即可。
7)此外这里要特别提到一种情况,便是换型的控制,大家都知道,有些时候电池产线可能不是专用的,同一条产线会生产两个型号甚至多型号的电池(如电池组装尺寸一样,材料体系不一样,三元可以切换铁锂,同一体系配方也可能切换),在换型时候产线清理得不干净,也会有其他杂质的引入,比如三元颗粒混入到LFP中,因为双方的粒度要求不一致,对电池性能会有一定影响。
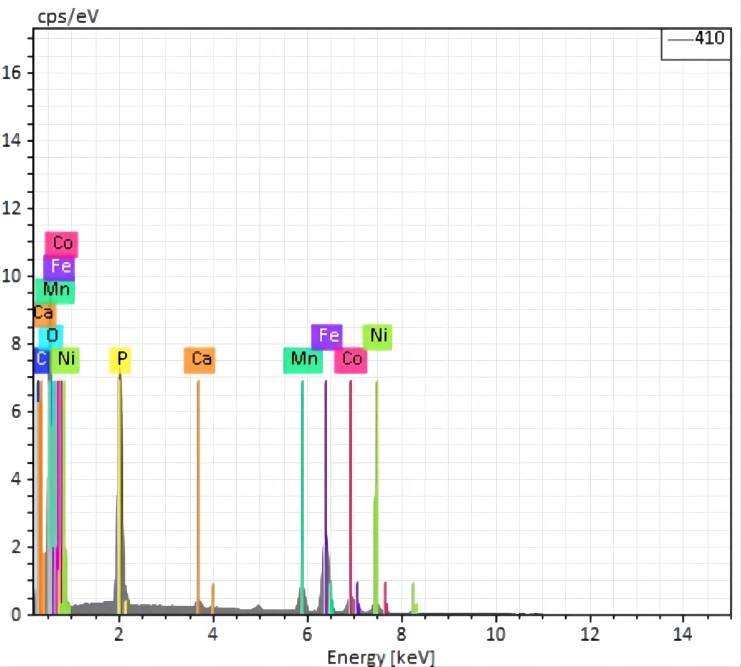
8)人员的话需严格按照着装和作业规范。虽然很多时候设备是自动化,但是人员进出,本身会携带一部分粉尘进入车间,并且在操作过程中,比如防静电服的洁净程度、手套的洁净程度也会给电池带来粉尘引入的风险。
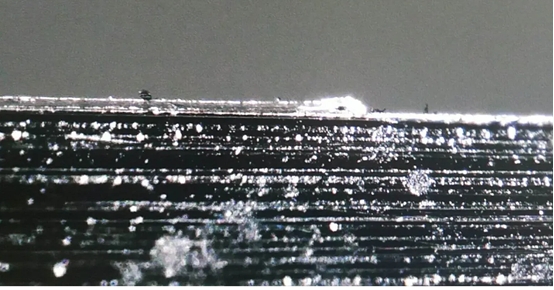
1)无论是正极还是负极,在涂布时候都是宽幅涂布,涂完后到辊压进行压实并分切成小卷,再到制片设备,使用激光裁切极耳,再到卷绕根据单个卷芯所要的长度进行裁切,这个过程需要裁切的有分切裁切、制片激光切、卷绕裁切。
2)凡是有裁切的地方,均有集流体毛刺产生的可能,虽然对毛刺的要求根据经验来看,低于二分之一隔膜厚度情况下可放行,但实际生产中是很难做到对每一卷每一个裁切后的毛刺进行监控的,一旦存在一些较长毛刺,以及一些平行于极片的毛刺,在某些情况下会刺穿隔膜,势必会造成电池内部短路,自放电率增加。故而对切刀和裁切工艺的控制需要进行监控。
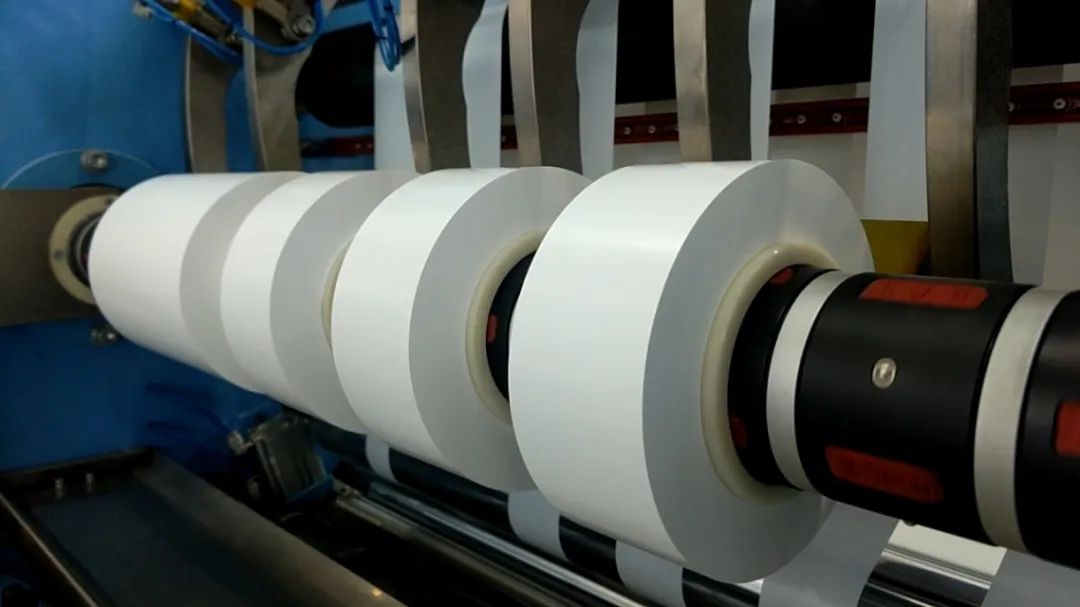
3)按照汽车行业相关经验,切刀在最初的使用时是不稳定的,故而计算切刀的设备能力时都不以新切刀的使用为前提,使用一段时间后
会趋于稳定,然后稳定性逐渐下降直到后面磨损厉害报废;此外,裁切时候极片两端承载着一定的拉力,以及与辊之间的压力,会干扰
切刀的稳定性,故而裁切工艺控制也需要监控。
4)此外有研究表明,集流体端面金属屑,即裁切后在集流体边缘的金属屑,对电池的自放电性能也有一定的影响。
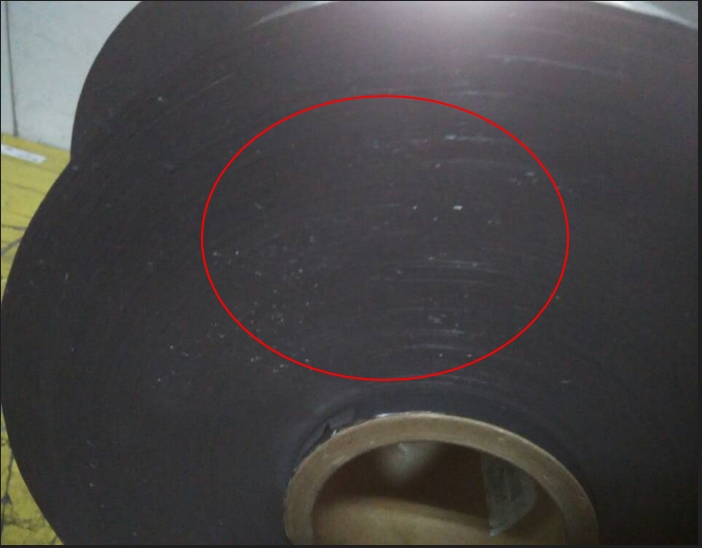
5)就方形电池来说,无论是在注液,还是在化成工序,为了确保内部电解液浸润以及化成过程中产气的排出,都会间断性对电池进行抽
真空,在抽真空的过程中,因切刀裁切导致的端面铜屑或者其他引入的金属屑,会在抽真空的过程中被带到极片和隔膜之间,且颗粒越
小,越能随着排气通道被吸入到极片和隔膜之间。
6)进一步的这种铜屑杂质在电解液作用下,在正极氧化形成离子并在负极还原析出,最终可能会穿透隔膜,造成微短路,从而导致电池
自放电异常,进一步的跑到正极和隔膜之间的金属杂质和跑到负极和隔膜之间的金属杂质,对电池自放电的影响情况也存在一定差异,
跑到正极和隔膜之间的金属杂质,对电池自放电的影响更大。
4、 隔膜缺陷对自放电的影响:隔膜本来的功能是隔离正负极,如果隔膜质量出现问题,隔膜的作用不能正常发挥。隔膜一点微小的缺
陷,也会对锂电池的自放电率产生明显的影响。之前拆电池会看到隔膜缺陷,比如隔膜存在微孔,会直接导致正负极短路。
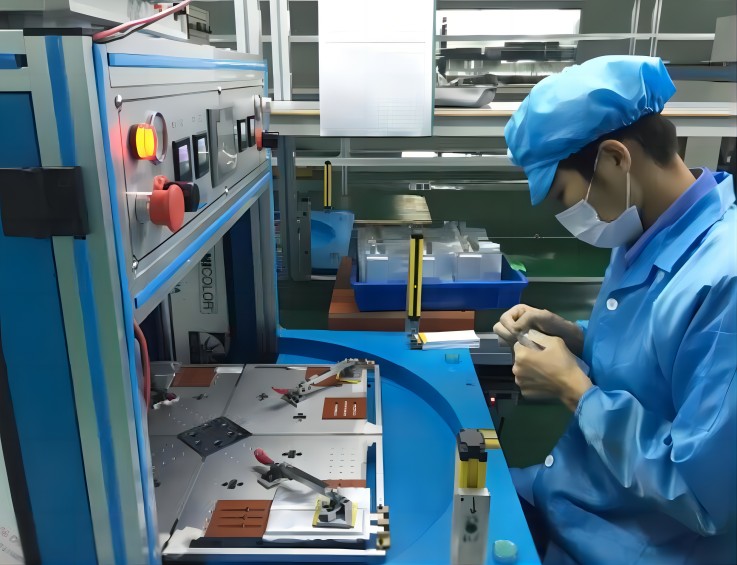